Chloride ions in maritime conditions enter the concrete protective layer and rust rebars, jeopardizing their structural safety and longevity. A new study in the journal Buildings considers how continuous glass fiber and resin are used to make glass fiber reinforced polymer (GFRP) bars. They are corrosion-resistant, have high tensile strength, and are light in weight.
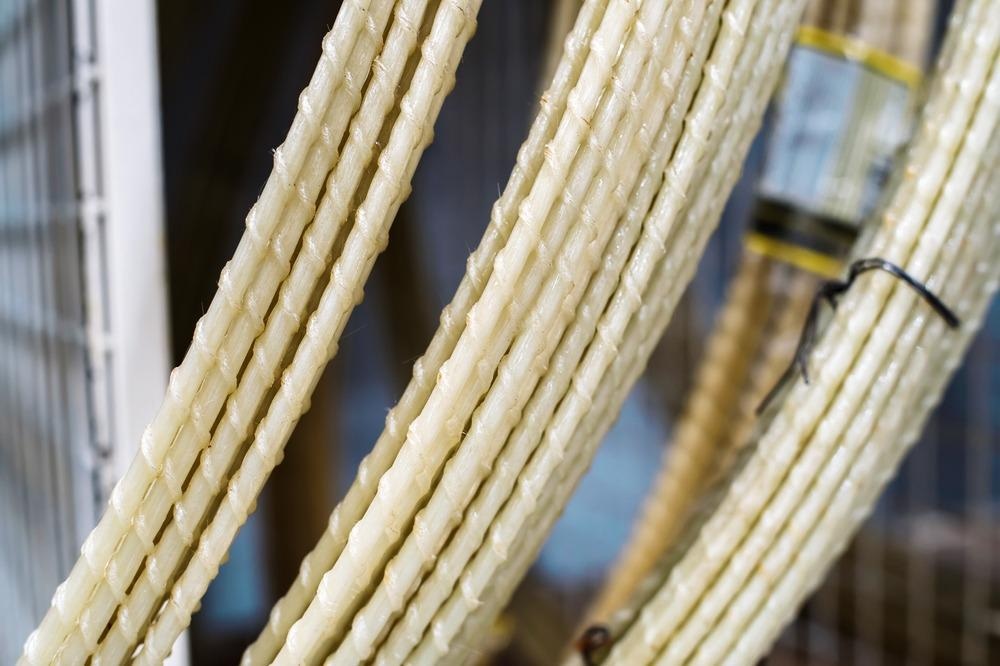
Study: Assessment and Prediction Model of GFRP Bars’ Durability Performance in Seawater Environment. Image Credit: Dmitry Markov152/Shutterstock.com
GFRP induces microstructure damage and a macro-mechanical property decrease when employed in a high alkali concrete solution and marine environment, despite their corrosion resistance. This is due to damage to glass fiber, resin, and their interface phase caused by the service environment. GFRP bars of vinyl-ester, polyester, and epoxy resin in the alkali environment at 60 °C showed signs of deterioration after 5000 hours.
When free OH− and water molecules diffuse in GFRP bars, they produce a chemical reaction with esters groups in the resin matrix, resulting in the degradation of GFRPs.
Researchers have been studying the endurance of GFRP bars in the maritime environment in recent years. They discovered that the resin matrix had a significant influence on the durability of the materials.
Due to the alternating impact of seawater wet-dry environment on offshore engineering, seawater concrete was utilized to wrap GFRPs and accelerated aging at 60 °C, based on an exponential degradation model. The tensile strength of GFRP bars was retained at a rate of 72%.
The goal of this research was to look at the durability of GFRP bars that had been treated in natural seawater, an artificial saline-alkali solution, and concrete. Temperature (25, 40, and 60 °C), as well as age duration (15, 30, 60, 90, and 183 days), were studied.
The study also planned to use interlaminar shear strength (ILSS) to investigate the mechanical property deterioration of GFRP bars under various test settings. Finally, a model was devised for predicting the long-term mechanical characteristics of GFRP bars in a saltwater environment.
Methodology
As illustrated in Figure 1, the samples were put in an incubator for accelerated aging.
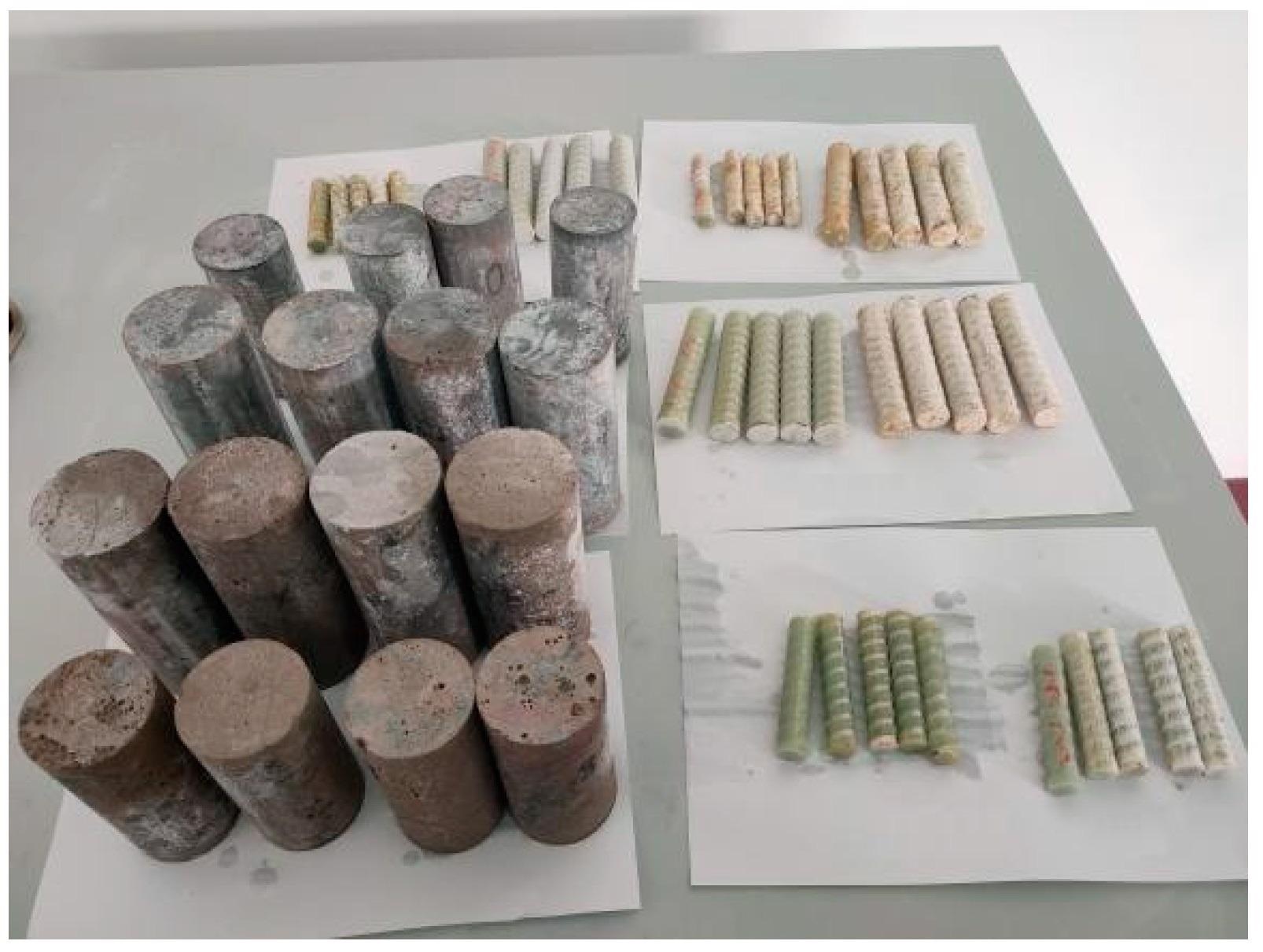
Figure 1. Specimens. Image Credit: Li, et al., 2022
The WAW-1000D electro-hydraulic servo universal testing equipment was used to conduct the short-beam shear test, which followed ASTM D4475. Figure 2 shows the span, which was set at 48 mm.

Figure 2. Short-beam shear test. Image Credit: Li, et al., 2022
Results and Discussion
Figure 3 illustrates the surface morphologies of the specimens after 183 days of aging in three environments at 60° C.
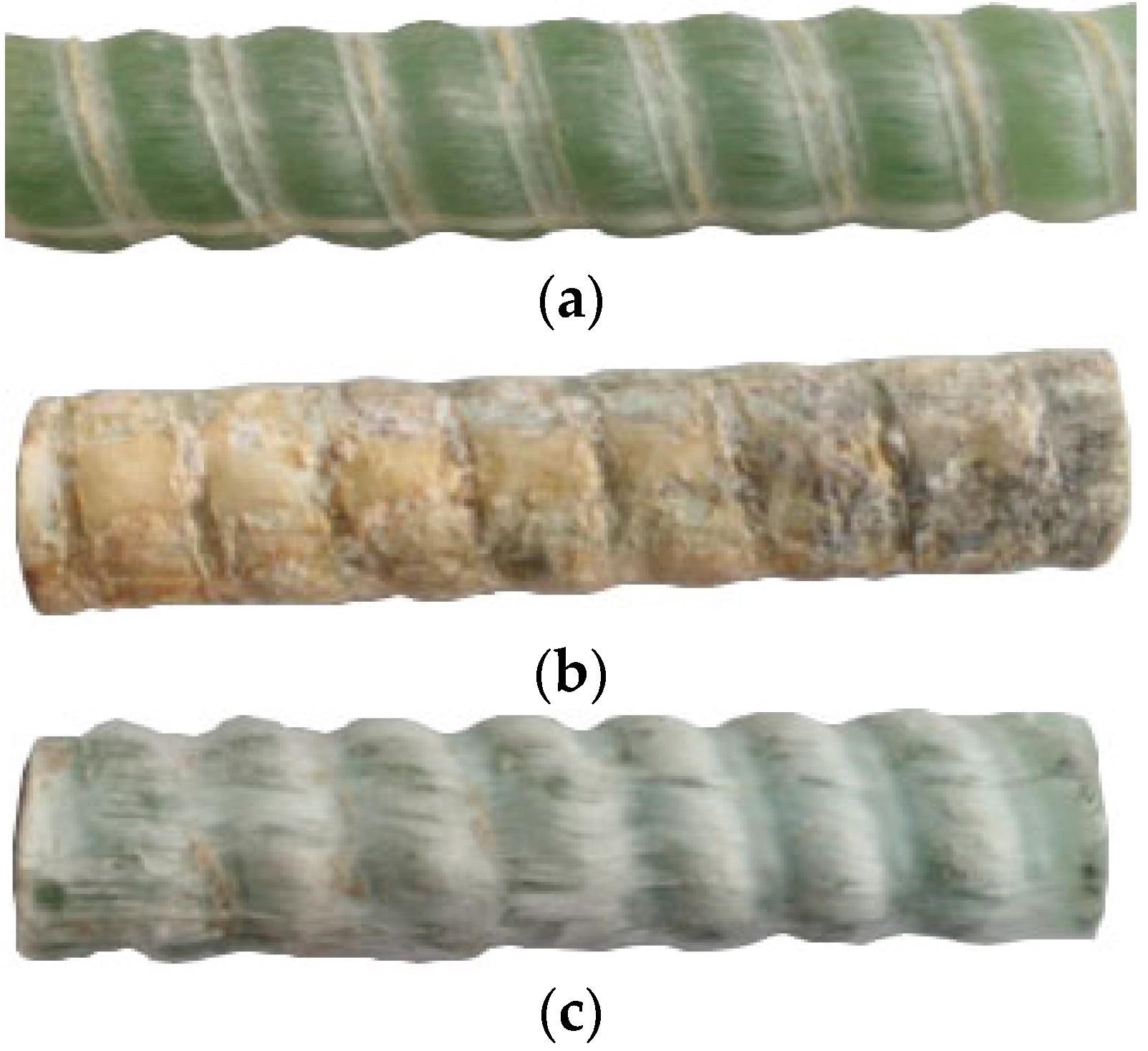
Figure 3. Surface morphology of GFRP bars after aging in different environments at 60 °C for 183 days: (a) SW; (b) SA; and (c) SWC. Image Credit: Li, et al., 2022
Unconditioned bars had an ILSS of 46.93 MPa on average. The ILSS retention rate in Table 1 is the ratio of the aged sample’s ILSS to the unconditioned bars’ ILSS. Table 1 lists the test results.
Table 1. ILSS retention (%). Source: Li, et al., 2022
|
SW |
SWC |
SA |
|
25 °C |
40 °C |
60 °C |
25 °C |
40 °C |
60 °C |
25 °C |
40 °C |
60 °C |
15 d |
98.53 |
97.10 |
94.41 |
97.82 |
96.70 |
92.93 |
95.93 |
95.53 |
90.16 |
30 d |
98.21 |
95.97 |
89.94 |
96.58 |
94.93 |
87.04 |
93.23 |
92.45 |
81.45 |
60 d |
95.93 |
93.93 |
83.25 |
94.37 |
91.23 |
76.58 |
87.22 |
85.45 |
70.80 |
90 d |
94.76 |
92.33 |
75.46 |
92.37 |
88.05 |
68.27 |
81.84 |
77.94 |
61.66 |
183 d |
91.82 |
86.62 |
66.41 |
89.16 |
80.22 |
53.10 |
78.25 |
68.73 |
45.36 |
Figure 4 shows that in the three environments of SW, SWC, and SA, the ILSS retention of GFRP bars reduces.
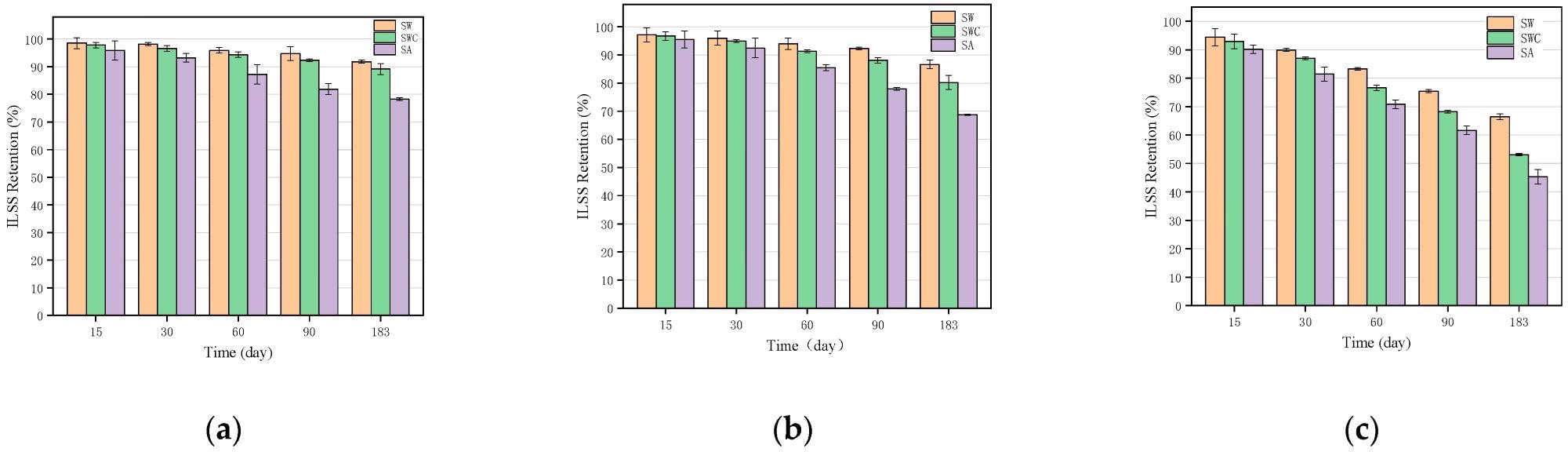
Figure 4. Comparison of ILSS retention of GFRP bars in three environments: (a) 25 °C; (b) 40 °C; (c) 60 °C. Image Credit: Li, et al., 2022
Figure 5 depicts the effect of aging temperature on GFRP bar strength retention.
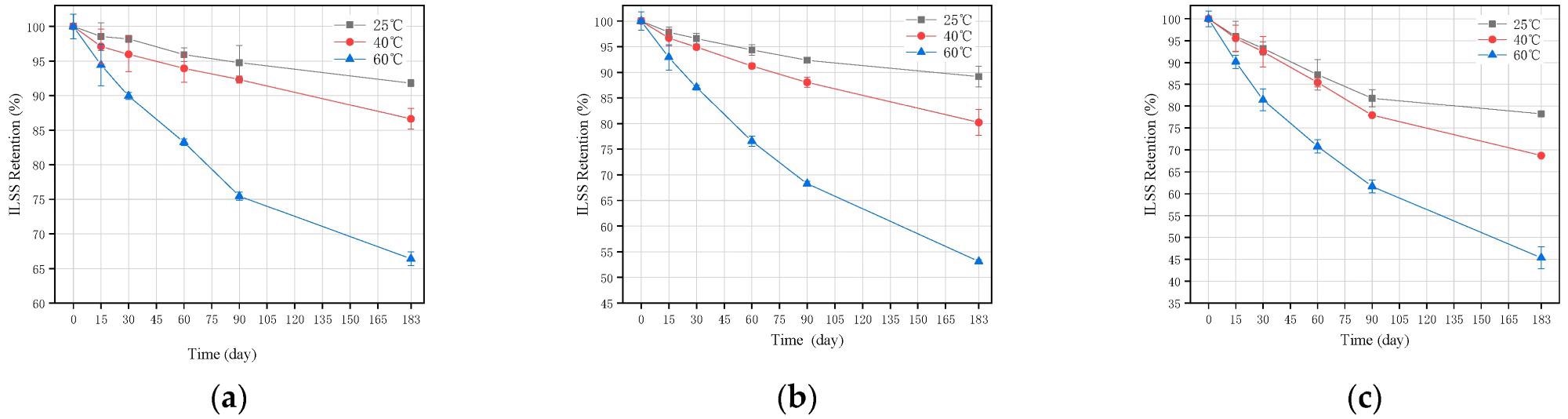
Figure 5. Comparison of ILSS retention of GFRP bars in three temperatures: (a) SW; (b) SWC; and (c) SA. Image Credit: Li, et al., 2022
Figure 6 illustrates the microstructures of the samples after 183 days of accelerated aging at 60 °C in three environments.
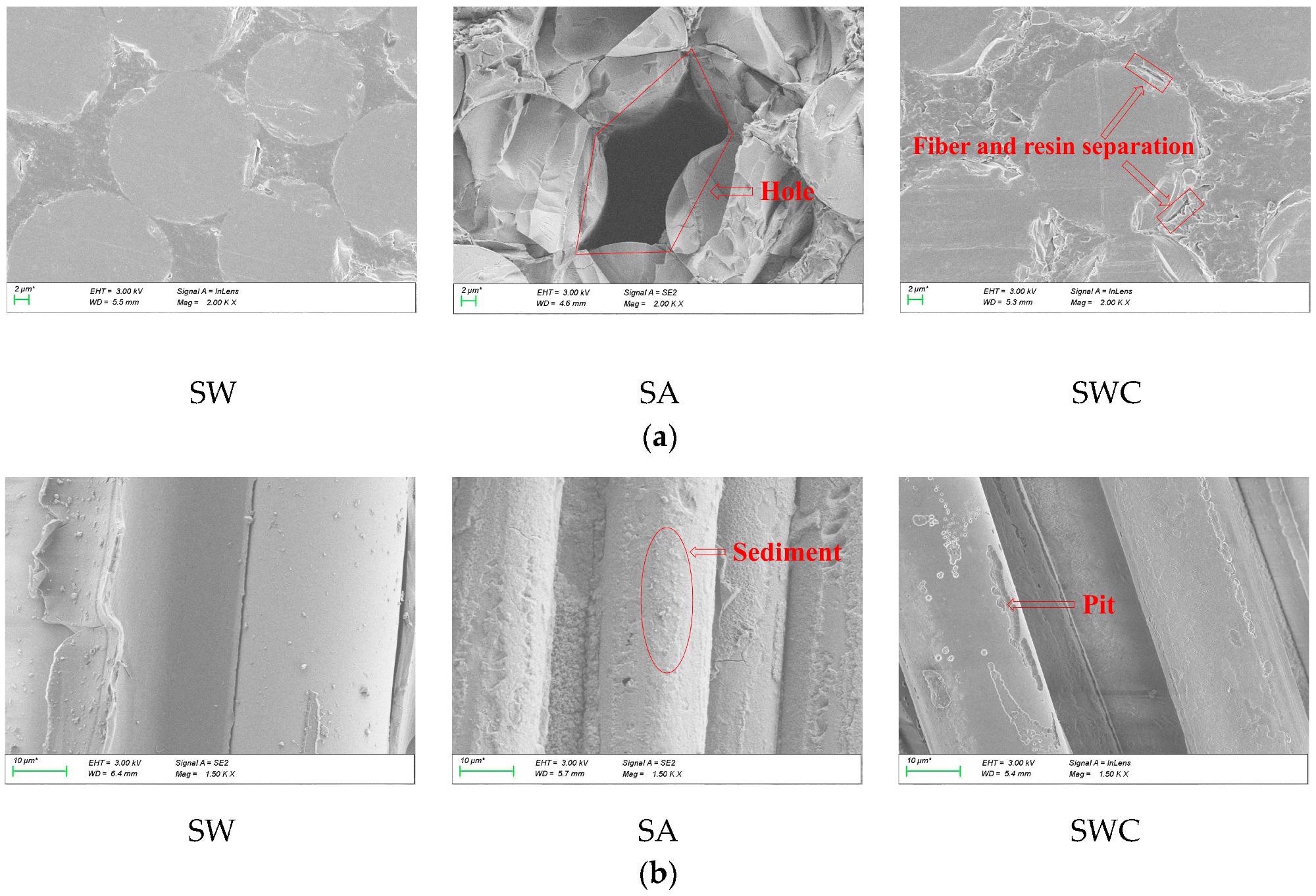
Figure 6. SEM photos of GFRP bars aged at 60 °C for 183 days: (a) Cross section; (b) Longitudinal section. Image Credit: Li, et al., 2022
Tg represents the glass transition temperature. Tg1 and Tg2 were assigned to the two temperature rise mechanisms, as illustrated in Table 2.
Table 2. The Tg of GFRP bars in different environments. Source: Li, et al., 2022
Environment |
Temperature (°C) |
Aging Time (Day) |
Tg (°C) |
Tg1 |
Tg2 |
Unconditioned |
- |
- |
113 |
115 |
SW |
60 |
183 |
105 |
113 |
SA |
60 |
183 |
102 |
106 |
SWC |
60 |
183 |
102 |
107 |
Tg2 of all samples is larger than Tg1, as seen in Figure 7. After aging at 60 °C for 183 days in the three environments, Tg2 of GFRP bars reduced by 1.7%, 7.8%, and 7.0%, respectively, compared to unconditioned samples.
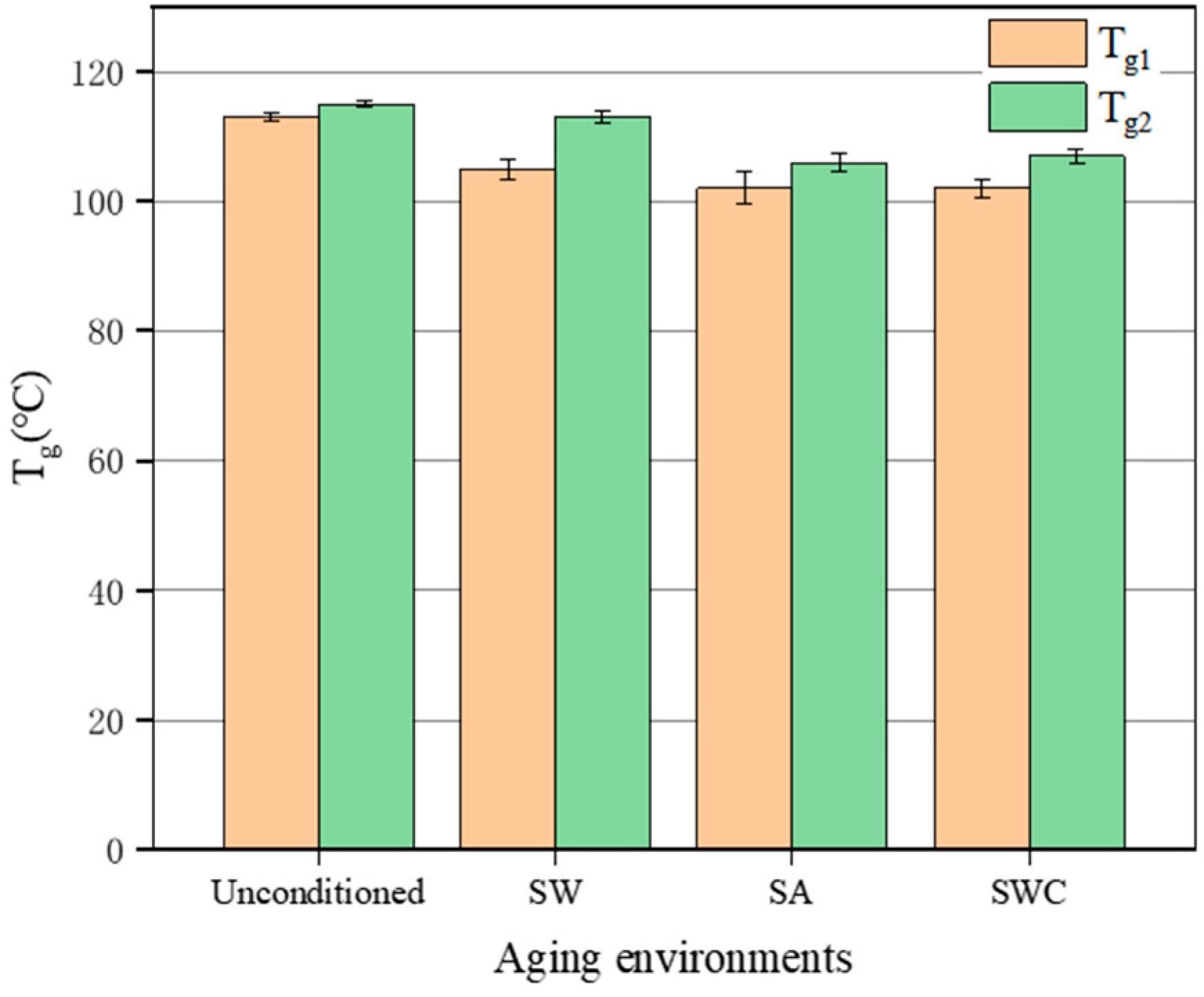
Figure 7. Comparison of Tg of GFRP bars in different aging environments. Image Credit: Li, et al., 2022
The infrared spectra of GFRP bars aged in the environments at 60 °C for 183 days and in a non-aged condition were tested using FTIR, as illustrated in Figure 8.
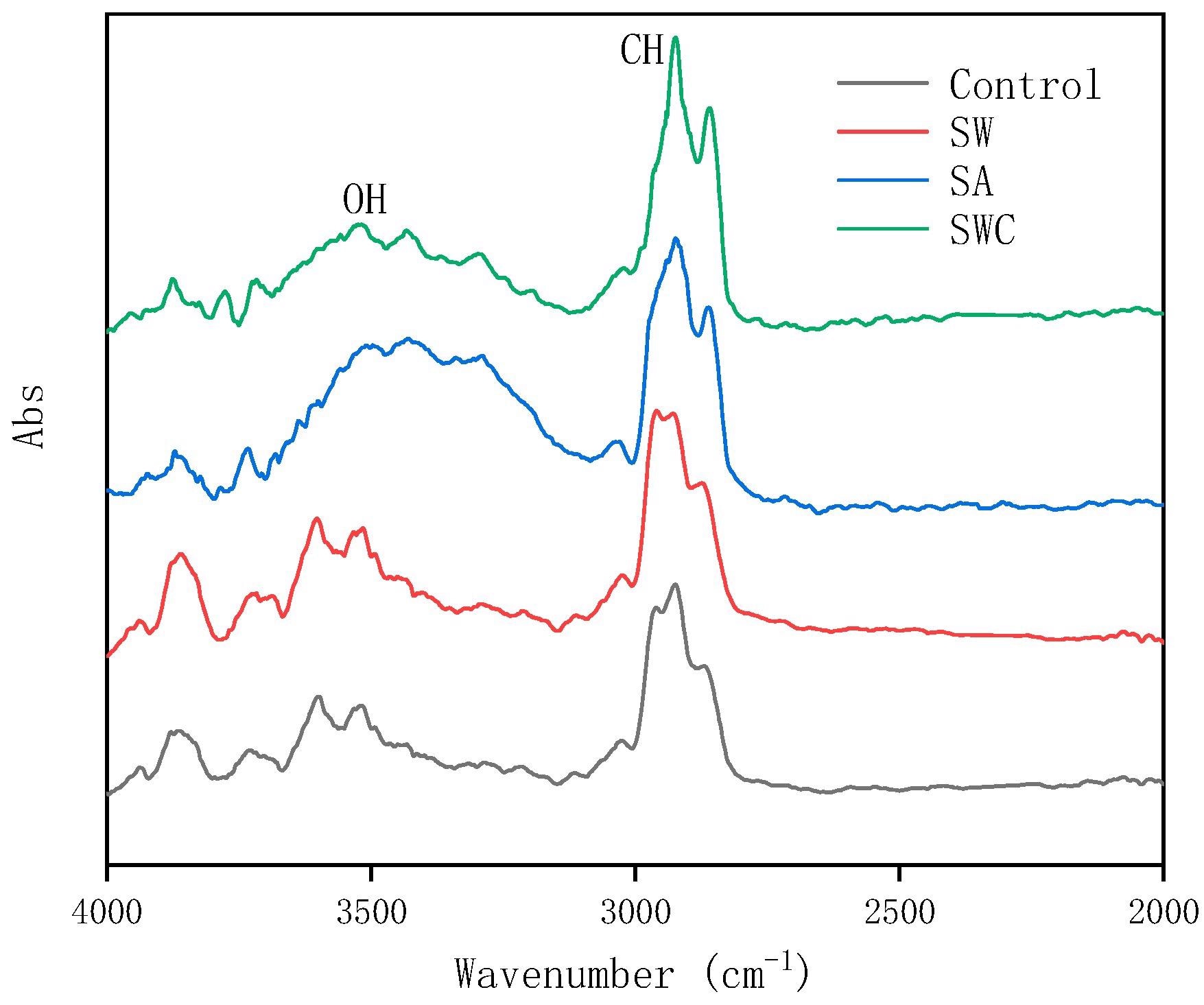
Figure 8. FTIR of GFRP bars. Image Credit: Li, et al., 2022
The test data were fitted to produce the fitting parameter (i.e., τ), and Figure 9 depicts the fitting curve. Table 3 shows the results of theτand correlation coefficients.
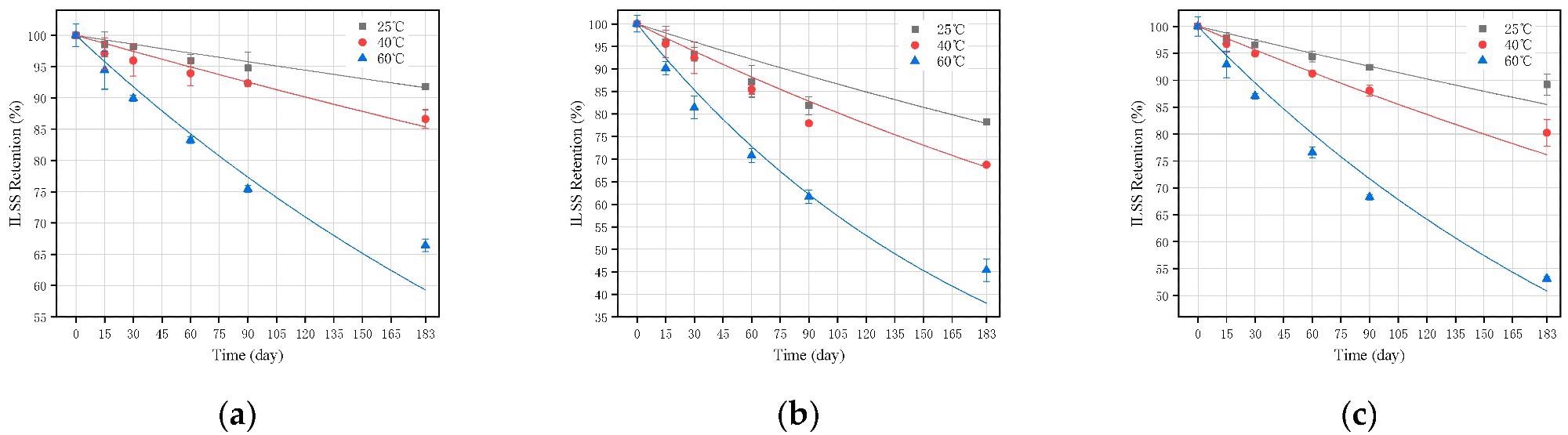
Figure 9. Fitting of long-term mechanical property test data for GFRP bars based on Model 2 in different environments: (a) SW; (b) SA; and (c) SWC. Image Credit: Li, et al., 2022
Table 3. Data fitting of long-term mechanical property test for GFRP bars based on Model 2. Source: Li, et al., 2022
Environment |
Temperature (°C) |
τ |
Fitted Equation |
R2 |
|
25 |
2092 |
Y=100exp(−t/2092) |
0.97 |
SW |
40 |
1157 |
Y=100exp(−t/1157) |
0.95 |
|
60 |
350 |
Y=100exp(−t/350) |
0.89 |
|
25 |
733 |
Y=100exp(−t/733) |
0.93 |
SA |
40 |
478 |
Y=100exp(−t/478) |
0.88 |
|
60 |
189 |
Y=100exp(−t/189) |
0.97 |
|
25 |
1167 |
Y=100exp(−t/1167) |
0.88 |
SWC |
40 |
672 |
Y=100exp(−t/672) |
0.94 |
|
60 |
270 |
Y=100exp(−t/270) |
0.97 |
Figure 10 shows the Arrhenius straight-line fit, and Table 4 lists the straight-line slope and correlation coefficient.
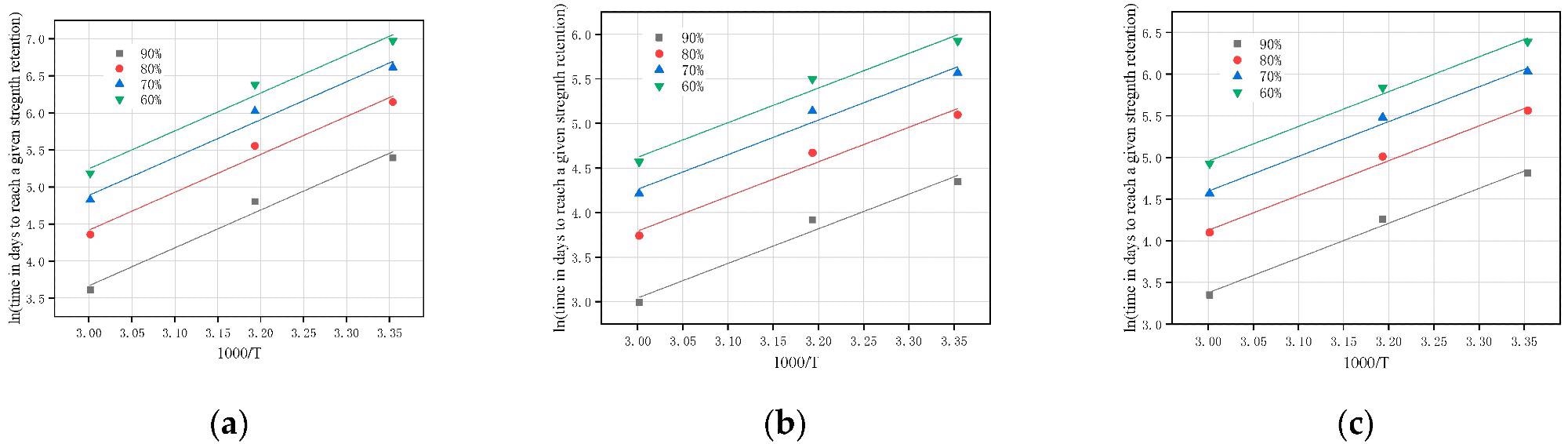
Figure 10. Arrhenius line for durability prediction model of GFRP bars in different environments: (a) SW; (b) SA; and (c) SWC. Image Credit: Li, et al., 2022
Table 4. Fitting of Equation (6) for long-term mechanical property prediction of GFRP bars. Source: Li, et al., 2022
Environment |
Ea/R |
R2 |
SW |
5111 |
0.97 |
SA |
3878 |
0.95 |
SWC |
4173 |
0.98 |
Table 5 shows the TSF for three distinct temperatures and environments.
Table 5. TSF of GFRP bars at different temperatures. Source: Li, et al., 2022
Environment |
12.3 °C |
25 °C |
40 °C |
60 °C |
SW |
1 |
2.144 |
4.873 |
12.983 |
SA |
1 |
1.784 |
3.326 |
6.995 |
SWC |
1 |
1.864 |
3.644 |
8.110 |
The master curve of the mechanical model of GFRP bars in the offshore area of the Yellow Sea of China was developed using the data and test results in Table 5, as shown in Figure 11, and the regression equation parameters are listed in Table 6.
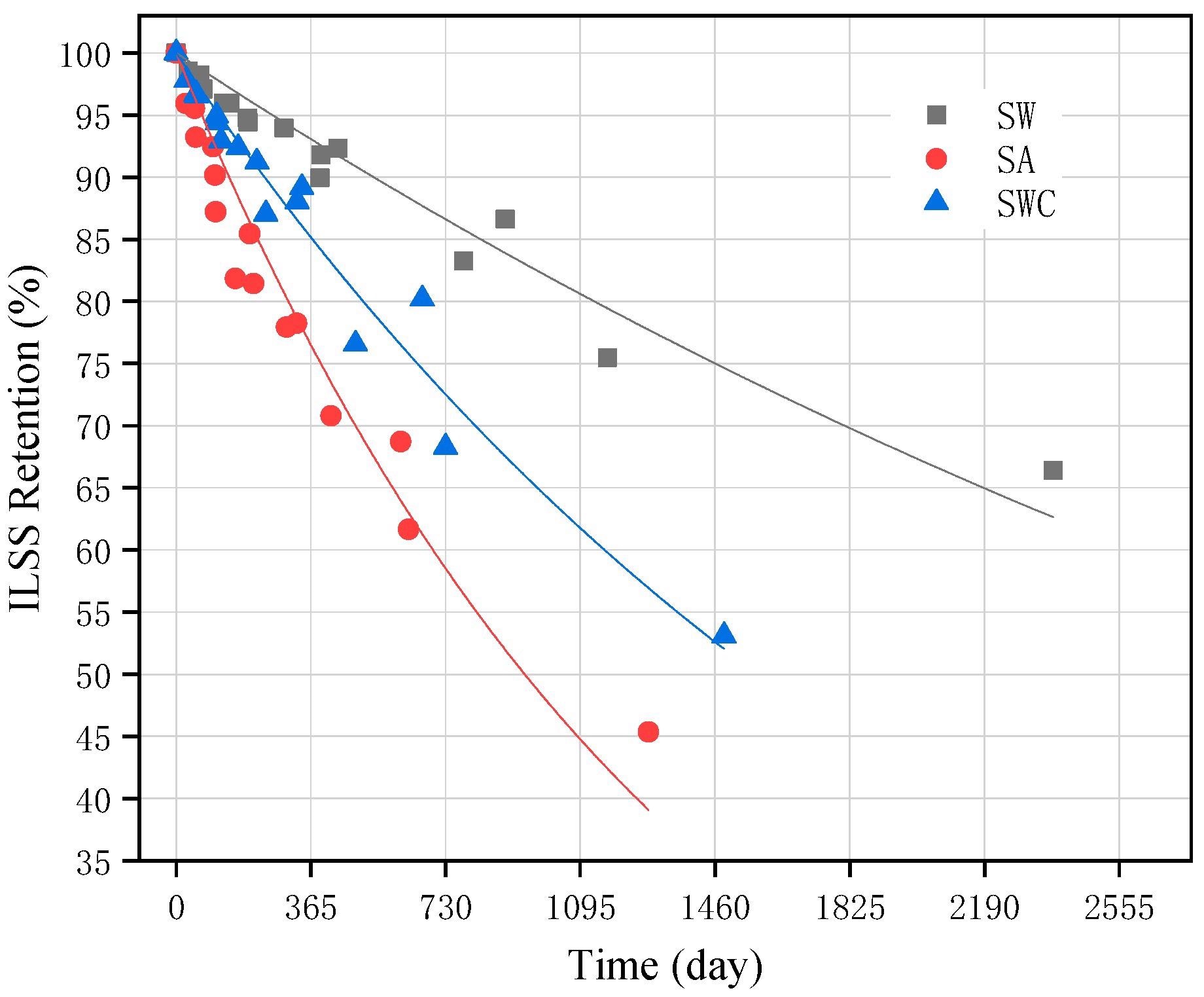
Figure 11. Master curve of long-term mechanical property degradation of GFRP bars in different environments at 12.3 °C. Image Credit: Li, et al., 2022
Table 6. Main curve parameters of regression equation of long-term mechanical model of GFRP bars in the Yellow Sea area of China. Source: Li, et al., 2022
Environment |
τ |
R2 |
SW |
5078 |
0.95 |
SA |
1362 |
0.94 |
SWC |
2272 |
0.96 |
Conclusion
The mechanical deterioration law and mechanism of GFRP bars in different aging environments were investigated in this work.
In the same environment, GFRP bars degraded the fastest in the saline-alkali solution (SA), followed by wrapped with concrete, and then submerged in natural seawater (SWC), and finally natural seawater (SW). The basic reason is that the OH- radical degrades the glass fiber when it combines with SiO2. In the SWC environment, the concrete had a protective effect, resulting in reduced damage.
The rate of ILSS deterioration increases as the temperature rises in all three conditions. Water molecules immediately diffused to the GFRP bars during the early stages of aging, decreasing the resin and fiber’s interfacial bonding capacity. The rate of strength deterioration in the early stages was quicker than in the latter stages.
The microstructures of the samples were examined following accelerated aging in three conditions for 183 days. After aging in SA and SWC conditions, the sample fiber and resin were separated to varying degrees. Different degrees of resin matrix expansion after water absorption generated this phenomenon, and seepage pressure will damage the interface phase as well.
The fiber surface of samples in the SA and SWC environments was extensively affected after aging, while samples in the SW environment had very little aging damage.
Tg of GFRP bars aged in the three environments at 60° C for 183 days. In three environments, the hydrolysis degree of GFRP bars dropped by 1.7%, 7.8%, and 7.0%, respectively, when compared to Tg of conventional samples. In the Yellow Sea area of China, a master curve of a long-term mechanical model of GFRP bars was constructed, which can forecast the strength retention of GFRP bars serving in three environments.
Journal Reference
Li, W., Wen, F., Zhou, M., Liu, F., Jiao, Y., Wu, Q., Liu, H. (2022) Assessment and Prediction Model of GFRP Bars’ Durability Performance in Seawater Environment. Buildings, 12(2), p. 127. Available Online: https://www.mdpi.com/2075-5309/12/2/127/htm
References and Further Reading
- Jiang, L., et al. (2012) Influence of chloride salt type on threshold level of reinforcement corrosion in simulated concrete pore solutions. Construction and Building Materials, 30, pp. 516–521. doi.org/10.1016/j.conbuildmat.2011.12.044.
- Soriano, C & Alfantazi, A (2016) Corrosion behavior of galvanized steel due to typical soil organics. Construction and Building Materials, 102, pp. 904–912. doi.org/10.1016/j.conbuildmat.2015.11.009.
- ACI (American Concrete Institute) (2015) Guide for the Design and Construction of Structural Concrete Reinforced with Fiber-Reinforced Polymer (FRP) Bars; ACI Committee 440, Report 440.1R-15; American Concrete Institute: Farmington Hills, MI, USA.
- Arczewska, P., et al. (2021) Degradation of glass fiber reinforced polymer (GFRP) bars in concrete environment. Construction and Building Materials, 293, p. 123451. doi.org/10.1016/j.conbuildmat.2021.123451.
- Duo, Y., et al. (2012) Environmental impact on the durability of FRP reinforcing bars. Journal of Building Engineering, 43, p. 102909. doi.org/10.1016/j.jobe.2021.102909.
- Al-Salloum, Y. A., et al. (2013) Effect of harsh environmental conditions on the tensile properties of GFRP bars. Composites Part B: Engineering, 45, pp. 835–844. doi.org/10.1016/j.compositesb.2012.05.004.
- El-Hassan, H., et al. (2018) Durability of glass fiber-reinforced polymer bars conditioned in moist seawater-contaminated concrete under sustained load. Construction and Building Materials, 175, pp. 1–13. doi.org/10.1016/j.conbuildmat.2018.04.107.
- Manalo, A., et al. (2020) Comparative durability of GFRP composite reinforcing bars in concrete and in simulated concrete environments. Cement and Concrete Composites, 109, p. 103564. doi.org/10.1016/j.cemconcomp.2020.103564.
- Benmokrane, B., et al. (2017) Laboratory Assessment and Durability Performance of Vinyl-ester, Polyester, And Epoxy Glass-FRP Bars for Concrete Structures. Composites, 114, pp. 163–174. doi.org/10.1016/j.compositesb.2017.02.002.
- Chen, Y., et al. (2007) Accelerated aging tests for evaluations of durability performance of FRP reinforcing bars for concrete structures. Composite Structures, 78, pp. 101–111. doi.org/10.1016/j.compstruct.2005.08.015.
- Koller, R., et al. (2007) Fiber-reinforced bars under freeze-thaw cycles and different loading rates. Journal of Composite Materials, 41, pp. 5–25. doi.org/10.1177%2F0021998306063154.
- Robert, M & Benmokrane, B (2013) Combined effects of saline solution and moist concrete on long-term durability of GFRP reinforcing bars. Construction and Building Materials, 38, pp. 274–284. doi.org/10.1016/j.conbuildmat.2012.08.021.
- Morales, C. N., et al. (2021) Durability of GFRP reinforcing bars in seawater concrete. Construction and Building Materials, 270, p. 121492. doi.org/10.1016/j.conbuildmat.2020.121492.
- Khatibmasjedi, M., et al. (2020) Durability of commercially available GFRP reinforcement in seawater-mixed concrete under accelerated aging conditions. Journal of Composites for Construction, 24, p. 04020026.
- Fergani, H., et al. (2018) Durability and degradation mechanisms of GFRP reinforcement subjected to severe environments and sustained stress. Construction and Building Materials, 170, pp. 637–648. doi.org/10.1016/j.conbuildmat.2018.03.092.
- Montaigu, M., et al. (2013) Laboratory characterization and evaluation of durability performance of new polyester and vinylester E-glass GFRP dowels for jointed concrete pavement. Journal of Composites for Construction, 17, pp. 176–187.
- Bank, L. C., et al. (2003) A model specification for composites for civil engineering structures. Construction and Building Materials, 17, pp. 405–437. doi.org/10.1016/S0950-0618(03)00041-2.
- Wu, G., et al. (2015) Prediction of long-term performance and durability of BFRP bars under the combined effect of sustained load and corrosive solutions. Journal of Composites for Construction, 19, p. 04014058.
- Robert, M., et al. (2009) Durability of GFRP reinforcing bars embedded in moist concrete. Journal of Composites for Construction, 13, pp. 66–73.
- Lu, C., et al. (2020) Comparative Investigation on Tensile Performance of FRP Bars after Exposure to Water, Seawater, and Alkaline Solutions. Journal of Materials in Civil Engineering, 32, p. 04020170.
- Wang, Z., et al. (2017) Durability study on interlaminar shear behaviour of basalt-, glass- and carbon-fibre reinforced polymer (B/G/CFRP) bars in seawater sea sand concrete environment. Construction and Building Materials, 156, pp. 985–1004. doi.org/10.1016/j.conbuildmat.2017.09.045
- Canadian Standards Association (CSA).(2019) Specification for Fibre-Reinforced Polymers (CAN/CSA S807-19); CSA: Rexdale, ON, Canada.
- ASTM Standard ASTM D4475-02 Standard Test Method for Apparent Horizontal Shear Strength of Pultruded Reinforced Plastic Rods by the Short-Beam Method (ASTM D4475-02 (2016)), ASTM International: West Conshohocken, PA, USA, 2016; p. 19103.
- Chen, Y (2007) Accelerated Ageing Tests and Long-Term Prediction Models for Durability of FRP Bars in Concrete. Ph.D. Dissertation, West Virginia University, Morgantown, WV, USA.
- ASTM Standard ASTM D3418-08 Standard Test Method for Transition Temperatures and Enthalpies of Fusion and Crystallization of Polymers by Differential Scanning Calorimetry, ASTM: West Conshohocken, PA, USA.
- Nelson, W (1990) Accelerated Testing—Sustained Models, Test Plans, and Data Analyses; Wiley: New York, NY, USA.
- Litherland, K L (1981) The use of accelerated aging procedures to predict the long term strength of GRC composites. Cement and Concrete Research, 11, pp. 455–466. doi.org/10.1016/0008-8846(81)90117-4.
- Gonenc, O (2001) Durability and Service-life Prediction of Concrete Reinforcing Materials. Master’s Thesis, University of Wisconsin-Madison, Madison, WV, USA.
- Kamal, A.S.M & Boulfiza, M (2011) Durability of GFRP rebars in simulated concrete solutions under accelerated aging conditions. Journal of Composites for Construction, 15, pp. 473–481. doi.org/10.1061/(ASCE)CC.1943-5614.0000168.
- Wang, Z., et al. (2017) Long-term durability of basalt- and glass-fibre reinforced polymer (BFRP/GFRP) bars in seawater and sea sand concrete environment. Construction and Building Materials, 139, pp. 467–489. doi.org/10.1016/j.conbuildmat.2017.02.038