This article provides a review of a study on the use of coal bottom ash with silica fume as an alternative for fine aggregate material in concrete. The researchers published their review in the journal Buildings.
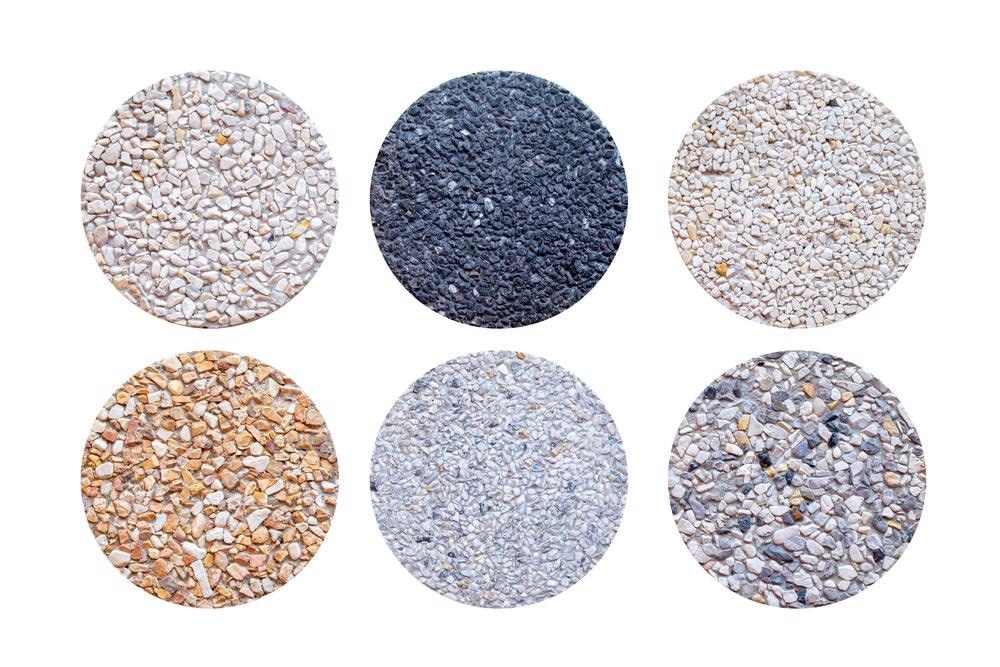
Study: Investigation on Mechanical and Durability Properties of Concrete Mixed with Silica Fume as Cementitious Material and Coal Bottom Ash as Fine Aggregate Replacement Material. Image Credit: ISEN STOCKER/Shutterstock.com
Concrete is one of the primary materials in building construction and other infrastructure projects. The large-scale use of concrete increases cement and natural aggregate usage, causing environmental stress.
Around 60–75% of concrete is occupied by fine and coarse aggregates. As both these natural materials are used extensively, there will be a scarcity of these materials in the coming years. Therefore, in a world that is facing a scarcity of river sand as well as increased infrastructure growth, there is a dire necessity to find a substitute material for river sand in concrete.
The main aim of this study was to analyze the effect of using CBA as an alternative for sand (10–30%), together with SF as a replacement for cement with various percentages ranging from 7.5–12.5%. The compressive strength and split tensile strength attributes of concrete were identified with water curing of 28- and 90-day.
Methodology
In concrete, ordinary Portland cement (OPC) of Type-I was employed as a binder and the crushed aggregate of 20 mm (maximum size) was utilized as a coarse aggregate. The hill sand served as a fine aggregate after sieving. As a partial alternative material, the CBA was used for sand.
For better understanding, SEM images of CBA and SF are shown in Figure 1. In Table 1, the chemical composition of materials employed in this research is given. As per Table 2, a concrete mix ratio of 1:2:4 with a w/c ratio of 0.5 was used for the study throughout.
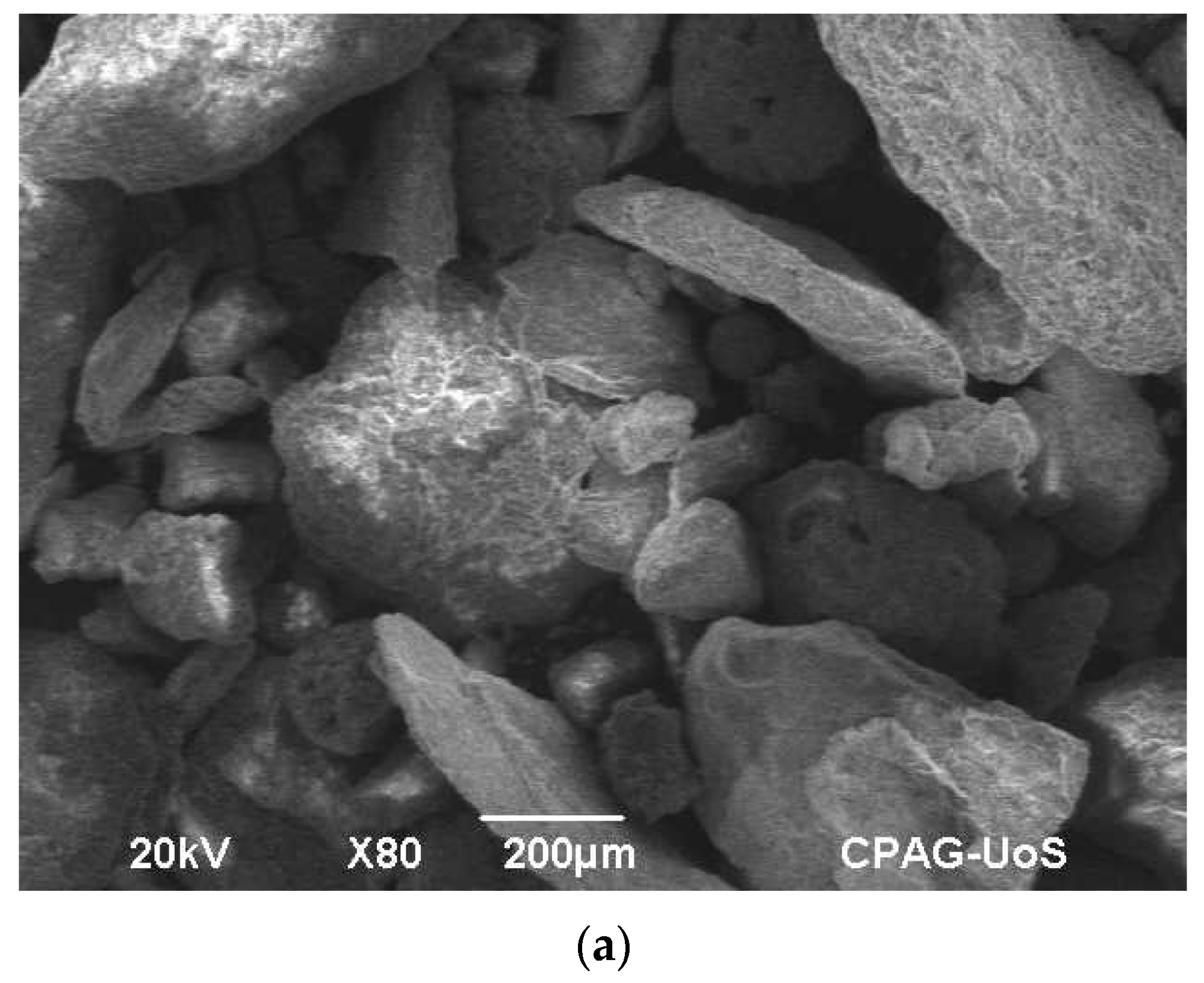
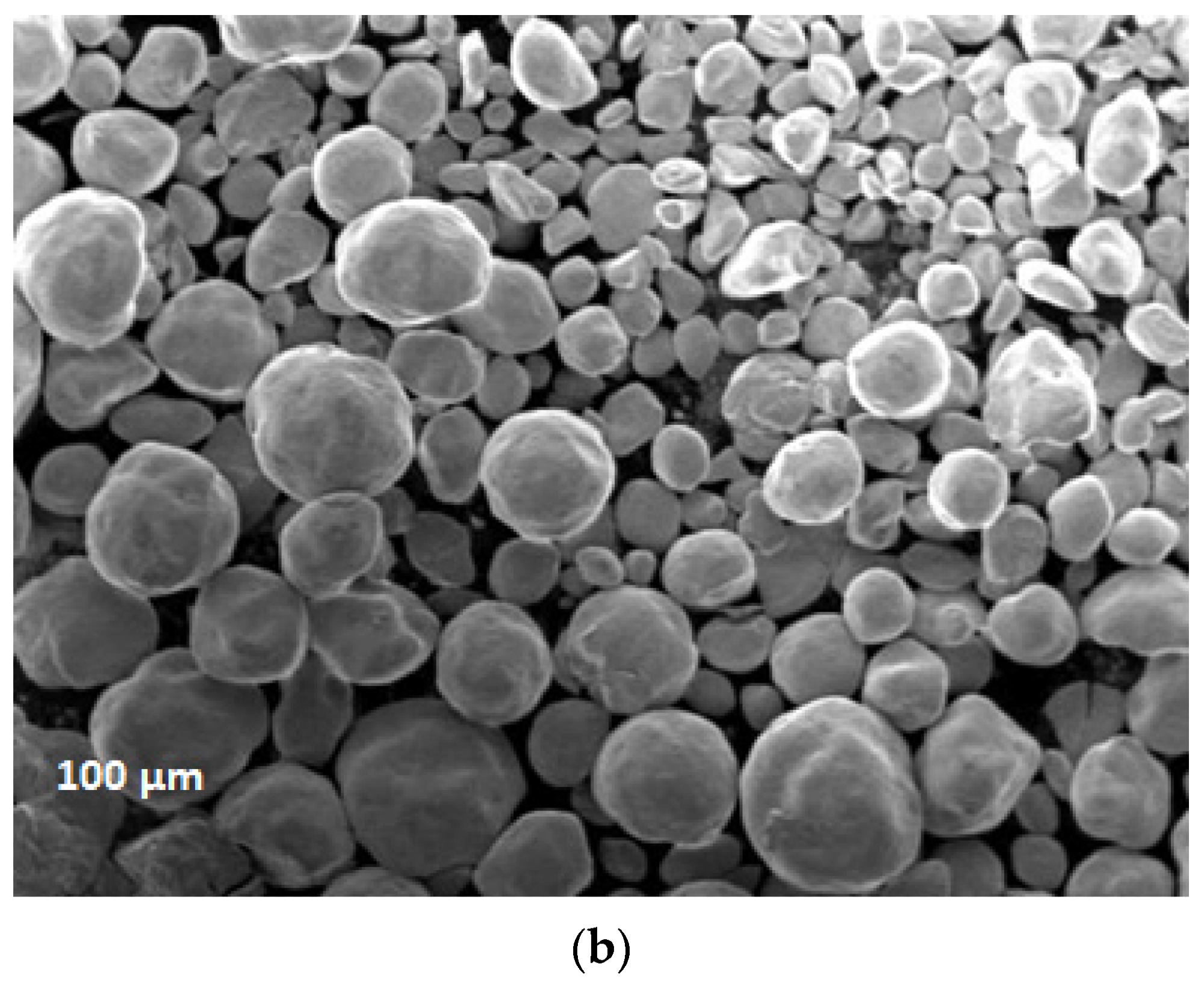
Figure 1. SEM images of (a) Coal Bottom Ash; (b) Silica Fume. Image Credit: Ali, et al., 2022
Table 1. Properties of cement and coal bottom ash. Source: Ali, et al., 2022
Material |
Physical Properties |
Chemical Analysis (% Age) |
Blaine
(cm2/g) |
Specific Gravity |
SiO2 |
CaO |
Al2O3 |
MgO |
K2O |
Fe2O3 |
LOI |
Cement |
3008 |
3.14 |
20.78 |
60.89 |
5.11 |
3.00 |
0.00 |
3.17 |
1.71 |
CBA |
- |
2.30 |
35.37 |
3.307 |
28.18 |
1.956 |
0.976 |
20.64 |
- |
Silica Fume |
- |
2.22 |
93.28 |
0.23 |
0.49 |
0.9 |
0.98 |
1.3 |
- |
Table 2. Concrete mix proportion. Source: Ali, et al., 2022
S.No |
Mix Type |
OPC
(kg) |
Sand
(kg) |
CBA
(kg) |
SF
(kg) |
C.A
(kg) |
Water
(kg) |
W/C
(kg) |
01 |
Plain |
20 |
40 |
0 |
0 |
80 |
10 |
0.5 |
02 |
10CBA |
20 |
38 |
2 |
0 |
80 |
10 |
0.5 |
03 |
20CBA |
20 |
36 |
4 |
0 |
80 |
10 |
0.5 |
04 |
30CBA |
20 |
34 |
6 |
0 |
80 |
10 |
0.5 |
05 |
7.5SF |
18.5 |
32 |
0 |
1.5 |
80 |
10 |
0.5 |
06 |
10SF |
18 |
30 |
0 |
2 |
80 |
10 |
0.5 |
07 |
12.5SF |
17.5 |
28 |
0 |
2.5 |
80 |
10 |
0.5 |
08 |
7.5SF10CBA |
18.5 |
38 |
2 |
1.5 |
80 |
10 |
0.5 |
09 |
7.5SF20CBA |
18.5 |
36 |
4 |
1.5 |
80 |
10 |
0.5 |
10 |
7.5SF30CBA |
18.5 |
34 |
6 |
1.5 |
80 |
10 |
0.5 |
11 |
10SF10CBA |
18 |
38 |
2 |
2 |
80 |
10 |
0.5 |
12 |
10SF20CBA |
18 |
36 |
4 |
2 |
80 |
10 |
0.5 |
13 |
10SF20CBA |
18 |
34 |
6 |
2 |
80 |
10 |
0.5 |
14 |
12.5SF10CBA |
17.5 |
38 |
2 |
2.5 |
80 |
10 |
0.5 |
15 |
12.5SF20CBA |
17.5 |
36 |
4 |
2.5 |
80 |
10 |
0.5 |
16 |
12.5SF20CBA |
17.5 |
34 |
6 |
2.5 |
80 |
10 |
0.5 |
To measure each concrete mix’s workability (slump test), Abram’s cone apparatus was used. After 24 hours, the concrete specimens were removed from the cone and kept in clean water for 28 and 90 days, respectively, to carry out water curing.
The compressive strength and tensile strength of samples were tested. Cylindrical specimens with a size of 100 × 200 mm were cast for the corrosion analysis test. The corrosion potential was identified based on ASTM C-876. To calculate the corrosion potential of a specimen, the mean of three specimens was used.
To calculate the sulfate resistance of concrete, the length variations of prism specimens with a size of 25 mm × 25 mm × 285 mm were employed. The prisms were de-molded and kept in a solution of sodium sulfate for 28 days. Lastly, the length change was noted with the help of a digital meter.
Results
To check the feasibility of each concrete mix, the slump test was conducted. Figure 2 illustrates the workability of the mixtures that include CBA of 10%, 20%, and 30%. It also denotes that the slump decreased with an increase in CBA percentage.

Figure 2. Workability of the mixture blended with CBA. Image Credit: Ali, et al., 2022
In addition, Figure 3 depicts the feasibility of various mixtures that contain SF and CBA in different percentages. Figure 4 illustrates the workability of mixtures containing SF as a replacement for cement with 5%, 10%, and 15%.
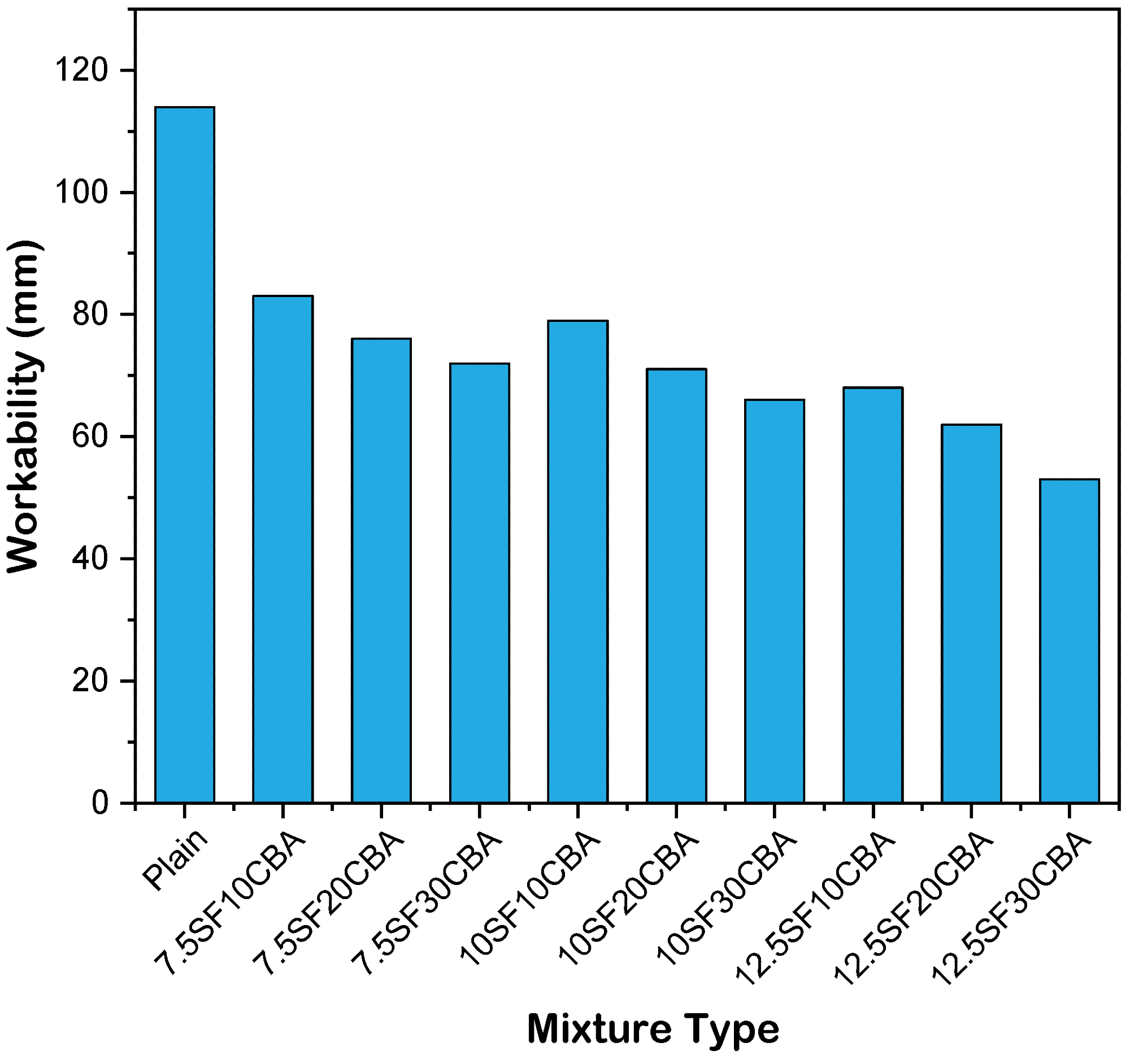
Figure 3. Workability of mixture blended with different percentages of CBA and SF. Image Credit: Ali, et al., 2022
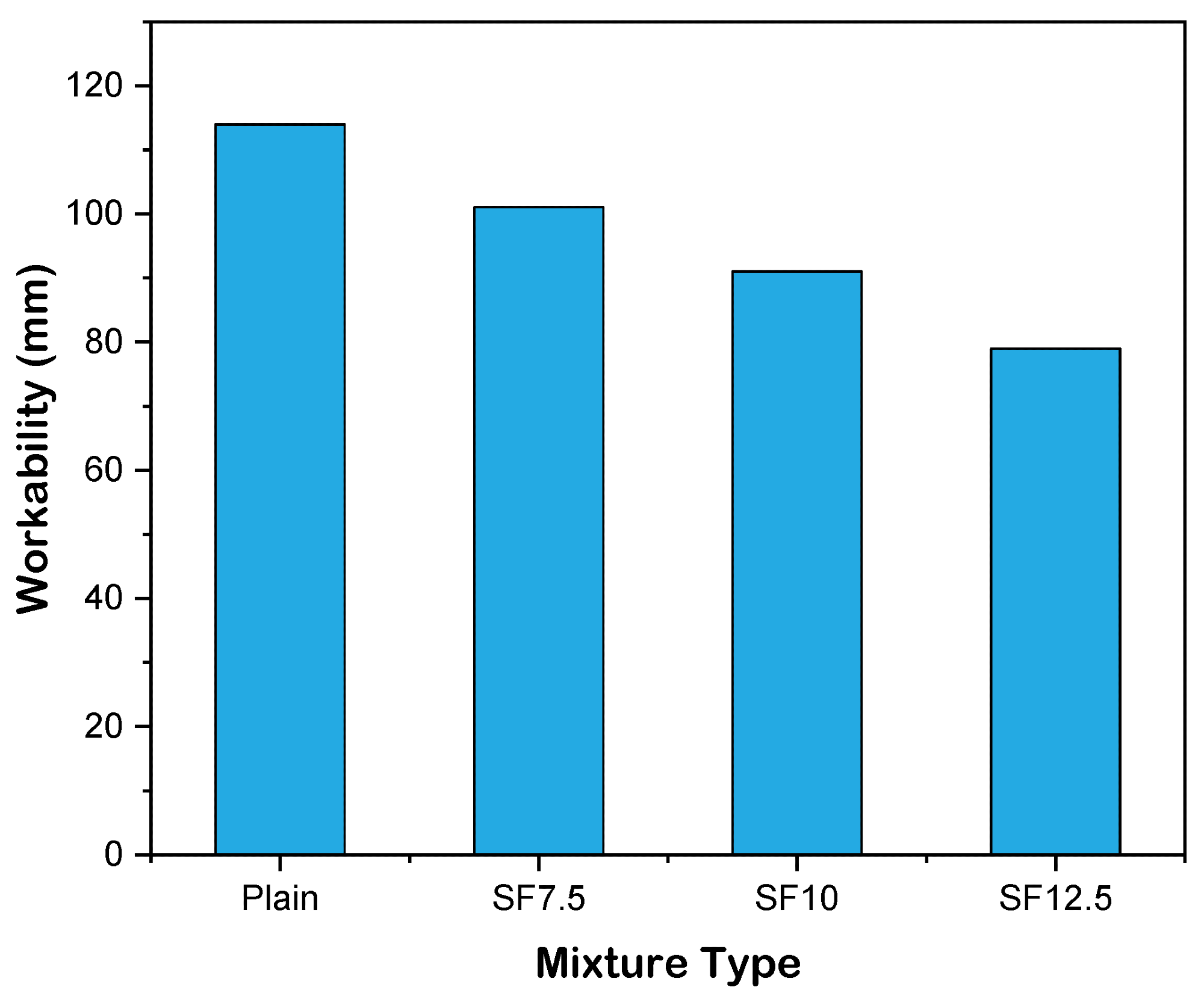
Figure 4. Workability of mixture blended with SF. Image Credit: Ali, et al., 2022
Figure 5 illustrates the compressive strength of concrete that contains different percentages of SF. The figure proves that the strength of concrete increases as the percentage of SF increases.
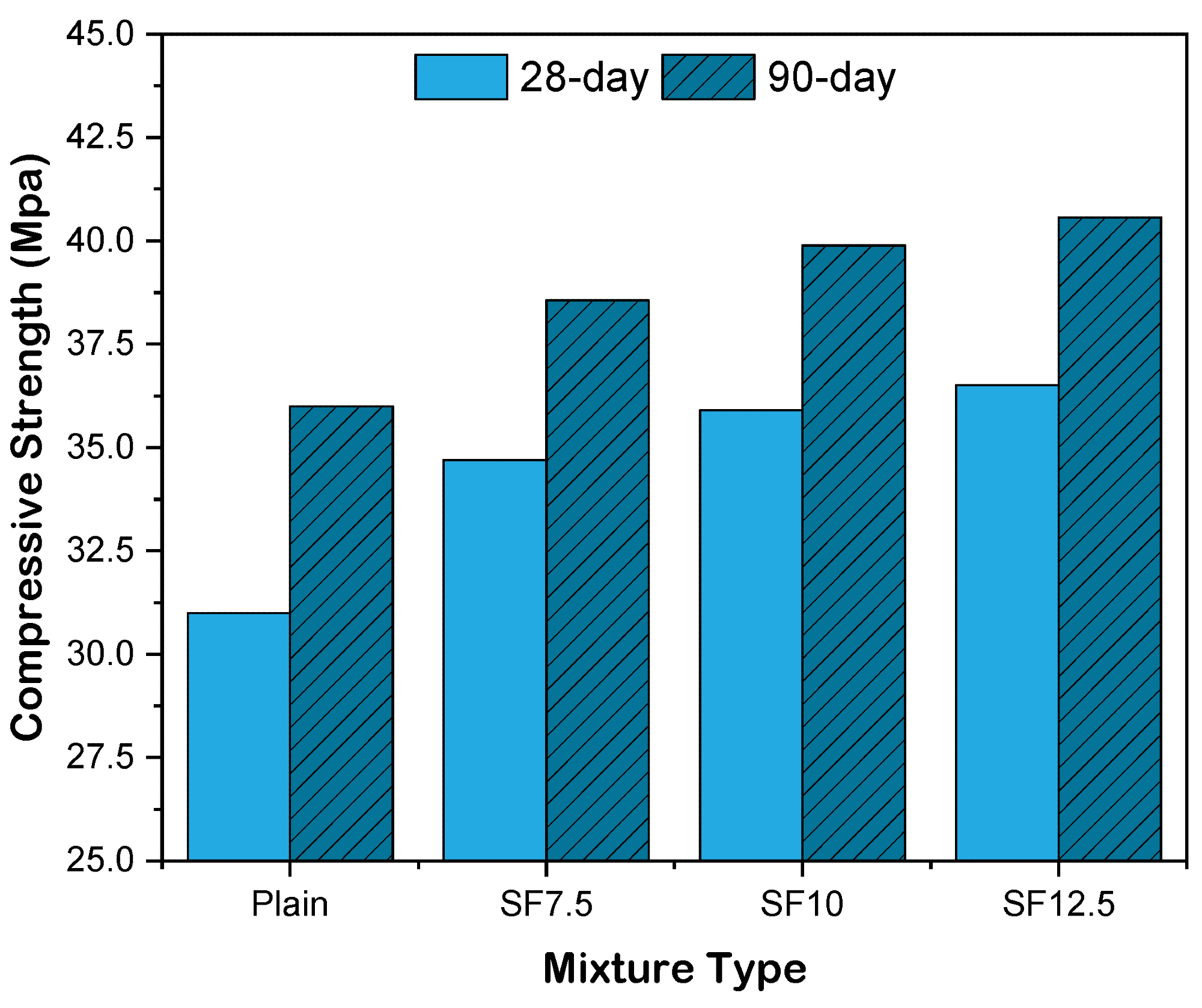
Figure 5. Compressive strength of concrete with Silica Fume. Image Credit: Ali, et al., 2022
The cylindrical compressive strength of the specimens, which contain CBA as an alternative for fine aggregates after water curing of 28- and 90-days, is depicted in Figure 6.
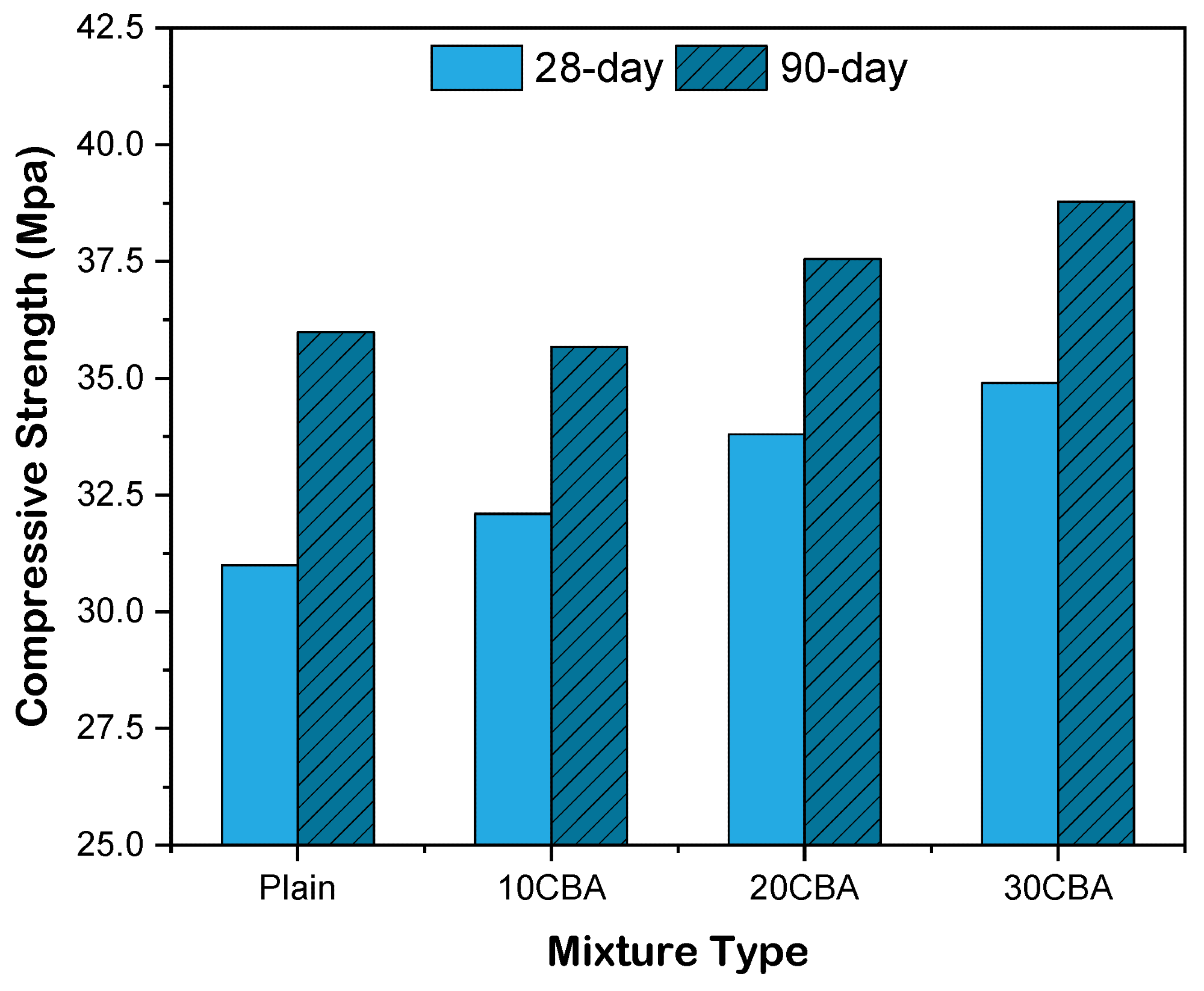
Figure 6. Compressive strength of concrete mixed with CBA. Image Credit: Ali, et al., 2022
The compressive strength of concrete with different mixtures of CBA and SF is depicted in Figure 7.
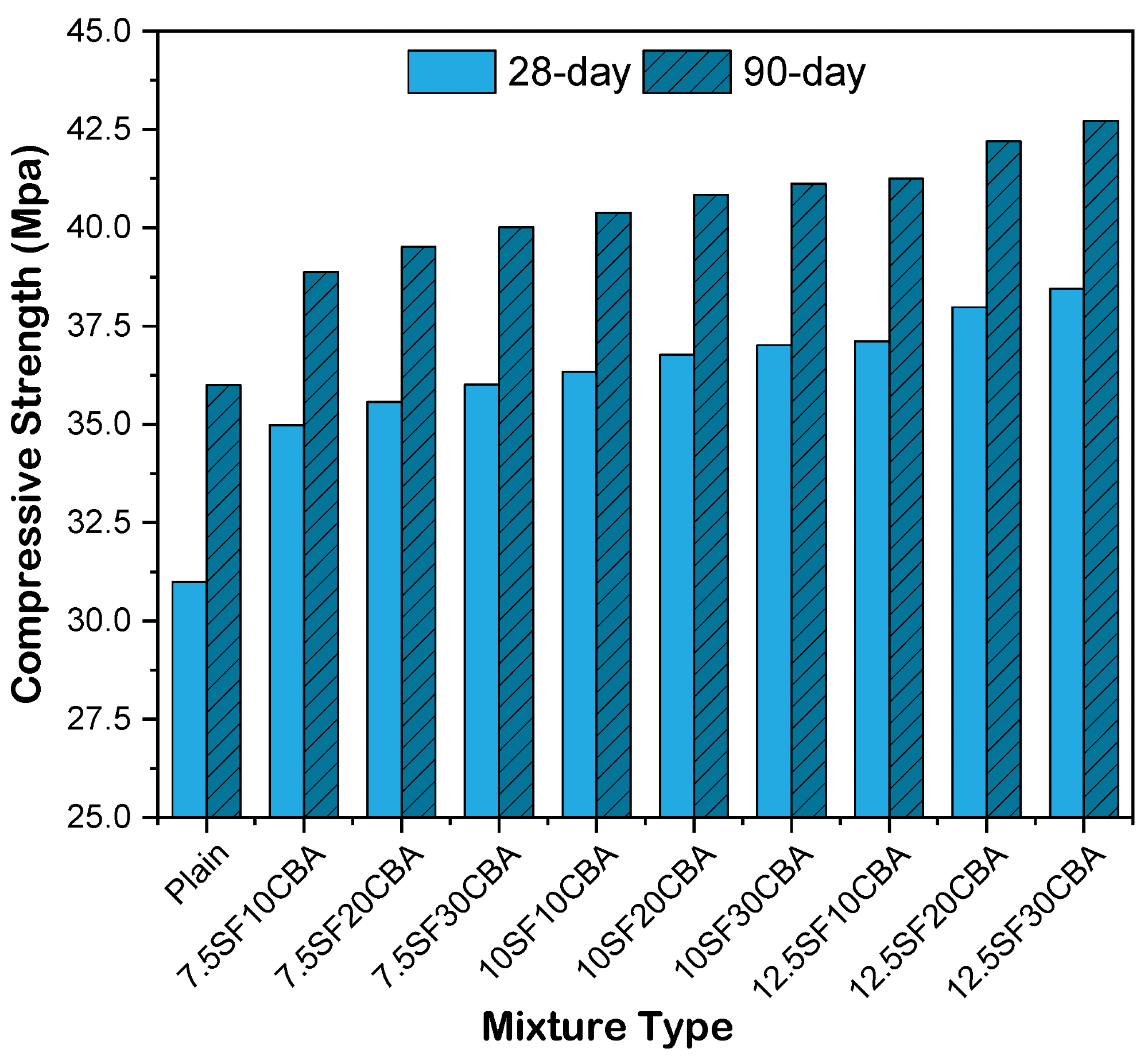
Figure 7. Compressive strength of concrete mixed CBA and SF. Image Credit: Ali, et al., 2022
Figure 8 illustrates the tensile strength of concrete that contains SF after 28- and 90-day water curing, whereas Figure 9 illustrates the tensile strength of concrete with various percentages of CBA.
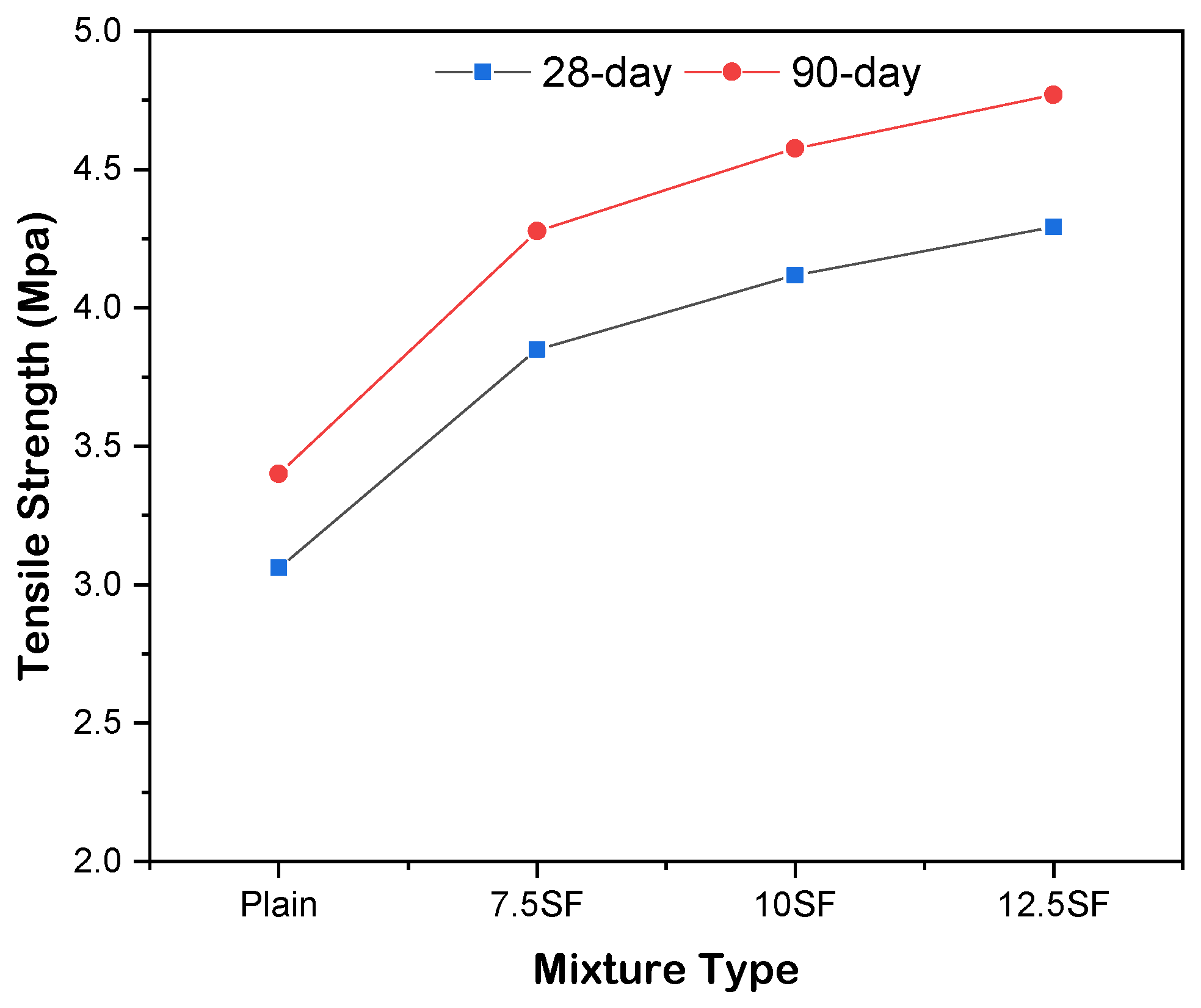
Figure 8. Tensile Strength of concrete mixed with SF. Image Credit: Ali, et al., 2022
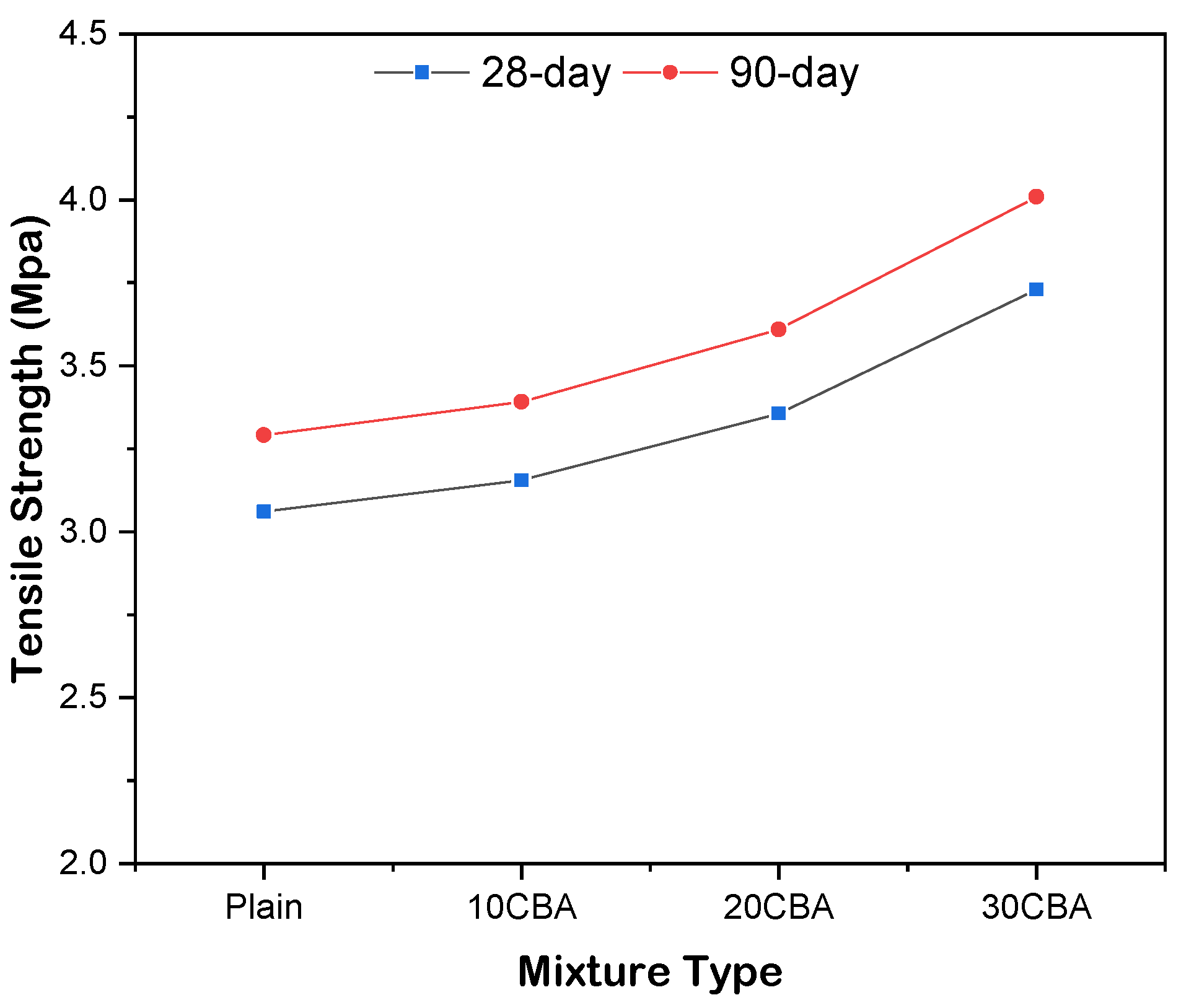
Figure 9. Tensile Strength of concrete mixed with CBA. Image Credit: Ali, et al., 2022
Figure 10 depicts the split tensile strength of concrete combined with different amounts of SF (7.5–12.5%) and CBA (10–30%).
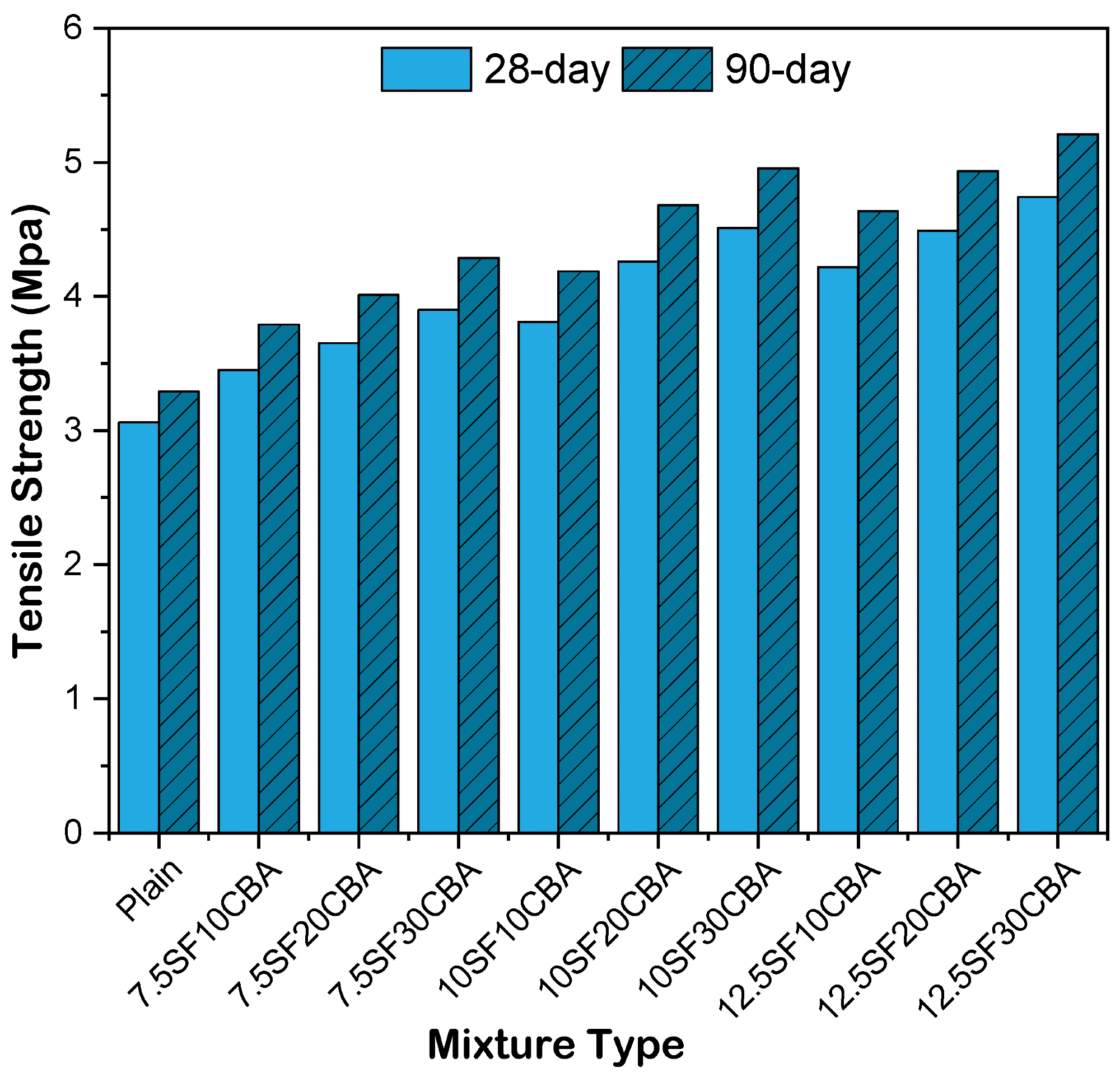
Figure 10. Tensile Strength of concrete mixed with CBA and SF. Image Credit: Ali, et al., 2022
The study shows that the increase in CBA and SF decreases the penetration of chloride within the concrete mass while enhancing the internal resistance of concrete. Figure 11 and Table 3 show that when the CBA percentage was increased, the resistance to chloride ions was also found to increase.
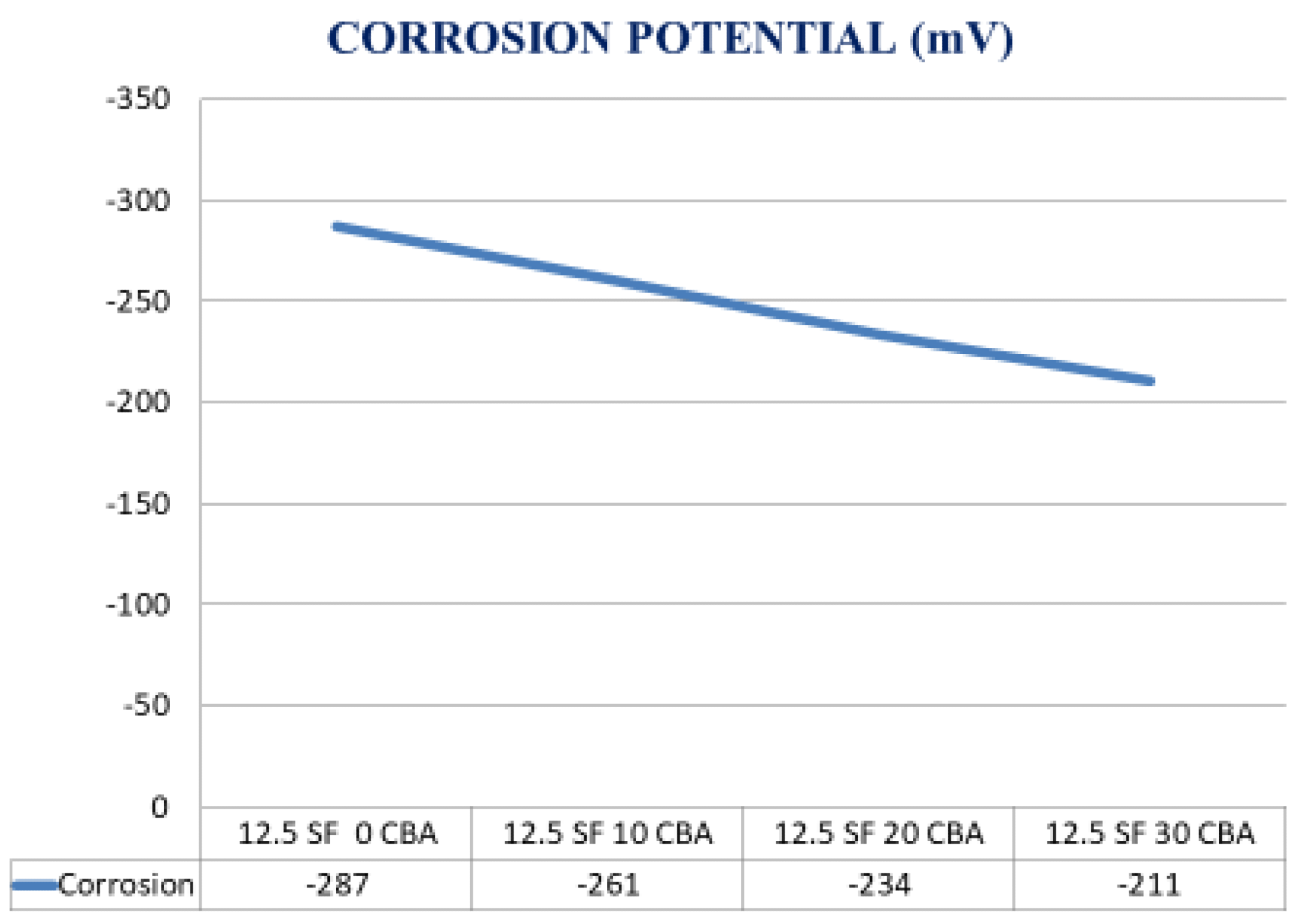
Figure 11. Corrosion Potential mV. Image Credit: Ali, et al., 2022
Table 3. Corrosion analysis of 90-Day’s sodium chloride solution. Source: Ali, et al., 2022
Sr. |
CBA and SF % Replacement |
Corrosion Potential (mV) |
M 1 |
12.5 SF 0 CBA |
−287 |
M 2 |
12.5 SF 10 CBA |
−261 |
M 3 |
12.5 SF 20 CBA |
−234 |
M 4 |
12.5 SF 30 CBA |
−211 |
Usage of SF and CBA in the concrete matrix offers outstanding resistance to sulfate attack. Table 4 shows that the increase in CBA improves resistance to sulfate attack.
Table 4. Sulfate Attack of 28-Days in sodium sulfate solution (Na2SO4). Source: Ali, et al., 2022
Sr.No |
CBA % Replacement |
Initial Length (mm) |
Final Length (mm) |
% Increment |
M 1 |
12.5 SF 0 CBA |
285.2 ± 0.03 |
286.7 ± 0.04 |
0.52 |
M 2 |
12.5 SF 10 CBA |
285.4 ± 0.04 |
286.5 ± 0.05 |
0.39 |
M 3 |
12.5 SF 20 CBA |
285.7 ± 0.02 |
286.7 ± 0.04 |
0.35 |
M 4 |
12.5 SF 30 CBA |
285.0 ± 0.05 |
285.9 ± 0.05 |
0.32 |
Conclusion
This study concludes that CBA can be an ideal substitute material for fine aggregate in the concrete mix with SF. The successful use of CBA in large volumes as a sand and gravel substitute will reduce the use of natural fine and coarse materials.
SF, with its low-carbon content, is beneficial in generating high-quality pozzolanic reactions. It also serves as an additional binder element in the concrete hardening process.
The study depicts that replacing conventional concrete mixture with 30% CBA and 12.5% SF showed commendable mechanical and durability properties. Also, these mixtures tend to exhibit notable economic and environmental benefits.
Journal Reference:
Ali, T., Buller, A. S., Abro, F. U. R., Ahmed, Z., Shabbir, S., Lashari, A. R., Hussain, G. (2022) Investigation on Mechanical and Durability Properties of Concrete Mixed with Silica Fume as Cementitious Material and Coal Bottom Ash as Fine Aggregate Replacement Material. Buildings, 12(1), p. 44. Available Online: https://www.mdpi.com/2075-5309/12/1/44/htm.
References and Further Reading
- Rafieizonooz, M., et al. (2016) Investigation of coal bottom ash and fly ash in concrete as replacement for sand and cement. Construction and Building Materials, 116, pp. 15–24. doi.org/10.1016/j.conbuildmat.2016.04.080.
- Humphreys, K & Mahasenan, M (2002) Towards a Sustainable Cement Industry. Substudy 8: Climate Change; World Buisness Council for Sustainable Development: Geneva, Switzerland.
- Buller, A. S., et al. (2019) Mechanical Recovery of Cracked Fiber-Reinforced Mortar Incorporating Crystalline Admixture, Expansive Agent, and Geomaterial. Advances in Materials Science and Engineering. doi.org/10.1155/2019/3420349.
- Abro, F.u.R., et al. (2021) Autogenous Healing of Cracked Mortar Using Modified Steady-State Migration Test against Chloride Penetration. Sustainability, 13, p. 9519. doi.org/10.3390/su13179519.
- Mardani-Aghabaglou, A., et al. (2015) Mechanical and durability performance of concrete incorporating fine recycled concrete and glass aggregates. Materials and Structures, 48, pp. 2629–2640. doi.org/10.1617/s11527-014-0342-3.
- Singh, M & Siddique, R (2014) Strength properties and micro-structural properties of concrete containing coal bottom ash as partial replacement of fine aggregate. Construction and Building Materials, 50, pp. 246–256. doi.org/10.1016/j.conbuildmat.2013.09.026.
- Argiz, C., et al. (2018) Use of ground coal bottom ash as cement constituent in concretes exposed to chloride environments. Journal of Cleaner Production, 170, pp. 25–33. doi.org/10.1016/j.jclepro.2017.09.117.
- Singh, M & Siddique, R (2016) Effect of coal bottom ash as partial replacement of sand on workability and strength properties of concrete. Journal of Cleaner Production, 112, pp. 620–630. doi.org/10.1016/j.jclepro.2015.08.001.
- Singh, N., et al. (2018) Influence of coal bottom ash as fine aggregates replacement on various properties of concretes: A review. Resources, Conservation and Recycling, 138, pp. 257–271. doi.org/10.1016/j.resconrec.2018.07.025.
- Siddique, R & Cachim, P (2018) Waste and Supplementary Cementitious Materials in Concrete: Characterisation, Properties and Applications; Woodhead Publishing: Cambridge, UK. ISBN 0081021577.
- Kim, H K & Lee, H K (2011) Use of power plant bottom ash as fine and coarse aggregates in high-strength concrete. Construction and Building Materials, 25, pp. 1115–1122. doi.org/10.1016/j.conbuildmat.2010.06.065.
- Ghafoori, N & Bucholc, J (1996) Investigation of lignite-based bottom ash for structural concrete, Journal of Materials in Civil Engineering, 8, pp. 128–137. doi.org/10.1061/(ASCE)0899-1561.
- Ghafoori, N & Buchole, J (1997) Properties of High-Calcium Dry Bottom Ash for Structural Concrete. Journal of Materials Science, 94, pp. 90–101.
- Bai, Y., et al. (2005) Strength and drying shrinkage properties of concrete containing furnace bottom ash as fine aggregate. Construction and Building Materials, 19, pp. 691–697. doi.org/10.1016/j.conbuildmat.2005.02.021.
- Kou, S C & Poon, C S (2009) Properties of concrete prepared with crushed fine stone, furnace bottom ash and fine recycled aggregate as fine aggregates. Construction and Building Materials, 23, pp. 2877–2886. doi.org/10.1016/j.conbuildmat.2009.02.009.
- Liao, W., et al. (2019) Hydration of Binary Portland Cement Blends Containing Silica Fume: A Decoupling Method to Estimate Degrees of Hydration and Pozzolanic Reaction. Frontiers in Materials, 6, p. 78. doi.org/10.3389/fmats.2019.00078.
- Duval, R & Kadri, E H (1998) Influence of silica fume on the workability and the compressive strength of high-performance concretes. Cement and Concrete Research, 28, pp. 533–54. doi.org/10.1016/S0008-8846(98)00010-6.
- Sanjuán, M. Á., et al. (2015) Effect of silica fume fineness on the improvement of Portland cement strength performance. Construction and Building Materials, 96, pp. 55–64. doi.org/10.1016/j.conbuildmat.2015.07.092.
- De Belie, N., et al. (2017) Properties of Fresh and Hardened Concrete Containing Supplementary Cementitious Materials: State-of-the-Art Report of the RILEM Technical Committee 238-SCM, Working Group 4; Springer: Berlin/Heidelberg, Germany. Volume 25: ISBN 3319706063.
- Yang, J., et al. (2017) Influence of Curing Time on the Drying Shrinkage of Concretes with Different Binders and Water-to-Binder Ratios. Advances in Materials Science and Engineering, 2017, pp. 1–10. doi.org/10.1155/2017/2695435.
- Sharaky, I. A., et al. (2019) The influence of silica fume, nano silica and mixing method on the strength and durability of concrete. SN Applied Sciences, 1, pp. 1–10. doi.org/10.1007/s42452-019-0621-2.
- Toutanji, H., et al. (2004) Effect of supplementary cementitious materials on the compressive strength and durability of short-term cured concrete. Cement and Concrete Research, 34, pp. 311–319. doi.org/10.1016/j.cemconres.2003.08.017.
- Wille, K., et al. (2014) Properties of strain hardening ultra high performance fiber reinforced concrete (UHP-FRC) under direct tensile loading. Cement and Concrete Composites, 48, pp. 53–66. doi.org/10.1016/j.cemconcomp.2013.12.015.
- Arora, A., et al. (2018) Microstructural packing- and rheology-based binder selection and characterization for Ultra-high Performance Concrete (UHPC). Cement and Concrete Research, 103, pp. 179–190. doi.org/10.1016/j.cemconres.2017.10.013.
- Bheel, N., et al. (2021) An investigation on fresh and hardened properties of concrete blended with rice husk ash as cementitious ingredient and coal bottom ash as sand replacement material. Silicon, pp. 1–12. doi.org/10.1007/s12633-020-00906-3.
- ASTM C618 (2003) Standard specification for coal fly ash and raw or calcined natural pozzolan for use in concrete. In American Society for Testing and Materials; ASTM International: West Conshohocken, PA, USA.
- ASTM International (2003) Standard Test Method for Corrosion Potentials of Uncoated Reinforcing Steel in Concrete; ASTM International: West Conshohocken, PA, USA, 2003.
- ASTM C1012/C1012M-12 Standard test method for length change of hydraulic-cement mortars exposed to a sulfate solution, ASTM International: West Conshohocken, PA, USA.
- Kurama, H & Kaya, M (2008) Usage of coal combustion bottom ash in concrete mixture. Construction and Building Materials, 22, pp. 1922–1928. doi.org/10.1016/j.conbuildmat.2007.07.008.
- Mangi, S. A., et al. (2019) Effects of ground coal bottom ash on the properties of concrete, Journal of Engineering Science and Technology, 14, pp. 338–350. Available at: https://core.ac.uk/download/pdf/188217821.pdf.
- Singh, M & Siddique, R (2013) Effect of coal bottom ash as partial replacement of sand on properties of concrete. Resources, Conservation and Recycling, 72, pp. 20–32. doi.org/10.1016/j.resconrec.2012.12.006.
- Abidin, N. E. Z., et al. (2014) The effect of bottom ash on fresh characteristic, compressive strength and water absorption of self-compacting concrete. In Applied Mechanics and Materials; Trans Tech Publications Ltd.: Stafa-Zurich, Switzerland, 660, pp. 145–151. doi.org/10.4028/www.scientific.net/AMM.660.145.
- Keerio, M. A., et al. (2020) Effect of silica fume as cementitious material and waste glass as fine aggregate replacement constituent on selected properties of concrete. Silicon, pp. 1–12. doi.org/10.1007/s12633-020-00806-6.
- Almusallam, A. A., et al. (2004) Effect of silica fume on the mechanical properties of low quality coarse aggregate concrete. Cement and Concrete Composites, 26, pp. 891–900. doi.org/10.1016/j.cemconcomp.2003.09.003.
- Behnood, A & Ziari, H (2008) Effects of silica fume addition and water to cement ratio on the properties of high-strength concrete after exposure to high temperatures. Cement and Concrete Composites, 30, pp. 106–112. doi.org/10.1016/j.cemconcomp.2007.06.003.
- Hasim, A. M., et al. (2021) Properties of high volume coal bottom ash in concrete production. Materials Today Proceedings, 48(6), pp. 1861–1867. doi.org/10.1016/j.matpr.2021.09.250.
- Roy, D K S & Sil, A (2012) Effect of partial replacement of cement by silica fume on hardened concrete. International Journal of Emerging Technology and Advanced Engineering, 2, pp. 472–475.
- Hanumesh, B. M., et al. (2015) The mechanical properties of concrete incorporating silica fume as partial replacement of cement. International Journal of Emerging Technology and Advanced Engineering, 5, p. 270.
- Yazıcı, H (2008) The effect of silica fume and high-volume Class C fly ash on mechanical properties, chloride penetration and freeze–thaw resistance of self-compacting concrete. Construction and Building Materials, 22, pp. 456–462. doi.org/10.1016/j.conbuildmat.2007.01.002.
- Detwiler, R. J., et al. (1994) Use of supplementary cementing materials to increase the resistance to chloride ion penetration of concretes cured at elevated temperatures. Journal of Materials Science, 91, pp. 63–66.
- Al-Saadoun, S S & Al-Gahtani, A S (1992) Reinforcement corrosion-resisting characteristics of silica-fume blended-cement concrete, Journal of Materials Science, 89, pp. 337–344.
- Berke, N S (1989) Resistance of microsilica concrete to steel corrosion erosion and chemical attack. Special Publications, 114, pp. 861–886.
- Khedr, S A & Idriss, A F (1995) Resistance of silica-fume concrete to corrosion-related damage. Journal of Materials in Civil Engineering, 7, pp. 102–107. doi.org/10.1061/(ASCE)0899-1561(1995)7:2(102).
- Singh, M & Siddique, R (2014) Compressive strength, drying shrinkage and chemical resistance of concrete incorporating coal bottom ash as partial or total replacement of sand. Construction and Building Materials, 68, pp. 39–48. doi.org/10.1016/j.conbuildmat.2014.06.034.
- Ghafoori, N & Cai, Y (1998) Laboratory-made roller compacted concretes containing dry bottom ash: Part ii—long-term durability. Journal of Material Science, 95, pp. 244–251.
- Ghafoori, N & Cai, Y (1998) Laboratory-Made RCC containing Dry Bottom Ash: Part I—Mechanical Properties. Journal of Material Science, 95, pp. 121–130.
- Mangat, P S & Khatib, J M (1993) Influence of fly ash, silica fume, and slag on sulfate resistance of concrete. Journal of Material Science, 92, pp. 542–552.
- Cohen, M D & Bentur, A (1988) Durability of portland cement-silica fume pastes in magnesium and sodium sulfate solutions. Journal of Materials Science, 85, pp. 148–157.
- Mangi, S. A., et al. (2019) Short-term effects of sulphate and chloride on the concrete containing coal bottom ash as supplementary cementitious material. Engineering Science and Technology, an International Journal, 22, pp. 515–522. doi.org/10.1016/j.jestch.2018.09.001.