Scientists have used AI and advanced modeling to design greener cement mixes, cutting carbon emissions without sacrificing strength and offering a faster, more efficient route to sustainable construction materials.
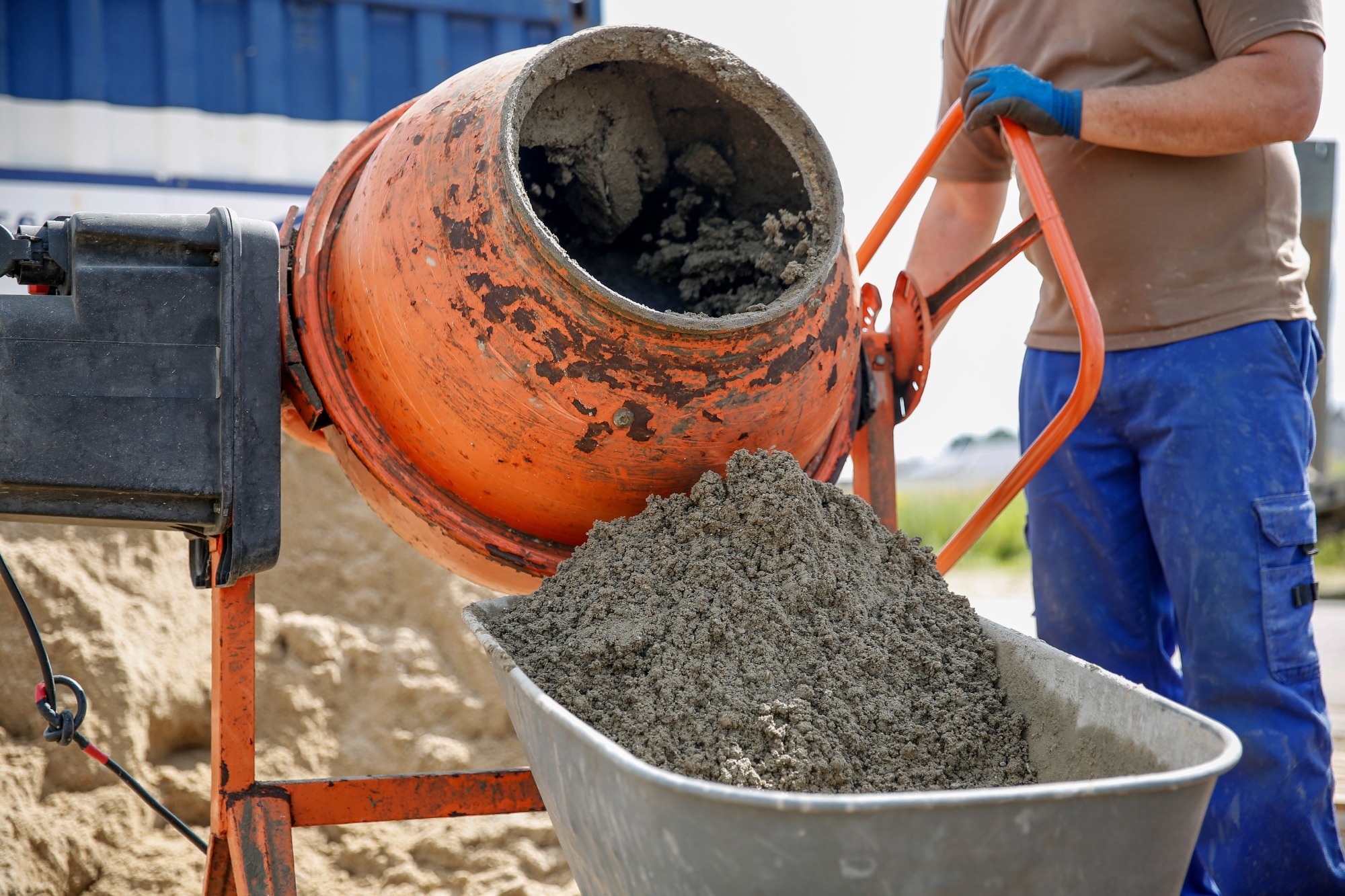
Image Credit: Tatjana Meininger/Shutterstock.com
The research, published in Materials and Structures, demonstrates how machine learning and multi-objective optimization can identify cement paste formulations that balance mechanical performance and lower environmental impact. The team trained an artificial neural network (ANN) to predict elastic moduli directly from cement recipes, dramatically speeding up what has traditionally been a slow, trial-and-error process.
Background
Designing sustainable concrete formulations requires time-consuming and costly lab testing and development. Data-driven research techniques are beginning to change that. Tools such as Response Surface Methodology have guided experimental optimization, while machine learning has helped accelerate the search for high-performance, low-carbon mixes.
However, most of these efforts have focused on optimizing concrete, rather than the cement paste itself, despite cement being the leading cause of concrete’s carbon footprint. This study addresses that gap with its new approach to optimizing clinker composition and supplementary cementitious materials (SCMs). The research aims to develop a way to reduce emissions without compromising mechanical properties.
Computational Methods
The researchers combined two advanced computational models to build a thermodynamically consistent, physics-based framework: the thermodynamic Gibbs Energy Minimization Software (GEMS) and the Self-Consistent Scheme (SCS) for elastic moduli homogenization. The combined models predicted hydrated cement paste's key elastic properties (bulk modulus K and shear modulus G).
The cement paste was modeled at Level II for analysis, accounting for homogeneous calcium-silicate-hydrates, portlandite crystals, aluminate hydrates, unhydrated clinker, and unreacted SCMs. The previously calculated elastic moduli formed the dataset for training and validating the ANN, a six-layer network with 30 neurons per layer. Once trained, the ANN could predict bulk and shear moduli much faster than the underlying physics-based model.
The team used the Non-dominated Sorting Genetic Algorithm II (NSGA-II), a well-established method for solving multi-objective optimization problems, to find the most promising formulations, implemented via the Pymoo library. This generated a Pareto front of optimal solutions offering different trade-offs between strength and emissions.
Results and Discussion
The analysis produced 100 Pareto-optimal recipes in total. Bulk modulus values in these mixes ranged from 14.61 to 23.63 GPa, while CO2 emissions per kilogram of cement varied between 0.39 and 0.76 kilograms. Formulations incorporating higher proportions of ground granulated blast furnace slag were particularly promising for reducing emissions.
The model’s predictions were validated against experimental data from published studies, focusing on samples with water-to-cement ratios of 0.40-0.50, hydration levels above 40 %, and curing ages over 14 days. The thermodynamic-physical model achieved good agreement, with a mean relative error of about 8.9 %.
The ANN trained on nearly 18,000 data points demonstrated comparable performance, with a mean error of around 11.9 % when weighed up against 56-day-old experimental samples. The researchers found that the ANN produced results around 500 times faster than the full physics-based model, with potential for even greater efficiency if more physical parameters are included.
Download your PDF copy now!
A Pathway For Sustainable Standards
The researchers believe their method provides a strong proof of concept for designing low-carbon, high-performance cement blends. The optimized recipes are consistent with emerging classifications of ternary and quaternary cement types. The model could help inform updates to national standards and codes.
Although the study focused on elasticity and CO2 emissions, the framework could include other important factors such as tensile and compressive strength, flexural behavior, durability, and cost, offering a more comprehensive picture of each mix’s real-world viability.
Journal Reference
Boiger, R. et al. (2025). Machine learning-accelerated discovery of green cement recipes. Materials and Structures, 58(5). DOI: 10.1617/s11527-025-02684-z, https://link.springer.com/article/10.1617/s11527-025-02684-
Disclaimer: The views expressed here are those of the author expressed in their private capacity and do not necessarily represent the views of AZoM.com Limited T/A AZoNetwork the owner and operator of this website. This disclaimer forms part of the Terms and conditions of use of this website.