May 15 2007
Background
The purpose of this advisory note is to draw your attention to recent major changes within Australian Galvanizing Standards.
Summary:
- The long standing AS/NZS 1650 “Hot Dipped Galvanized Coatings on Ferrous Articles”, which covered most galvanized products, was deleted in 1999 and replaced by a series of Standards which better distinguish current galvanizing grades and associated steel products such as sheet, wire or light structural or manufactured items.
The difference of these grades is the direct result of the different process and purpose of the galvanizing involved.
After-fabrication galvanizing by the primary process, produces the maximum thickness possible relative to steel thickness, with long term protection its only objective. Its new identity is AS/NZS 4680 and is aligned to the International Standard EN ISO 1461.
- The term “Hot Dip” is no longer sufficient to specify this product.
- In-line galvanizing is a much thinner controlled coating, used where ductility and other characteristics of subsequent manufacture are needed. The thinner coatings normally require supplementary coating for hard wear or corrosive exposure.
- Many products listed in the in-line galvanized Standards are provision for products only and are not stock items.
- Where steel is to be used in hard wear or corrosive service only the primary grade of galvanizing is suitable, where galvanizing service life is directly proportional to coating thickness.
- Coatings previously known by the term electroplating are now called electro-galvanizing.
Thus if long term steel protection is a prime consideration, the galvanizing charts attached are an essential reference.
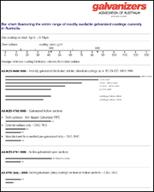
Principal Standards
AS/NZS 4680:1999
“ Hot-dip galvanized (zinc) coatings on fabricated ferrous articles”
This Standard specifies requirements and tests for hot-dip zinc coatings on fabricated ferrous articles including structural steel, steel reinforcements, steel sheet fabrications, assembled steel products, tubular fabrications, fabricated wire work, steel forgings, steel stampings, ferrous castings, nails and other small components.
This Standard is closely aligned to EN ISO 1461:1999 and is the universal Standard for the provision of After Fabrication (or general) hot dip galvanized iron and steel.
This Standard applies to both centrifuged and non-centrifuged articles.
AS/NZS 1397:2001
“ Steel sheet and strip – Hot-dip zinc coated or aluminium/zinc-coated”
This Standard specifies requirements for hot-dip zinc-coated or aluminium/zinc-coated steel sheet and strip, supplied in thickness up to and including 5.0mm.
This Standard specifies requirements for steel grades, coating classes and surface finish.
AS/NZS 4534:1998
“ Zinc and zinc/aluminium-alloy coatings on steel wire”
This Standard specifies requirements for the mass, quality and testing of zinc coatings and zinc/aluminium-alloy coatings on steel wire of circular or non-circular (shaped) cross-section. The coatings are applied in a continuous process and may be formed either by the application of molten metal or by electro deposition. Six coating mass classes are covered.
AS/NZS 4791:1999
“ Hot-dip galvanized (zinc) coatings on ferrous open sections, applied by an in-line process”
This Standard specifies requirements for the mass, quality and testing of galvanized coatings applied to ferrous open sections on all surfaces except cut ends, using an in-line process that utilizes specialized equipment.
AS/NZS 4792:1999
“ Hot-dip galvanized (zinc) coatings on ferrous hollow sections, applied by a continuous or a specialized process”
This Standard specifies requirements for mass, quality and testing of hot-dip galvanized coatings applied to –
a) Hollow sections galvanized on both surfaces in a specialized plant;
b) Hollow sections produced by welding pre-galvanized steel strip; and
c) Hollow sections galvanized on external surfaces only, using a continuous (in-line) process.
AS 4750(Int): 2000
“ Electrogalvanized (zinc) coatings on ferrous hollow sections”
This Interim Standard specifies requirements for the classification, mass, quality and testing of zinc coatings on welded hollow sections produced from Electrogalvanized strip.
AS 4751(Int): 2000
“ Electrogalvanized (zinc) coatings on ferrous open sections”
This Interim Standard specifies requirements for the classification, mass, quality and testing of zinc coatings on open sections produced from Electrogalvanized steel strip.
Specification Selection
Of the following sheet and wire standards have obvious and specific reference to their steel product groups only and are unlikely to be mistaken in use.
Confusion does arise between the other standards, which are more difficult to distinguish without details of their composition and purpose.
In this respect After Fabrication Galvanizing to AS/NZS 4680 / ISO 1461 is the primary product and is the only grade produced by static dipping, to produce a hard alloy coating of maximum available thickness. Abrasion resistance and very long service life are its engineering purposes and it is aligned to the International Standard EN ISO 1461.
Continuous and inline coating as covered in AS/NZS 4791/4792 and AS 4750 (Int) / 4751 (Int) in specially developed galvanizing processes, allow accurate control of coating thickness and in consequence, ductility, weld through characteristics, smooth finish and clean storage. This provides a range of products to suite a wide variety of subsequent manufacturing and end usage. These products should not be confused with after fabrication galvanizing.
In line products with thinner coatings often require supplementary coatings for outdoor exposure, and due consideration of product with uncoated internal surfaces.
Coating Thickness
As the longevity of a galvanized coating is proportional to the coating thickness structural specification details now involve a critical design choice as the range of coatings offered vary from 14mm to 125mm in thickness. Sheet/strip coatings of aluminium and zinc are an exception and have greater life than zinc alone.
A durability guide for galvanizing grades is also in preparation as a guide to designers and will be circulated shortly.
Source: Galvanizers Association of Australia
For more information on this source please visit Galvanizers Association of Australia