Foam concrete is a unique concrete material with numerous applications not only in the construction industry. This article explains what the material is, describes its advantages and applications, and relays the latest advances in foam concrete research.
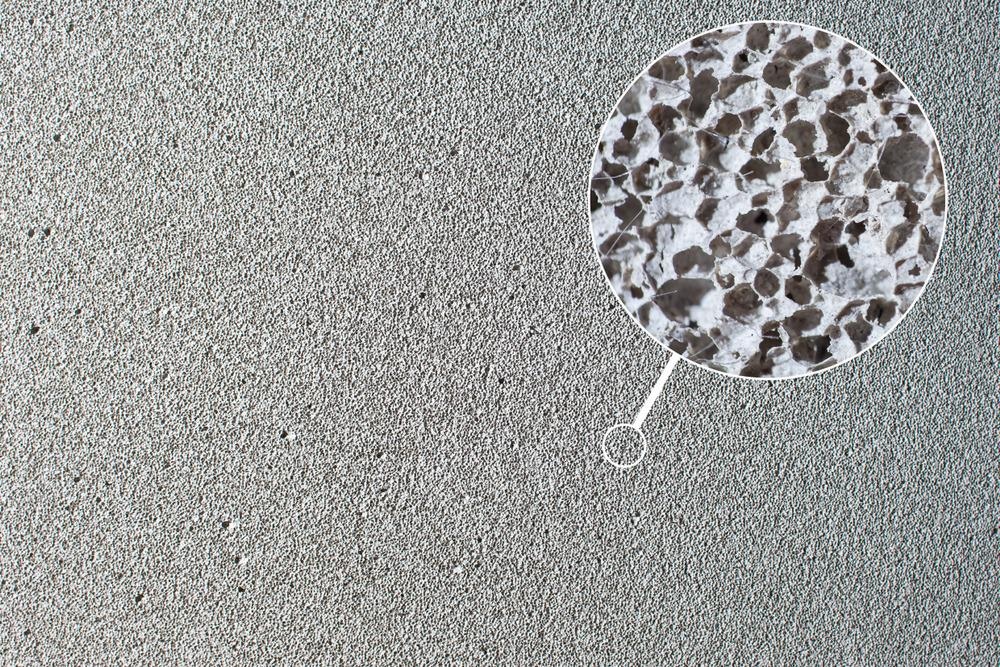
Image Credit: Denys N/Shutterstock.com
Foam concrete is a highly air entrained sand cement that has at least 20% air by volume in the set product. It is made with a cement slurry and can range as high as 85% foam or air content. Most foam concrete applications require at least 50% foam or air by volume.
To foam the concrete, air is entrained mechanically with a pre-formed foam. This is mixed with the cementitious base material in order to create a low-density composite material.
The densities of set foam concrete are also tunable. They range from around 400 kg per m3 to 1,800 kg per m3, and strengths can range from 0.5 N per mm2 to 12 N per mm2.
Foam concrete is also known as foamed concrete, or lightweight cellular concrete (LCC), low-density cellular concrete (LDCC), aerated lightweight concrete, cellular lightweight concrete, and various other industry or brand-specific terms as well as (perhaps more accurately) foamed mortar, foamed grout, and foamed cement.
It is made mostly without coarse aggregate, instead using a liquid concrete slurry. This is why foamed mortar, grout, or cement are perhaps more accurate descriptions of the material. Density is controlled by substituting some or in some cases all of the fine aggregate with foam products.
Fly ash and sand typically make up the fine aggregate material, which is mixed with water and cement. Some manufacturers recommend using only water and cement plus the foaming agent to produce extremely lightweight concrete mixes.
The concrete slurry is combined with an aerated foam product in a concrete mixing plant. To make the foam, manufacturers mix a foaming agent with water and air from a generator. It produces consistent bubbles with high levels of stability in order to resist the chemical and mechanical strains of concrete mixing, pouring, placing, and setting.
Foam concrete can be poured into molds or pumped directly inside structural elements. With the foam, the concrete slurry can flow freely. This is because of the thixotropic behavior of the aerated foam’s bubbles.
The viscous slurry takes up to 24 hours to fully set, but this can be accelerated to as short as two hours with steam curing methods. These techniques raise temperatures up to 70 °C in order to speed up the solidifying process. The temperature required depends on variables like the ambient humidity and external temperature, as well as the specific foam concrete mixture.
Foamed concrete can be removed from its mold once it has fully set, although in some foam concrete manufacturing applications the material is cut into blocks of required sizes using steel wires before it has fully set.
The base mix for foamed concrete products tends to have a much higher cement content than standard concrete mixtures for slabs and structural applications. This has two reasons. First, the amount of air captured in foam bubbles in the concrete decreases the material’s strength exponentially at higher aeration rates. Second, the amount of water in the concrete slurry reduces the strength of the concrete linearly at higher hydration rates.
Typically, foamed concrete mixes have more water included than traditional concrete as well. This is so that it can be easily pumped and thoroughly mixed with foam additives. Water reducing agents and plasticizers used to minimize water content in conventional concrete also typically perform poorly when mixed with foaming agents.
Protein-based dry foams commonly used as foaming agents (or surfactants) for this application can expand by up to 20 times when diluted in water. The surfactant is generally diluted at between 3% and 5% concentration, then it is agitated through a cigar-shaped extruder to produce a stable mixture with foam bubbles.
In the 1990s, synthetic enzyme-based foaming agents have been developed to increase foam stability. The enzyme includes highly active biotechnological proteins that are not based on protein hydrolysis.
These new surfactants, enhanced with specialized foam generation, mixing, and pumping equipment, have led to foam and foam concrete with significantly improved stability. Now, foamed concrete can achieve densities as low as 75 kg per m3, which is just 7.5% that of water.
Foamed concrete has been used extensively in infrastructure projects including highways, commercial construction, disaster relief, school, and residential developments around the world.
It is used primarily for void filling applications and has found use in numerous construction settings. In landscaping, it is used in bridge approaches, embankments, and trench backfill. Infrastructure projects use it for pipeline abandonment, annular fill, and highway sub-base. Buildings use it in precast block form, precast as entire wall elements or panels, cast-in-situ walls, insulation floor and roof screeds, and prefabricated insulation boards.
More from AZoBuild: What is the AFm phase in Portland Cements?
References and Further Reading
Jones, M.R. and L. Zheng (2013). Energy absorption of foamed concrete from low-velocity impacts. Magazine of Concrete Research. Available at: https://www.icevirtuallibrary.com/doi/10.1680/macr.12.00054
ProPump Engineering Ltd. What is Foam Concrete? Foamedconcrete.co.uk. [Online] Available at: https://www.foamedconcrete.co.uk/what-is-foam-concrete/#:~:text=Foam%20concrete%20is%20used%20primarily,loose%20materials%20that%20require%20compaction.
Disclaimer: The views expressed here are those of the author expressed in their private capacity and do not necessarily represent the views of AZoM.com Limited T/A AZoNetwork the owner and operator of this website. This disclaimer forms part of the Terms and conditions of use of this website.