In this interview, Murielle Goubard, the Global Sector Manager for Building Materials at Malvern Panalytical, talks to AzoBuild about sustainable challenges in the cement industry.
How does your work relate to cement development and production?
My primary responsibility is assisting our customers in resolving their concerns and addressing new and upcoming challenges within their industry. Cement is significant among construction materials as a standalone and fundamental concrete component.
My role entails identifying effective analytical solutions for crucial issues such as cement production decarbonization, raw material recycling, energy consumption management, and the digitalization of processes.
This last aspect is a vital determinant of success across all these areas. We aim to achieve these objectives while preserving or enhancing cement and concrete's final properties.
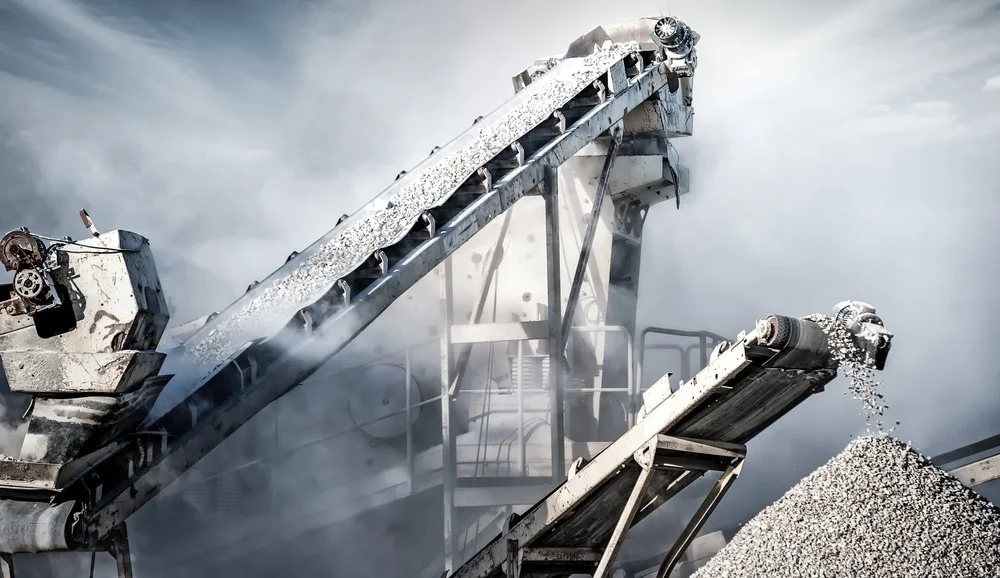
Image Credit: Shutterstock/Banana Republic images
This task involves the opportunity to exchange ideas with industry specialists and to incorporate local specificities, including regulatory requirements and the availability of materials at plant locations.
A particularly exciting aspect of my role is combining my analytical expertise with cement manufacturing knowledge to conceive and develop increasingly optimal solutions. These solutions enhance efficiency, resilience, predictive capabilities, and cost control.
What changes has the cement industry undergone these last years?
For more than 40 years, cement manufacturers have tried to reduce their environmental impact, specifically concerning their CO2 emissions.
To achieve this, they have undertaken several actions:
- Enhancing the energy efficiency of kilns and processes
- Utilizing alternative fuels (like industrial residues and biomass) to partially replace the fossil fuels that power cement kilns
- Employing alternative raw materials
- Producing new multi-constituent cement (such as clinker + slag/fly ash, calcined clay/limestone, etc.) while reducing the clinker content to mitigate the environmental footprint of concrete. The most commonly used cement, Portland and Portland-composite cement contain over 95% and 65% clinker content, respectively. Supplementary cementitious materials, such as fly ash from coal power plants and blast furnace slag from steelmaking, can partially substitute clinker. Reducing the clinker ratio requires less energy for clinker burning, and some of the process emissions inherent to clinker-making are avoided. Depending on the decarbonization paths pursued by the power and steel sectors, these alternative feedstocks may become less accessible. This is why we now observe the emergence of new cement types like LC3 (limestone calcined clay cement), comprising 50% clinker, 30% calcined clay, 15% limestone, and 5% gypsum (traditional Ordinary Portland cement consists of 95% clinker + 5% gypsum).
Circularity has also been a focal point, leading, for example, to recycling concrete fines for cement production.
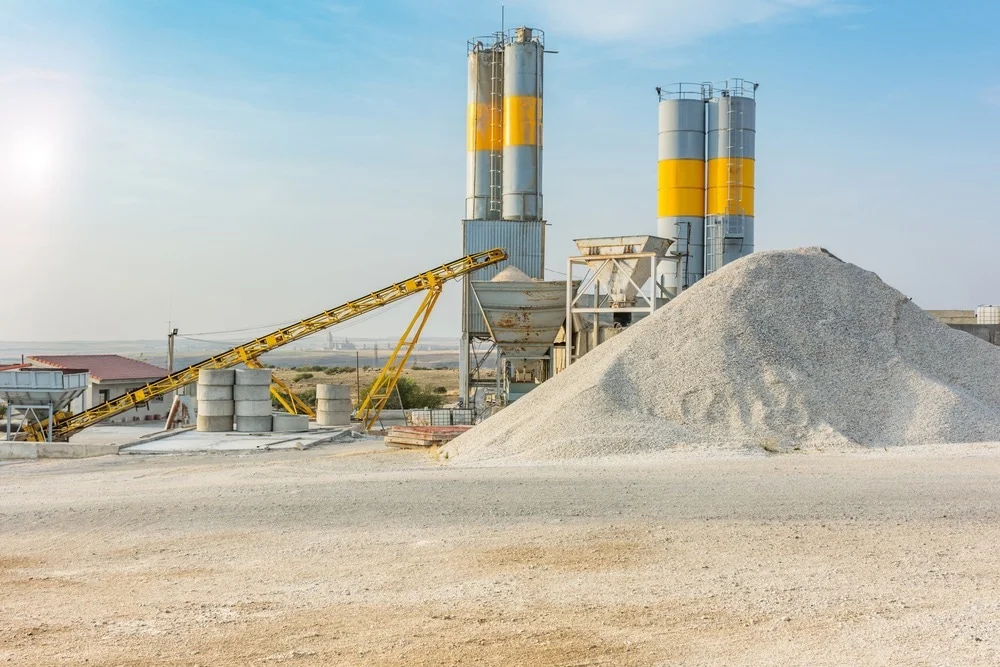
Image Credit: ShutterStock/Juan Enrique del Barrio
Large plants with multiple production lines have been developed, featuring highly automated processes and digital-driven monitoring.
Part of the solution for aiding this transition involves capturing CO2 emissions using Carbon Capture and Utilization and Storage (CCUS) technologies, applied to both combustion and process emissions or combining a zero-CO2 heat source with the capture of concentrated process emissions.
Several different breakthrough technologies are currently being investigated:
- Post-combustion technologies that separate CO2 from flue gas
- Oxyfuel combustion, where fuel is burned in oxygen rather than air, results in a much higher concentration of CO2 in the flue gas.
- Integration of calcium-looping into the cement plant or its use as a tail-end technology
- Direct separation technology, applied in conjunction with a zero-CO2 heat process. The selection of technologies depends on their techno-economic competitiveness and varies based on the availability of renewable electricity and waste heat recovery and integration.
Other innovative solutions are being researched and developed, such as optimizing structural design and concrete specifications, designing infrastructure for disassembly and reuse/recycling of concrete, substituting concrete with zero-CO2 materials like wood, employing graphene fibers instead of steel for reinforced concrete, and exploring 3D printing.
How have environmental concerns driven these changes in recent years?
Environmental concerns are the primary reasons for this disruptive transition. Cement is the binding agent for concrete, the world's most widely used construction material. The cement sector is a significant emitter of greenhouse gases, contributing to approximately 7% of global CO2 emissions.
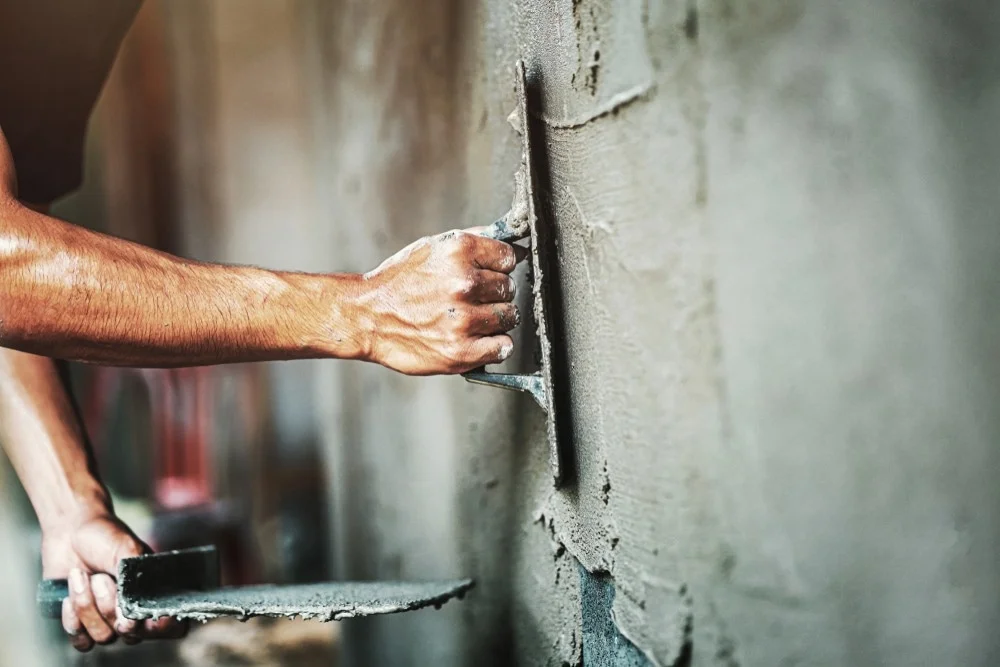
Image Credit: ShutterStock/lovelyday12
In the more advanced dry process of cement production, raw ingredients undergo calcination at temperatures ranging from 900 to 1250 °C in a pre-calciner, converting limestone into lime while releasing CO2 as a byproduct.
These materials are introduced into a rotary kiln, where they amalgamate to form clinker at 1450 °C (with flame temperatures reaching 2000 °C). The clinker is cooled, ground, and blended with other materials to produce cement.
The combustion of fuels for heating cement kilns accounts for 35% of the carbon footprint associated with clinker production, while the remaining 65% results from process emissions released during the calcination reaction involved in clinker production.
What regulations exist for cement production?
Regulations vary depending on the country or territory. Current norms are established based on the composition of cement and concrete. For instance, EN-197-1 governs blended Portland cement in Europe and has been recently updated with EN-197-5 to encompass new multi-component cement like LC3 (CEM II/C-M and CEM VI).
There is an ongoing project to develop a complementary new norm, EN-197-VI. These regulations can sometimes restrict the progress and adoption of innovative, low-CO2 cement. A study is underway to assess the advantages of transitioning from standards founded on chemical composition to standards rooted in cement performance.
When did Malvern Panalytical become involved in cement development?
Malvern Panalytical has always been deeply involved in cement development. Initially, the company contributed significantly to quality control by employing its renowned X-Ray fluorescence spectrometers for assessing the chemical composition of cement. These spectrometers were the first widely adopted analytical technique in cement plants.
Its laser diffraction analyzers have been pivotal in monitoring particle size distribution. More recently, X-Ray diffractometers have emerged as critical tools for optimizing clinker production in kilns. Over the past five years, this technique has gained widespread adoption.
With the advent of Plant 4.0, we observe a growing utilization of our real-time analyzers. These analyzers are employed for chemical analyses, such as Cross-belt PFTNA, which assesses the composition of kiln feed, and for particle size distribution, through online/at-line laser diffraction, which monitors cement particle size distribution.
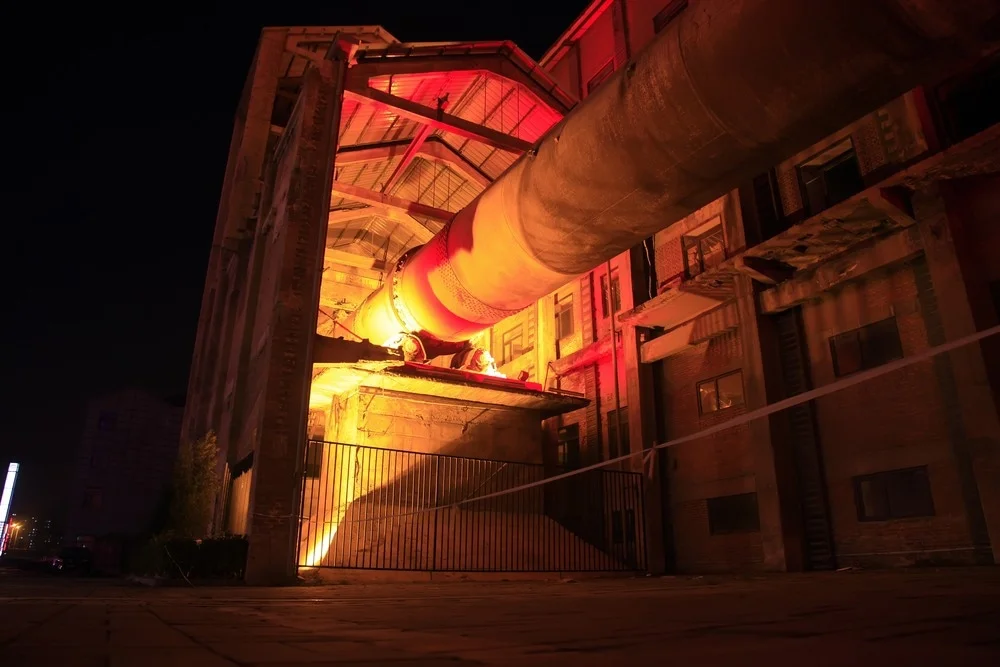
Image Credit: ShutterStock/junrong
What are some of the challenges associated with producing low-CO2 cement?
In addition to the traditional challenges of maintaining round-the-clock production, ensuring the suitability of cement properties, and preventing customer complaints, new challenges have emerged with the introduction of "green cement":
New challenges are linked to the new “green cement”:
- Utilizing alternative fuels introduces a high level of heterogeneity, necessitating the adjustment of kiln flame profiles to produce clinker. This entails managing many variations and maintaining strict control over composition to avoid harmful elements, such as Hg, Cd, and Tl (with a maximum concentration of < 0.5 ppm), or other elements like As, Cr, Sn, Sb, Pb, Zn, and Ni (with a maximum concentration of < 10s –100s ppm), which are poisons for the cement-making process.
- Reducing the clinker ratio necessitates precise control over kiln feed, including chemical composition and particle sizes, to maximize its reactivity.
- The control of various aspects of the production process, such as temperature and atmosphere, is crucial to achieving the desired product characteristics, including oxidation and color.
- For LC3, the use of suitable calcined clay presents a specific challenge. Producing high-quality calcined clay locally requires a dedicated calciner and precise operational parameters.
How can cement be analyzed? What products does Malvern Panalytical offer to help perform cement analysis?
The cement industry continually needs to reduce laboratory analysis costs while optimizing the quality and reliability of the analytical process. Additionally, every phase of the construction process is now being evaluated regarding sustainability.
Cement represents one component of the total Life Cycle Assessment (LCA) of construction. Consequently, its production must prioritize environmental friendliness. This objective can be achieved through advanced laboratory automation and the digitalization of operating and process control.
The complete sample preparation, analysis processes, and sample transportation to and within the laboratory can be mechanized and computerized within an automated laboratory.
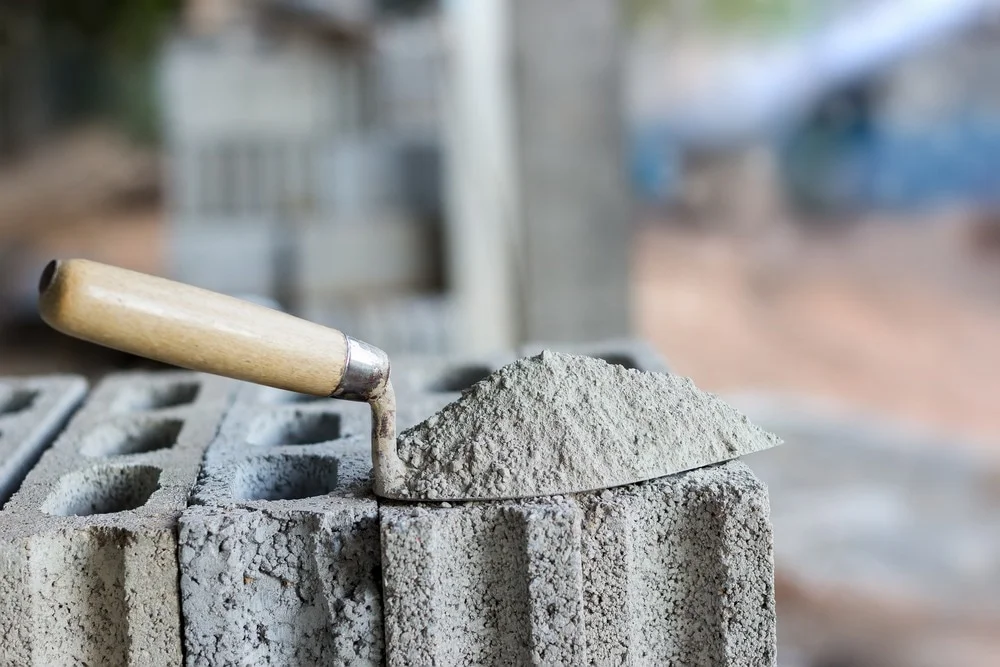
Image Credit: ShutterStock/Okaycm'Stocker
Results can be merged, validated, and distributed without human intervention. This leads to higher repeatability, smaller tolerances, and reduced costs for the required analyses.
It also enables the achievement of more ambitious Key Performance Indicators (KPIs), such as those related to a lower CO2 footprint based on low clinker cement or the use of alternative fuels for kiln heating.
KPIs related to electricity savings during cement grinding based on Particle Size Distribution or resource preservation through recycling materials based on chemical composition analyses can be targeted.
All these automated analyses help reduce the relative uncertainty of the results, allowing for the definition of narrower acceptance limits around the fundamental target values.
The next section delves into the leading automated solutions that can be used as sensors for KPIs to enhance the operational efficiency of a cement plant:
X-Ray Fluorescence (XRF) systems
Cement quality control laboratories employ X-Ray fluorescence (XRF) systems like the Malvern Panalytical Zetium to determine major and minor oxides in clinker, cement, and raw materials, such as limestone, sand, and bauxite.
For fast and accurate results across a wide range of products with varying chemical compositions, samples can be prepared as fused beads using the Automated Claisse Eagon2 and the synthetic Certified Reference Materials (CRMs) of the WROXI base and cement extension.
Combination of X-Ray fluorescence (XRF) and X-Ray diffraction (XRD) systems
Combining X-Ray fluorescence (XRF) and X-Ray diffraction (XRD) systems like the Malvern Panalytical Zetium and the Aeris-Cement enables chemical and mineralogical phase analyses for more comprehensive sample characterization.
In addition to oxide chemical compositions determined by XRF, cement quality is monitored based on classical quantifications, including quartz in raw meal, free lime (CaO), clinker phases, and calcite (CaCO3) in cement.
This combination helps manage alternative fuels (AF) or alternative raw materials (ARM) through the complete analysis of clinker to prevent adverse effects on reactivity. It also facilitates fuel consumption reduction through automated monitoring of clinker constituents.
It enables rigorous monitoring of cement quality control with representative, accurate, reliable, and rapid automated analyses of sulfates (dehydration during grinding significantly impacts cement properties) and the composition of blended cement, including quantification of 'low CO2' additives like slag, fly ash, or calcined clays.
Zetium and Aeris-Cement can be integrated into extensive automation or considered a single unit when installed as a Twin. In the latter case, dedicated software monitors both instruments, combining results from both techniques for better analysis.
Cross Belt Analyzer CNA Pentos and On-Line Particle Size Distribution Analyzer Insitec
On top of these automated solutions, two real-time instruments are used, including:
- The Cross Belt Analyzer, CNA Pentos, which employs pulsed fast and thermal neutron activation (PFTNA) technology for continuous analysis of raw materials
- The On-line Particle Size Distribution Analyzer Insitec
Both provide a lot of data for:
- Direct process optimization (for instance, achieving energy savings and precise monitoring to produce eco-friendly cement using new Supplementary Cementitious Materials such as calcined clays)
- Enhanced cement performance through digitalization (utilizing machine learning for predictive strength at 28 days, for example)
- Improved uptime through a cloud solution, Smart Manager
The Malvern Panalytical Cross Belt Analyzer, CNA Pentos, utilizes pulsed fast and thermal neutron activation (PFTNA) technology. It is installed directly on the conveyor belt to analyze the entire material stream continuously and in real-time.
This aids in troubleshooting issues related to pre-blending stockpile control, quarry management, raw mix proportioning control, and material sorting.
As the Zetium (XRF) and the Aeris Cement (XRD) together provide more comprehensive and precise information on the analyzed material, the Zetium (XRF) can be integrated into an interactive loop with the CNA Pentos (PFTNA). This offers access to fast and extensive real-time data with enhanced accuracy, employing software like O’Blend.
Incorporating a CNA and suitable mix control software can substantially reduce the standard deviation of the Lime Saturation Factor (LSF) in the kiln feed, often achieving a standard deviation approaching 1%.
This typically results in savings in three key areas:
- Kiln heat consumption
- Grinding energy
- Additional production
To illustrate, consider the impact of the CNA on LSF. The standard deviation (STDEV) at a well-designed, well-operating plant should approach 1%. A modest improvement in the kiln feed stability (reducing STDEV LSF from 5% to 2%) would yield the benefits described below. The less stable the initial kiln feed, the more pronounced the benefits.
Source: Malvern Panalytical
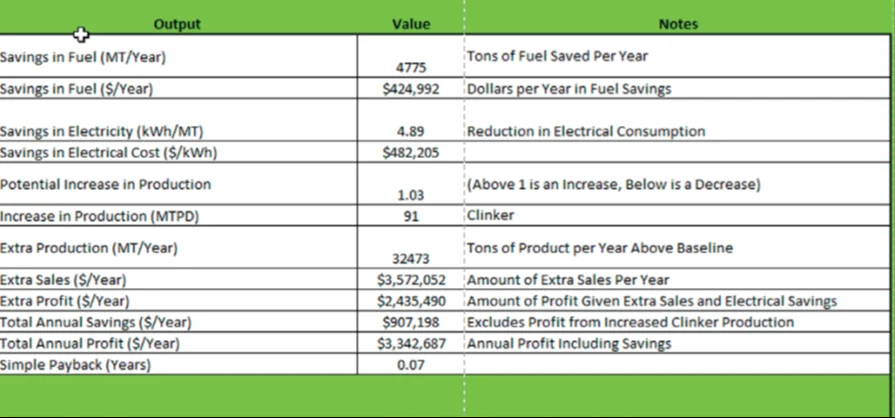
Other key parameters to manufacture performant cement
In addition to chemical and mineralogical compositions, other key parameters for manufacturing high-performance cement are particle size (fineness) and particle size distribution (PSD), which now replaces the Blaine approach.
These parameters directly impact physical and mechanical properties, such as setting time (the rate of hydration), rheology, and final strength development. Each fraction of the particle size distribution plays a vital role in determining cement performance. This is why it is so important to monitor the PSD with real-time analysis:
- Particles that are too fine (less than 2 microns in diameter) cause the cement to cure exothermically, leading to rapid setting and cracking
- Large particles (greater than 32 microns) may not fully hydrate during regular use, reducing the strength of the end product
- Typically, optimal strength is achieved when 50-70% of the cement falls within the 2 to 32-micron range, depending on the intended grade of the final product.
When integrated with an automated lab, the Malvern Panalytical Insitec Cement Labsizer (Laser Diffraction LD) measures large sample volumes and can reliably operate in challenging process environments (dusty, noisy, vibrating, etc.).
Malvern Panalytical's online Insitec (Laser Diffraction) offers real-time measurements to continuously monitor the final grinding steps. Its accurate and extensive data optimizes finish mill performance, increases plant throughput, and enables significant energy savings.
The Malvern Link II software manages automatic closed-loop control to respond in real-time to production fluctuations, optimizing the grinding process and reducing variability.
Based on our extensive experience, we can assert that cement production can increase by approximately 5-8%, and energy consumption can decrease by 4 to 8% when the standard deviation is reduced by 20-40% (resulting in more stable production).
In conclusion, the current sustainability challenges in the cement industry are driving the adoption of smart, "Industry 4.0" based plants. Technologies like the Industrial Internet of Things, artificial intelligence, and cyber-physical systems will seamlessly interact, communicate, and adjust.
Achieving this requires collecting precise data using the right sensors in an automated environment, including chemical compositions (XRF, PFTNA), mineralogy (XRD), and particle size (Laser diffraction), along with appropriate sampling methods (Fusion Machine for XRF).
Malvern Panalytical, with its extensive experience, stands as the sole supplier capable of providing all these automated sensors.
This enables us to leverage the combined results to enhance your process efficiency, ensuring the production of cement that aligns with your customer's requirements, including cement (or concrete) properties and life cycle assessments that meet the latest sustainability targets.
About Murielle Goubard
Murielle Goubard, the Global Sector Manager for Building Materials at Malvern Panalytical, focuses on developing business opportunities for analytical solutions applied to cement, concrete, glass, and asphalt materials.
She earned her Ph.D. in Materials Science from Sorbonne University in Paris, France, and then continued her materials research at Solvay for 15 years.
Murielle Goubard joined Malvern Panalytical 17 years ago, where she deepened her knowledge of building materials while serving as the General Manager of Malvern Panalytical France, collaborating extensively with international cement companies.
About Malvern Panalytical
Malvern Panalytical’s technologies assist scientists and engineers across various industries and organizations in overcoming challenges related to maximizing productivity, improving product quality, and expediting market delivery.
Malvern Panalytical's mission is to develop customer-centric solutions and services that yield tangible economic benefits through the chemical, physical, and structural analysis of materials.
Disclaimer: The views expressed here are those of the interviewee and do not necessarily represent the views of AZoM.com Limited (T/A) AZoNetwork, the owner and operator of this website. This disclaimer forms part of the Terms and Conditions of use of this website.