Ireland’s Museum of Cinema in Dublin and the Aleja Shopping Center in Ljubljana, Slovenia, have one thing in common – visually impressive, unique, and hard-wearing facades and interiors made with digitally printed glass. This kind of glass printing is a relatively new development, with the technology only maturing around the 2000s.
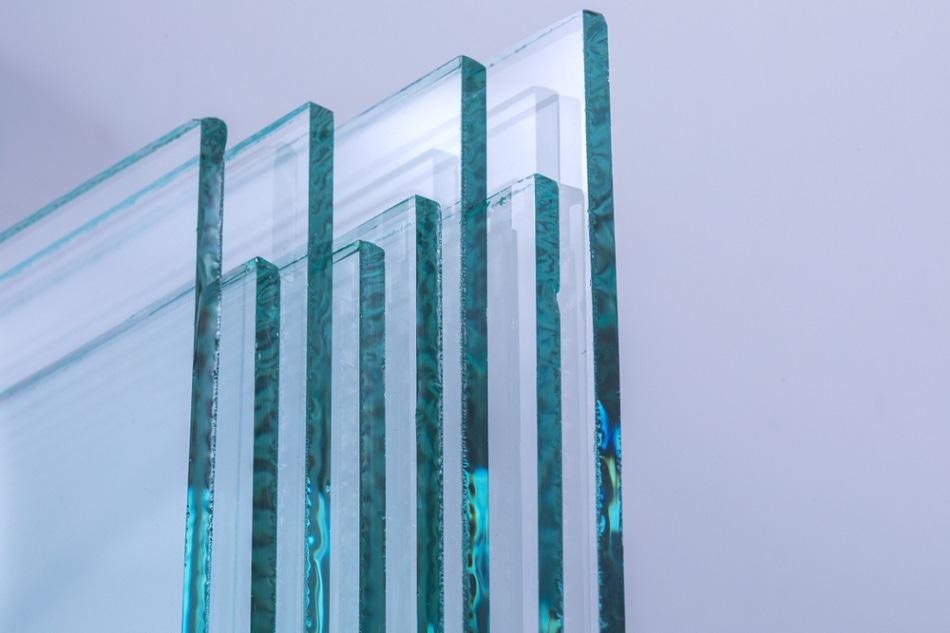
Image Credit: sichkarenko.com/shutterstock.com
Digital printing on glass applies ceramic frit to glass in a similar fashion to how an inkjet printer applies ink to paper – a thin layer of pigment sprayed directly on the substrate material in a series of small dots to create a photorealistic image. This relatively new technology means designers can apply aesthetic and practical coatings to glass used in all weathers that does not fade and that does not require any extra maintenance beyond what is needed for ordinary glass installation.
For architects and designers, the introduction of this technology represented a new blank canvas for applying printed glass in buildings. Any two-dimensional image can be applied in a hard-wearing print on glass, and manufacturers can fine-tune the print’s opacity to create stained glass effects or custom privacy barriers.
Novel uses of the technology can also make buildings perform better or more sustainably. Light diffusion and transmission can be achieved with coatings, reducing the building’s energy demand for lighting. UV-resistant coatings, heat-sink coatings, and varied color temperatures and opacities can also passively cool or warm buildings, further reducing their energy costs.
Digitally printed glass also helps buildings use glass more safely. For example, floor surfaces and stairs can be treated with anti-slip coatings, and visual warnings can be applied to windows to prevent birds from flying into them.
The FOJAB Architects-designed Parking House Hyllie in Malmö, Sweden, benefits from many of the possible advantages of digitally printed glass. It is bird-safe and also features glass panels of varying prints and opacities across its entire facade. These panels are set at different angles and printed to maximize the aesthetic and performance impact of the large glass facade.
Challenges of Printing On Glass
Glass printing has only recently matured enough as a technology for these kinds of applications to be possible. As glass is non-porous, non-absorbent, and transparent (unlike paper or fabric,) applying digital printing technologies like inkjet has remained a challenge. Silkscreen printing and digital UV printing were the two main technologies used for digital printing on glass until the 2000s, although both carried fairly significant downsides.
Silks screen printing directly applies ink onto a surface material through a mesh stencil or transfers ink from another material onto the surface in the case of screen printed transfers. Many fabric and textile applications exist for this technology, where a long-lasting transfer is possible. In the case of glass screen prints and transfers, the glass surface has to be fired for the ink to permanently fuse. This weakens the glass, making the method costly for outside applications or large panels. It is also costly and time-consuming to print images with multiple colors, which requires different coatings for each color and potentially a separate screen for each coating.
Digital Printing on Glass Machine
Video Credit: Dip-Tech Printing in Glass/Shutterstock.com
In UV printing, ink is applied to the glass surface and then subjected to ultraviolet (UV) waves to dry it and bond it with the glass. This method enables multi-colored and complex images to be printed on glass digitally for the first time, but still had its drawbacks. UV curable inks are not directly fused with the glass, which remains hard throughout the printing process. As a result, UV-printed glass is likely to fade in time, especially in external applications in buildings.
Digital Glass Printing with Ceramic Ink
A new method was developed in the 2000s using ceramic frit as ink and a deposition system similar to an inkjet printer’s series of spray nozzles on precisely controlled gantries. It resolves many of the historic challenges for printing on glass, and enables novel applications for printed glass in architecture.
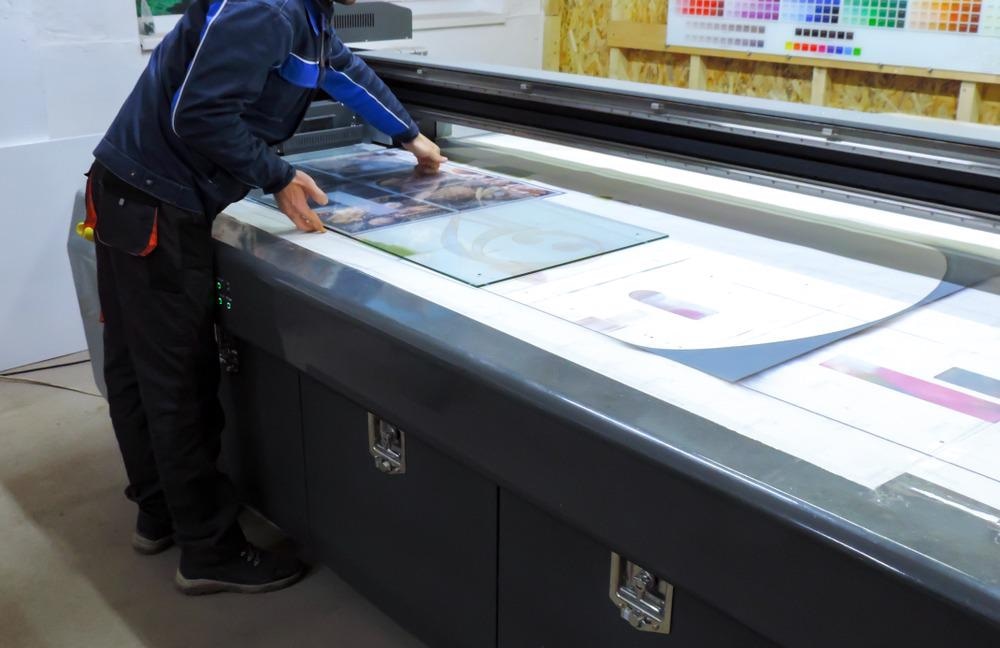
Image Credit: AsexuaL/Shutterstock.com
Like in screen printing, the glass surface has to be fired to temperature to enable the ceramic inks to fuse with the glass. The high temperature causes organic additives and binders in the ink to decompose quickly as it fuses with the glass surface and inorganic pigments and additives. Then, the glass must be smoothed out to expel all voids and cavities, ensuring a compacted, strong glass structure. Finally, any surface finishes are applied to what should be a completely bubble-free, smooth, and precisely printed glass product.
Digital glass printers are large flatbed machines with print heads positioned on gantries over the printing surface. Print heads jet ceramic frit and any additives directly onto the glass, which is fired on the print bed. The print head also immediately dries the ceramic frit when it drops it onto the glass, fixing it in place. This means that multiple colors and layers can be printed in a single pass across the fired glass.
References and Further Reading
Bergers, M., K. Natividad, S. Morse, et al (2016). Full scale tests of heat strengthened glass with ceramic frit. Glass Structures and Engineering. Available at: https://doi.org/10.1007/s40940-016-0032-3.
Kotz, F., K. Arnold, W. Bauer, et al (2017). Three-dimensional printing of transparent fused silica glass. Nature. https://doi.org/10.1038/nature22061.
Disclaimer: The views expressed here are those of the author expressed in their private capacity and do not necessarily represent the views of AZoM.com Limited T/A AZoNetwork the owner and operator of this website. This disclaimer forms part of the Terms and conditions of use of this website.