The construction industry is experiencing poor profit margins and falling orders, and there is a dire need to improve its productivity. Research in the journal Buildings takes a look at modular building as a means of reducing emissions and increasing productivity, using South Korea as a case study.
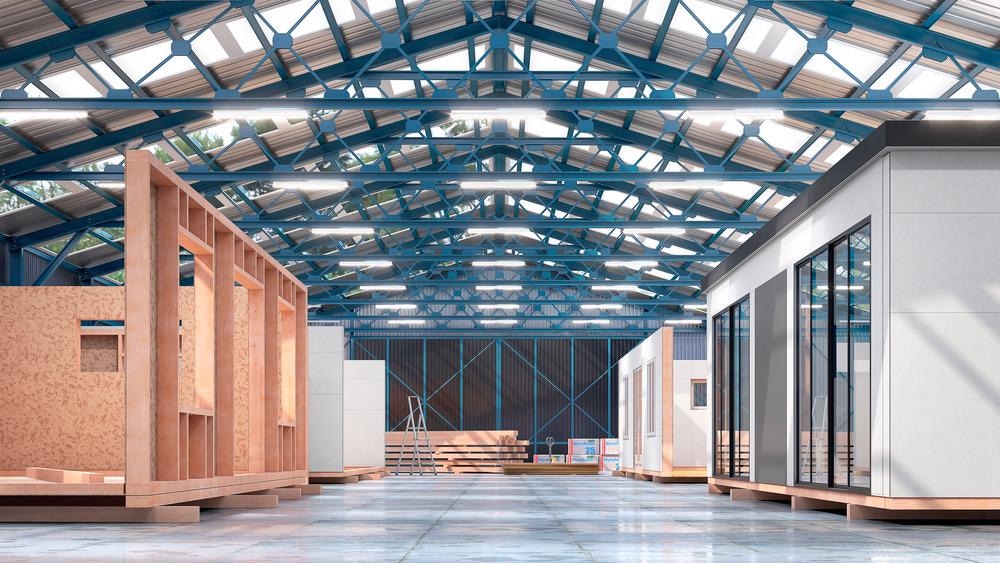
Study: Comparison of the Embodied Carbon Emissions and Direct Construction Costs for Modular and Conventional Residential Buildings in South Korea. Image Credit: vipman/Shutterstock.com
Construction corporations have started showing a substantial interest in modular construction methods, in which units are built under protected conditions in factories and then transported to a location for assembly and construction. Modular construction—a technology-intensive dry construction method—enhances construction efficiency and productivity.
New research in the journal Buildings analyzes the embodied carbon emissions and direct construction cost for a modular residential building’s production phase, and compares the findings with those of a conventional residential building. The study focuses on the material production phase, as it is reported that this phase results in increased embodied carbon emissions when compared to project stages.
Individual modules are assembled into the final building on-site using one of the modular construction approaches illustrated in Figure 1:
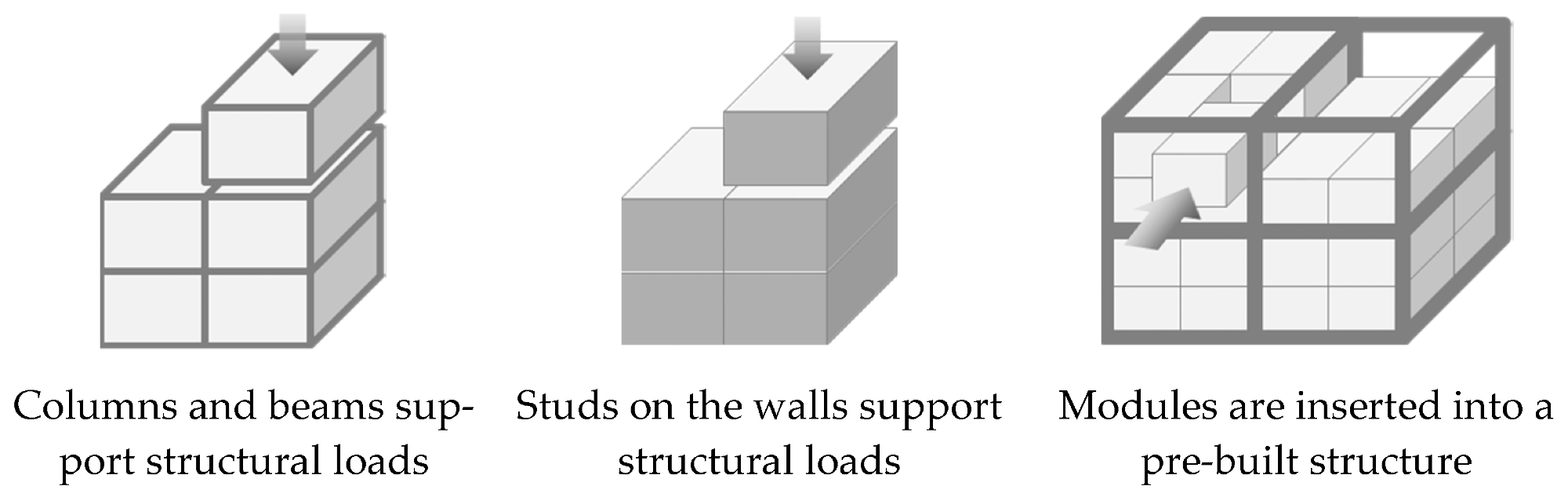
Figure 1. Modular construction methods, adapted from ref. Image Credit: Jang, et al., 2022
Enhanced quality, a quicker construction period, and sustainable building methods are three main advantages of modular construction, as modules can be produced in the factory next to the foundation work that is being performed at the site, thereby reducing the overall construction period and cost. Lastly, modular construction offers environmental advantages, with reduced use of on-site wet construction methods.
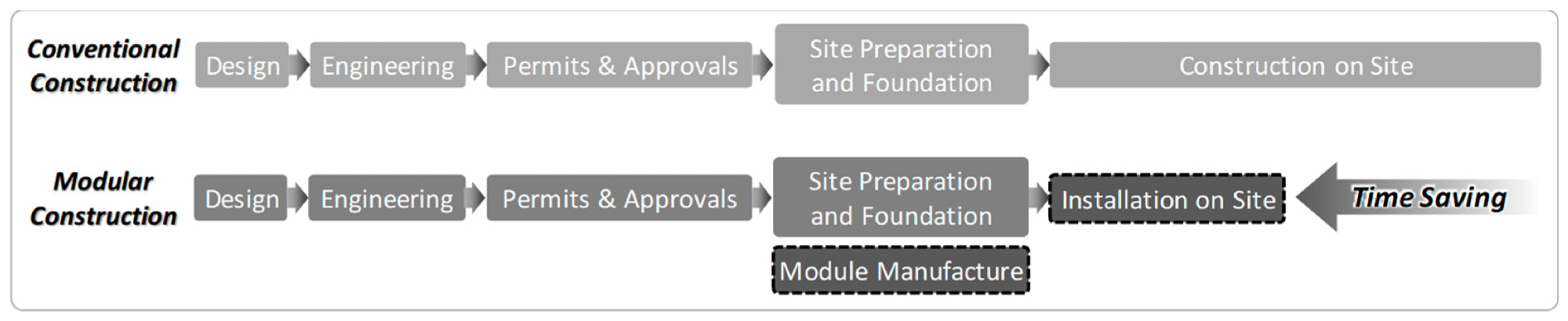
Figure 2. Comparison of modular and conventional RC construction methods, adapted from ref. Image Credit: Jang, et al., 2022
The scientists performed an environmental impact analysis and economic assessment of modular construction material production phases. For this method, a study was designed and performed to compensate for the lack of existing research.
Methodology
A modular residential building was analyzed for this study. Table 1 and Figure 3 present an overview and the front view of the project.
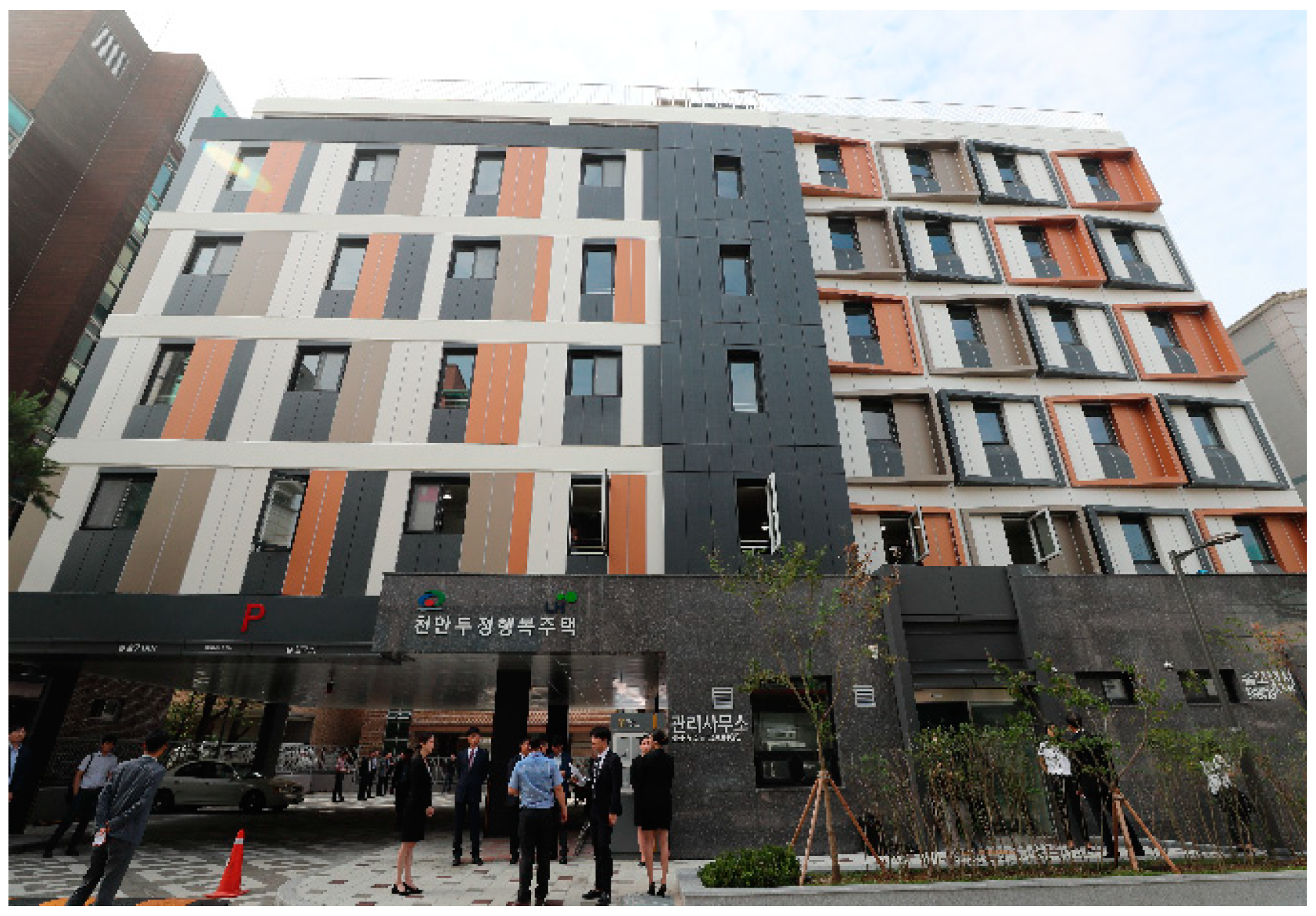
Figure 3. Front view of target building. Image Credit: Jang, et al., 2022
Table 1. Project overview. Source: Jang, et al., 2022
Division |
Contents |
B-Wing |
C-Wing |
Project |
1st District of Public Housing in Cheonan Dujeong District |
Supply Area |
485.80 m2 |
653.32 m2 |
No. of Households |
20 households |
20 households |
Floors |
B1F–6F |
Structure |
B1F–1F |
RC (A-wing) |
2F–6F |
Modular (B-wing, C-wing) |
As depicted in Figure 4, the building is divided into three areas. However, for this study, only the B-wing that was constructed using a column and beam support structure was chosen for examination and compared to the same residential building.
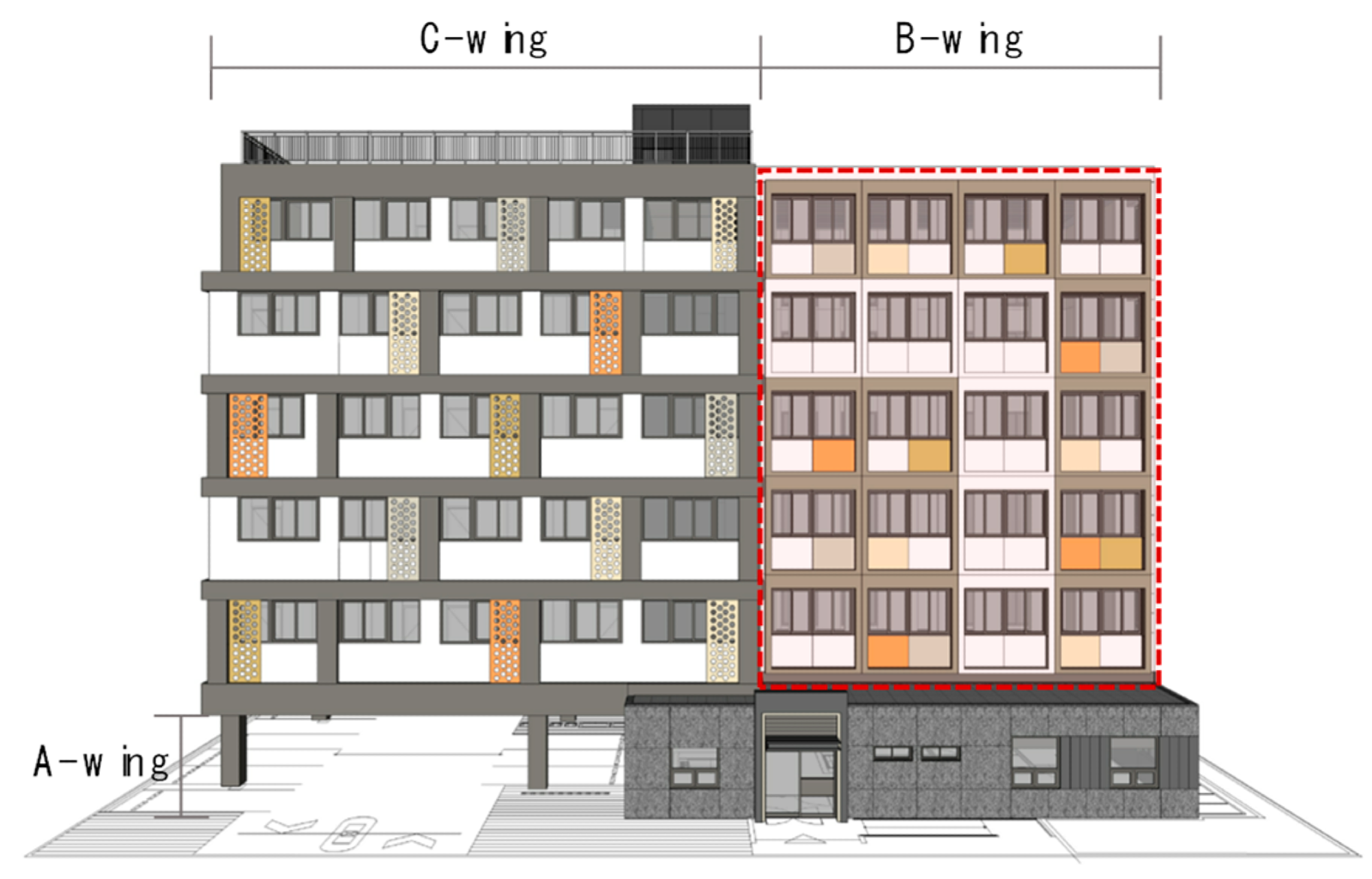
Figure 4. Division of target building. Image Credit: Jang, et al., 2022
The study examined the embodied carbon emissions produced during the production stage depending on the major construction materials. The embodied carbon emissions produced by construction materials and used for residential buildings as an outcome of modular and RC construction methods are compared in Table 2.
Table 2. Quantity of major construction material using the two building systems. Source: Jang, et al., 2022
Materials |
Unit |
Modular |
Reinforced Concrete |
RMC |
ton |
210.96 |
814.20 |
Steel |
ton |
53.65 |
- |
Gypsum Board |
ton |
42.38 |
2.25 |
Metal |
ton |
22.90 |
11.41 |
Sand |
ton |
13.01 |
46.40 |
Rebar |
ton |
7.28 |
24.56 |
Table 3 lists the factors of embodied carbon emission in the production stage for various major construction components.
Table 3. Embodied carbon emission factors in the production phase for major construction materials. Source: Jang, et al., 2022
Material |
Material Characteristics |
Units |
Embodied Carbon Emission Factor |
RMC |
24 MPa |
kg-CO₂/m3 |
414 |
18 MPa |
kg-CO₂/m3 |
409 |
Steel |
Channel |
kg-CO₂/kg |
0.404 |
Glass |
Double Glazing |
kg-CO₂/m2 |
22.4 |
Gypsum Board |
- |
kg-CO₂/kg |
0.138 |
Rebar |
- |
kg-CO₂/kg |
0.438 |
Block |
- |
kg-CO₂/kg |
0.123 |
Tile |
|
kg-CO₂/kg |
0.353 |
Cement |
- |
kg-CO₂/kg |
1.060 |
Sand |
- |
kg-CO₂/m3 |
3.870 |
Table 4 presents the unit costs of key construction elements.
Table 4. Unit material cost of major construction materials. Source: Jang, et al., 2022
Material |
Unit |
Material Cost * |
RMC |
24 MPa |
USD/m3 |
50.9 |
18 MPa |
USD/m3 |
45.3 |
Steel |
Hot Rolled Steel |
USD/ton |
645.2 |
Channel |
USD/ton |
661.3 |
Glass |
Double Glazing, 16 mm |
USD/m2 |
18.2 |
Double Glazing, 22 mm |
USD/m2 |
22.8 |
Gypsum Board |
Fireproof Board |
USD/m2 |
6.0 |
Rebar |
SD400, HD10 |
USD/ton |
542.9 |
SD400, HD13 |
USD/ton |
535.2 |
Block |
190 mm × 57 mm × 90 mm |
USD/each |
0.04 |
Tile |
Porcelain Tile |
USD/m2 |
6.9 |
Porcellaneous Tile |
USD/m2 |
7.3 |
Cement |
Ordinary Portland Cement |
USD/pack (40 kg) |
2.8 |
Sand |
- |
USD/m3 |
23.4 |
* 1 United States Dollar (USD) = 1240 Korea Won (KRW).
Results and Discussion
The results of the analysis of the embodied carbon emissions of the key construction materials employed in this study are shown in Table 5.
Table 5. Results of the assessment of the embodied carbon emissions. Source: Jang, et al., 2022
Materials |
Modular (B-Wing) |
Reinforced Concrete |
Embodied Carbon Emissions (kg-CO₂) |
Proportion (%) |
Embodied Carbon Emissions (kg-CO₂) |
Proportion (%) |
Metal |
47,961 |
35.32 |
24,793 |
11.66 |
RMC |
37,967 |
27.96 |
146,506 |
68.92 |
Steel |
29,719 |
21.89 |
- |
- |
Glass |
6238 |
4.59 |
8047 |
3.79 |
Gypsum Board |
5849 |
4.31 |
310 |
0.15 |
Cement |
4236 |
3.12 |
19,886 |
9.36 |
Rebar |
3191 |
2.35 |
10,757 |
5.06 |
Tile |
474 |
0.35 |
1669 |
0.79 |
Block |
121 |
0.09 |
408 |
0.19 |
Sand |
31 |
0.02 |
112 |
0.05 |
Stone |
- |
- |
71 |
0.03 |
Total |
135,787 |
100 |
212,559 |
100 |
Per m2 |
279.51 |
- |
437.54 |
- |
A comparison between the embodied carbon emissions required for the modular and RC construction methods is shown in Figure 5.
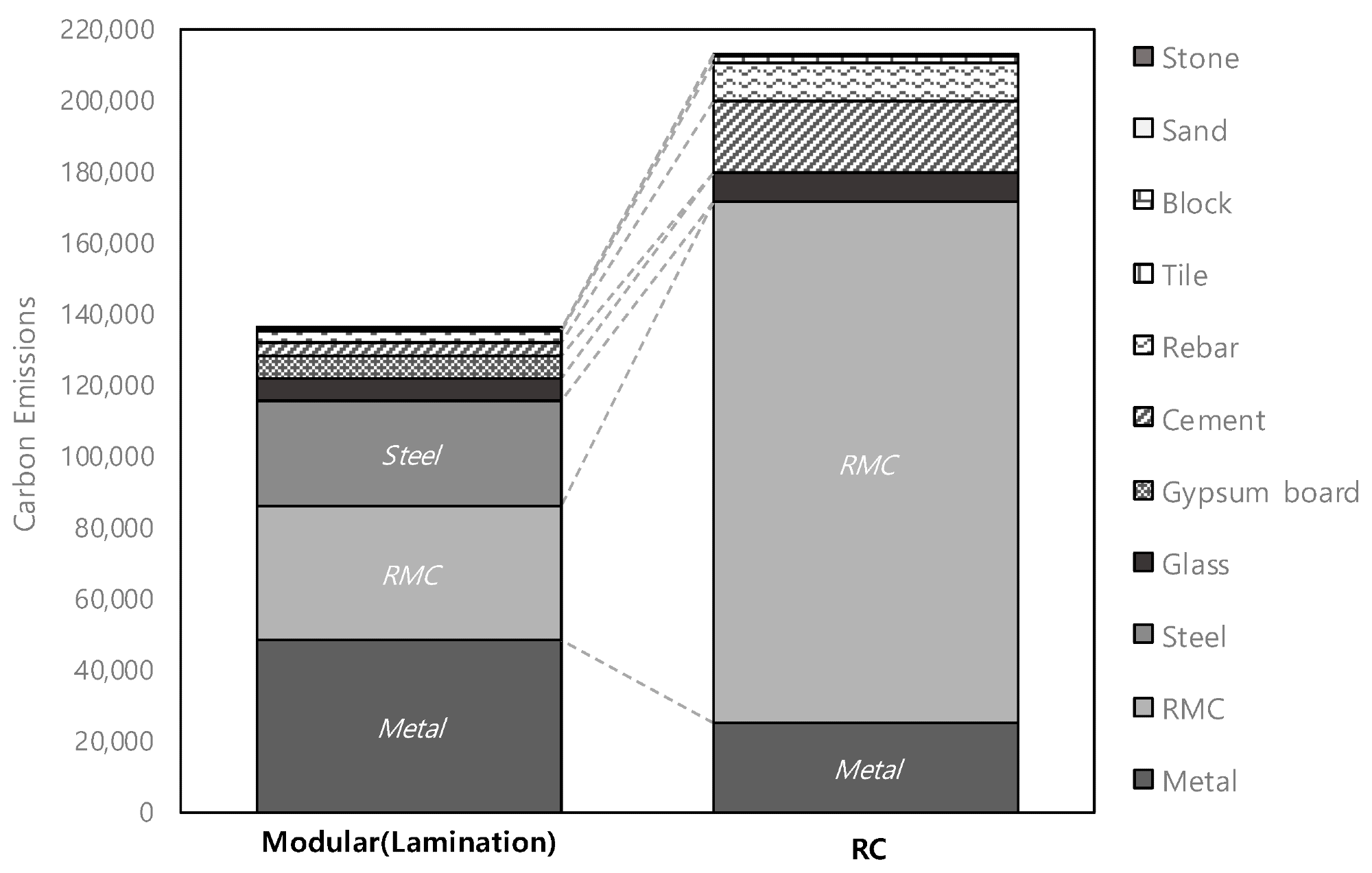
Figure 5. Comparison of the modular and RC building embodied carbon emissions. Image Credit: Jang, et al., 2022
Based on a detailed report of the national modular public housing demonstration complex project, the direct construction costs of the RC construction method and the modular construction method were examined.
The findings of the direct construction costs of both methods are shown in Figure 6 and Table 6.
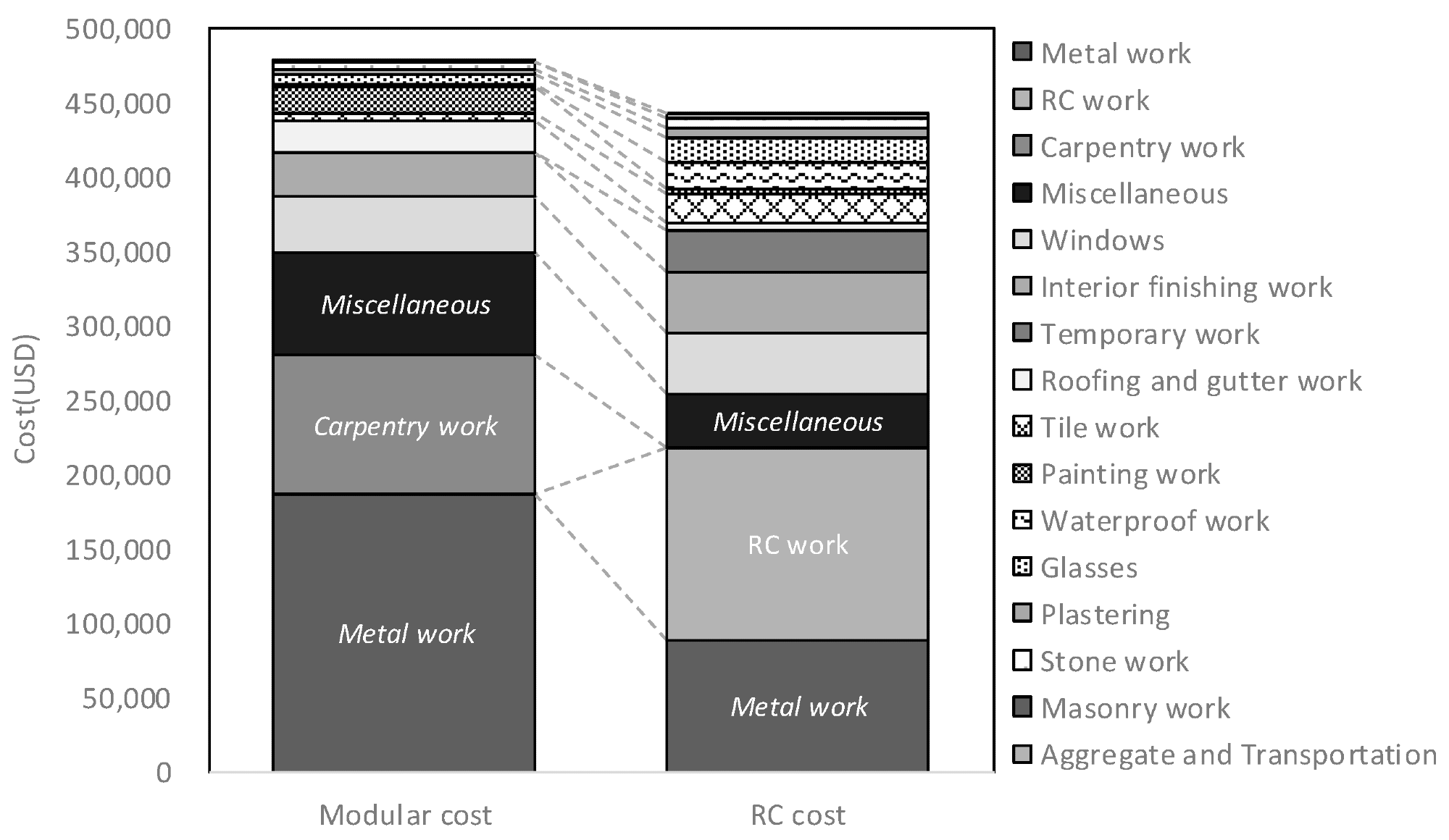
Figure 6. Comparison of modular construction and RC construction costs. Image Credit: Jang, et al., 2022
Table 6. Direct construction costs for the modular and RC construction methods. Source: Jang, et al., 2022
Activities |
Modular (B-Wing) |
Reinforced Concrete |
Cost
(USD) * |
Proportion
(%) |
Cost
(USD) * |
Proportion
(%) |
Metal work |
186,202 |
39.01 |
88,020 |
19.93 |
Reinforced concrete work |
- |
- |
129,968 |
29.43 |
Carpentry work |
92,976 |
19.48 |
- |
- |
Miscellaneous |
70,145 |
14.70 |
35,484 |
8.04 |
Windows |
37,123 |
7.78 |
41,083 |
9.30 |
Interior finishing work |
29,875 |
6.26 |
40,366 |
9.14 |
Temporary work |
- |
- |
28,764 |
6.51 |
Roofing and gutter work |
20,668 |
4.33 |
4700 |
1.06 |
Tile work |
5750 |
1.20 |
19,398 |
4.39 |
Painting work |
18,005 |
3.77 |
3124 |
0.71 |
Waterproof work |
704 |
0.15 |
17,793 |
4.03 |
Glass |
7487 |
1.57 |
16,831 |
3.81 |
Plastering |
3124 |
0.65 |
6908 |
1.56 |
Stone work |
5118 |
1.07 |
5969 |
1.35 |
Masonry work |
155 |
0.03 |
546 |
0.12 |
Aggregate and Transportation |
- |
- |
2626 |
0.59 |
Total |
477,332 |
100 |
441,580 |
100 |
Per m2 |
982.57 |
- |
908.97 |
- |
* 1 USD = 1240 KRW.
When the overall direct construction cost of RC and modular construction methods are compared, the modular construction costs were 8.1% higher approximately. Nevertheless, considering the possibility of reusing the individual modules, material cost reduction is possible due to mass module production and enhanced work productivity. Thus, a reduction in the production unit cost over the module’s entire lifecycle is possible.
Hence, the construction industry is using more of the latest modular construction methods to enhance productivity.
The embodied carbon emissions and direct construction costs of the RC and modular methods were examined and compared. This assessment considered both environmental and economic factors, thereby validating the modular method’s efficiency and value for money.
The study results prove that modular construction can reduce embodied carbon emissions in the material production phase, when compared to the RC structure, despite an expensive direct construction cost.
Similar to the results of equivalent previous studies, this result is also considered in the same context as the finding that the RC structures’ environmental influence is greater when compared with the environmental impact of modular (steel) structures and RC structures (Table 7).
In addition to the already identified benefits of modular construction, it is expected that the modular construction application will also provide environmental benefits.
Table 7. Characteristics summary table of RC method and modular method. Source: Jang, et al., 2022
Classification |
Previous Studies |
This Study |
Reinforced
Concrete (RC) |
Modular |
Modular |
Environment |
By using concrete, which is a carbon-intensive material, as the main material, a
lot of environmental impact occurs. |
By minimizing the use of ready-mixed concrete and using materials with a high reuse rate, it is possible to reduce carbon emissions by up to 88% [58]. |
The modular construction method reduced embodied carbon emissions in the material production stage by approximately 36%. |
Cost |
In general, the initial cost is less compared to the modular method. |
By mass production and using regular factory workers, it is possible to reduce the cost of materials by about 10% [2,68]. |
The modular construction method was approximately 8.1% higher than the reinforced concrete construction method. |
Time |
It is highly influenced by external factors such as weather, so
the possibility of air delay is high. |
By simultaneously manufacturing factories and on-site work, it is possible to shorten the construction period by 50% compared to the existing method [76]. |
- |
Quality |
Influence by external factors is high, and quality problems occur frequently. |
Manufactured by standardized working methods in the factory to ensure quality. |
- |
Safety |
The on-site work period is long and the safety accident rate is high due to the heavy equipment. |
It is possible to reduce the occurrence of safety accidents by minimizing field work. |
- |
Conclusion
The study analyzed and compared the produced embodied carbon emissions and direct construction costs that occurred during the material production stage of a residential building. The results are compared for the modular and RC construction methods, enabling the calculation of the cost involved in these two methods and the determination of characteristics through an assessment of their environmental cost and performance.
As a result, the modular construction method decreased embodied carbon emissions in the material production phase by around 36%, when compared with the conventional RC method. This is directly related to the amount of ready-mix concrete used, along with its high embodied carbon emissions.
The comparison revealed that the modular method was more expensive. Nevertheless, due to the benefits of the modular construction method, which offers high-recycling rates and ease of repair, the cost results were not considered, requiring a further cost review to obtain a full-lifecycle perspective. The study dealt only with the initial phase of material production and excluded the reuse possibility, so the results show only a partial scenario.
Journal Reference:
Jang, H., Ahn, Y., Roh, S. (2022) Comparison of the Embodied Carbon Emissions and Direct Construction Costs for Modular and Conventional Residential Buildings in South Korea. Buildings, 12(1), p51; Available Online: https://www.mdpi.com/2075-5309/12/1/51/htm
References and Further Reading
- Tam, V. W., et al. (2015) Best practice of prefabrication implementation in the Hong Kong public and private sectors. Journal of Cleaner Production, 109, pp.216–231. doi.org/10.1016/j.jclepro.2014.09.045.
- Kim, K-T & Lee, Y-H (2011) Economic Feasibility Study on the Unit Modular Fabrication Method According to the Life Cycle Costing Methodology. Journal of Architectural Institute of Korea, 27, pp.207–214.
- Jaillon, L C & Poon, C S (2009) The evolution of prefabricated residential building systems in Hong Kong: A review of the public and the private sector. Automation in Construction, 18, pp.239–248. doi.org/10.1016/j.autcon.2008.09.002.
- Xu, X & Zhao, Y (2010) Some Economic Facts of the Prefabricated Housing; Industry Report; Rutgers Business School: Newark, NJ, USA.
- Mao, C., et al. (2016) Cost analysis for sustainable off-site construction based on a multiple-case study in China. Habitat International, 57, pp.215–222. doi.org/10.1016/j.habitatint.2016.08.002.
- Kamali, M., et al. (2018) Life cycle sustainability performance assessment framework for residential modular buildings: Aggregated sustainability indices. Building and Environment, 138, pp.21–41. doi.org/10.1016/j.buildenv.2018.04.019.
- Li, Z., et al. (2014) Measuring the impact of prefabrication on construction waste reduction: An empirical study in China. Resources, Conservation and Recycling, 91, pp.27–39. doi.org/10.1016/j.resconrec.2014.07.013.
- Baldwin, A., et al. (2009) Designing out waste in high-rise residential buildings: Analysis of precasting methods and traditional construction. Renewable Energy, 34, pp.2067–2073. doi.org/10.1016/j.renene.2009.02.008.
- Li, Z., et al. (2014) Critical review of the research on the management of prefabricated construction. Habitat International, 43, pp.240–249. doi.org/10.1016/j.habitatint.2014.04.001.
- Nahmens, I & Ikuma, L H (2012) Effects of Lean Construction on Sustainability of Modular Homebuilding. Journal of Architectural Engineering, 18, pp.155–163. doi.org/10.1061/(ASCE)AE.1943-5568.0000054.
- Kamali, M & Hewage, K (2016) Life cycle performance of modular buildings: A critical review. Renewable and Sustainable Energy Reviews, 62, pp.1171–1183. doi.org/10.1016/j.rser.2016.05.031.
- Ahn, Y H & Kim, K -T (2014) Sustainability in modular design and construction: A case study of ‘The Stack’. International Journal of Sustainable Building Technology and Urban Development, 5, pp.250–259. doi.org/10.1080/2093761X.2014.985758.
- Ganiron, T U & Almarwae, M (2014) Prefabricated Technology in a Modular House. International Journal of Advanced Science and Technology, 73, pp.51–74. doi.org/10.14257/ijast.2014.73.04.
- Pervez, H., et al. (2021) A quantitative assessment of greenhouse gas (GHG) emissions from conventional and modular construction: A case of developing country. Journal of Cleaner Production, 294, p.126210. doi.org/10.1016/j.jclepro.2021.126210.
- Atmaca, N (2016) Life-cycle assessment of post-disaster temporary housing. Building Research & Information, 45, pp.524–538. doi.org/10.1080/09613218.2015.1127116.
- Giriunas, K., et al. (2012) Evaluation, modeling, and analysis of shipping container building structures. Engineering Structures, 43, pp.48–57. doi.org/10.1016/j.engstruct.2012.05.001.
- Masson-Delmotte, V., et al. (2018) Global warming of 1.5 C. An IPCC Special Report on the Impacts of Global Warming of 2018, 1. Available at: https://www.ipcc.ch/sr15/.
- Han, Y., et al. (2017) Market Equilibrium Supply Chain Model for Supporting Self-Manufacturing or Outsourcing Decisions in Prefabricated Construction. Sustainability, 9, p.2069. doi.org/10.3390/su9112069.
- Mao, C., et al. (2013) Comparative study of greenhouse gas emissions between off-site prefabrication and conventional construction methods: Two case studies of residential projects. Energy and Buildings, 66, pp.165–176. doi.org/10.1016/j.enbuild.2013.07.033.
- Cao, X., et al. (2015) A comparative study of environmental performance between prefabricated and traditional residential buildings in China. Journal of Cleaner Production, 109, pp.131–143. doi.org/10.1016/j.jclepro.2015.04.120.
- Thormark, C (2000) Including recycling potential in energy use into the life-cycle of buildings. Building Research & Information, 28, pp.176–183. doi.org/10.1080/096132100368948.
- Kamali, M & Hewage, K (2017) Development of performance criteria for sustainability evaluation of modular versus conventional construction methods. Journal of Cleaner Production, 142, pp.3592–3606. doi.org/10.1016/j.jclepro.2016.10.108.
- Tumminia, G., et al. (2018) Life cycle energy performances and environmental impacts of a prefabricated building module. Renewable and Sustainable Energy Reviews, 92, pp.272–283. doi.org/10.1016/j.rser.2018.04.059.
- Wang, S & Sinha, R (2021) Life Cycle Assessment of Different Prefabricated Rates for Building Construction. Buildings, 11, p.552. doi.org/10.3390/buildings11110552.
- Velamati, S (2012) Feasibility, Benefits and Challenges of Modular Construction in High Rise Development in the United States: A Developer’s Perspective. Master’s Thesis, Massachusetts Institute of Technology, Cambridge, MA, USA.
- Generalova, E., et al. (2016) Modular Buildings in Modern Construction. Procedia Engineering, 153, pp.167–172. doi.org/10.1016/j.proeng.2016.08.098.
- Lim, S.-H (2016) A Current State of Apartment Construction Technology Development with the Application of Modular Technology. Review of Architecture Building Science, 60, pp.16–21.
- Schoenborn, J M (2012) A Case Study Approach to Identifying the Constraints and Barriers to Design Innovation for Modular Construction. Master’s Thesis, Virginia Polytechnic Institute and State University, Blacksburg, VA, USA, 27 April.
- Lacey, A., et al. (2019) Review of bolted inter-module connections in modular steel buildings. Journal of Building Engineering, 23, pp.207–219. doi.org/10.1016/j.jobe.2019.01.035.
- Lacey, A.W., et al. (2018) Structural response of modular buildings–an overview. Journal of Building Engineering, 16, pp.45–56. doi.org/10.1016/j.jobe.2017.12.008.
- Srisangeerthanan, S., et al. (2020) Review of performance requirements for inter-module connections in multi-story modular buildings. Journal of Building Engineering, 28, p.101087. doi.org/10.1016/j.jobe.2019.101087.
- Aye, L., et al. (2012) Life cycle greenhouse gas emissions and energy analysis of prefabricated reusable building modules. Energy and Buildings, 47, pp.159–168 doi.org/10.1016/j.enbuild.2011.11.049.
- Thirunavukkarasu, K., et al. (2021) Sustainable Performance of a Modular Building System Made of Built-Up Cold-Formed Steel Beams. Buildings, 11, p.460. doi.org/10.3390/buildings11100460.
- Chiang, Y. H., et al. (2006) Prefabrication and barriers to entry—A case study of public housing and institutional buildings in Hong Kong. Habitat International, 30, pp.482–499. doi.org/10.1016/j.habitatint.2004.12.004.
- Xu, Z., et al. (2020) Comparative analysis of modular construction practices in mainland China, Hong Kong and Singapore. Journal of Cleaner Production, 245, p.118861. doi.org/10.1016/j.jclepro.2019.118861.
- Faludi, J., et al. (2012) Using life cycle assessment methods to guide architectural decision-making for sustainable prefabricated modular buildings. Journal of Green Building, 7, pp.151–170. doi.org/10.3992/jgb.7.3.151.
- Lawson, R & Ogden, R (2010) Sustainability and process benefits of modular construction. In Proceedings of the TG57-Special Track 18th CIB World Building Congress, Salford, UK, 10–13 May; p.38.
- Hartley, A & Blagden, A (2007) Current Practices and Future Potential in Modern Methods of Construction; Full Final Report WAS003-001; Waste & Resources Action Programme, AMA Research LtD.: London, UK.
- Dong, Y. H., et al. (2015) Comparing carbon emissions of precast and cast-in-situ construction methods–A case study of high-rise private building. Construction and Building Materials, 99, pp.39–53. doi.org/10.1016/j.conbuildmat.2015.08.145.
- Kamali, M., et al. (2019) Conventional versus modular construction methods: A comparative cradle-to-gate LCA for residential buildings. Energy and Buildings, 204, p.109479. doi.org/10.1016/j.enbuild.2019.109479.
- Hong, J & Shen, G Q (2016) Life-cycle energy analysis of prefabricated building components: An input–output-based hybrid model. Journal of Cleaner Production, 112, pp.2198–2207. doi.org/10.1016/j.jclepro.2015.10.030.
- Blanquet du Chayla, C., et al. (2021) A Method to Qualify the Impacts of Certifications for Prefabricated Constructions. Buildings, 11, p.331. doi.org/10.3390/buildings11080331.
- Park, J.-Y., et al. (2014) A Comparative Analysis on Life Cycle CO Emission between a Modular Housing and a R.C. Apartment Housing. Plant Design, 30, pp.35–43. doi.org/10.5659/JAIK_PD.2014.30.5.035.
- Kim, D (2008) Preliminary Life Cycle Analysis of Modular and Conventional Housing in Benton Harbor; University of Michigan: Ann Arbor, MI, USA.
- Balasbaneh, A. T., et al. (2019) Sustainable materials selection based on flood damage assessment for a building using LCA and LCC. Journal of Cleaner Production, 222, pp.844–855. doi.org/10.1016/j.jclepro.2019.03.005.
- Bovea, M & Vidal, R (2004) Increasing product value by integrating environmental impact, costs and customer valuation. Resources, Conservation and Recycling, 41, pp.133–145. doi.org/10.1016/j.resconrec.2003.09.004.
- Xie, H.-B., et al. (2018) Life-time reliability based optimization of bridge maintenance strategy considering LCA and LCC. Journal of Cleaner Production, 176, pp.36–45. doi.org/10.1016/j.jclepro.2017.12.123.
- Shi, J., et al. (2019) An integrated environment and cost assessment method based on LCA and LCC for mechanical product manufacturing. The International Journal of Life Cycle Assessment, 24, pp.64–77. doi.org/10.1007/s11367-018-1497-x.
- Pons, O & Wadel, G (2011) Environmental impacts of prefabricated school buildings in Catalonia. Habitat International, 35, pp.553–563. https://doi.org/10.1016/j.habitatint.2011.03.005.
- ISO, I (2006) ISO-14040 Environmental Management–Life Cycle Assessment–Principles and Framework, International Organization for Standardization: Geneva, Switzerland.
- Lee, J.-M., et al. (2014) Study on Recognition and Satisfaction of Modular Housing through the Post Occupancy Evaluation. Journal of the Korean housing association, 25, pp.63–71. doi.org/10.6107/JKHA.2014.25.5.063.
- Soust-Verdaguer, B., et al. (2016) Simplification in life cycle assessment of single-family houses: A review of recent developments. Building and Environment, 103, pp.215–227. doi.org/10.1016/j.buildenv.2016.04.014.
- Ben-Alon, L., et al. (2021) Life cycle assessment (LCA) of natural vs conventional building assemblies. Renewable and Sustainable Energy Reviews, 144, p.110951. doi.org/10.1016/j.rser.2021.110951.
- Li, D., et al. (2016) Development of an automated estimator of life-cycle carbon emissions for residential buildings: A case study in Nanjing, China. Habitat International, 57, pp.154–163. doi.org/10.1016/j.habitatint.2016.07.003.
- Ahmed, I. M., et al. (2018) Life cycle assessment (LCA) and cost (LCC) studies of lightweight composite flooring systems. Journal of Building Engineering, 20, pp.624–633. doi.org/10.1016/j.jobe.2018.09.013.
- Bribian, I. Z., et al. (2009) Life cycle assessment in buildings: State-of-the-art and simplified LCA methodology as a complement for building certification. Building and Environment, 44, pp.2510–2520. doi.org/10.1016/j.buildenv.2009.05.001.
- Pan, W., et al. (2018) Rethinking system boundaries of the life cycle carbon emissions of buildings. Renewable and Sustainable Energy Reviews, 90, pp.379–390. doi.org/10.1016/j.rser.2018.03.057.
- Minunno, R., et al. (2021) Investigating the embodied energy and carbon of buildings: A systematic literature review and meta-analysis of life cycle assessments. Renewable and Sustainable Energy Reviews, 143, p.110935. doi.org/10.1016/j.rser.2021.110935.
- Asdrubali, F., et al. (2020) An Evaluation of the Environmental Payback Times and Economic Convenience in an Energy Requalification of a School. Buildings, 11, p.12. doi.org/10.3390/buildings11010012.
- Chau, C.-K., et al. (2015) A review on Life Cycle Assessment, Life Cycle Energy Assessment and Life Cycle Carbon Emissions Assessment on buildings. Applied Energy, 143, pp. 395–413. doi.org/10.1016/j.apenergy.2015.01.023.
- Islam, H., et al. (2015) Life cycle assessment and life cycle cost implication of residential buildings—A review. Renewable and Sustainable Energy Reviews, 42, pp.129–140. doi.org/10.1016/j.rser.2014.10.006.
- Salehian, S., et al. (2020) Assessment on Embodied Energy of Non-Load Bearing Walls for Office Buildings. Buildings, 10, p.79. doi.org/10.3390/buildings10040079.
- Tae, S., et al. (2011) The development of apartment house life cycle CO2 simple assessment system using standard apartment houses of South Korea. Renewable and Sustainable Energy Reviews, 15, pp.1454–1467. doi.org/10.1016/j.rser.2010.09.053.
- Venkatraj, V & Dixit, M (2021) Life cycle embodied energy analysis of higher education buildings: A comparison between different LCI methodologies. Renewable and Sustainable Energy Reviews, 144, p.110957. doi.org/10.1016/j.rser.2021.110957.
- Mohammad, M., et al. (2020) A Comparative Life Cycle Assessment of Four Construction Method Scenarios. Buildings, 10, p.245. doi.org/10.3390/buildings10120245.
- Satola, D., et al. (2020) Life Cycle GHG Emissions of Residential Buildings in Humid Subtropical and Tropical Climates: Systematic Review and Analysis. Buildings, 11, p.6. doi.org/10.3390/buildings11010006.
- Korea Life Cycle Inventory Database; Korea Environmental Industry and Technology Institute (KEITI) (2004) Seoul, Korea.
- Shin, H. K., et al. (2019) Economic Feasibility Study on the Modular Apartment Housing According to the Life Cycle Costing Methodology: A Case Study on the Modular Apartment Housing in Cheonan. Korea Facility Management Association, 14, pp.15–24.
- Ristimäki, M., et al. (2013) Combining life cycle costing and life cycle assessment for an analysis of a new residential district energy system design. Energy, 63, pp.168–179. doi.org/10.1016/j.energy.2013.10.030.
- Dhaif, M., et al. (2021) A Life Cycle Cost Analysis of Structural Insulated Panels for Residential Buildings in a Hot and Arid Climate. Buildings, 11, p.255. doi.org/10.3390/buildings11060255.
- D’Incognito, M., et al. (2015) Actors and barriers to the adoption of LCC and LCA techniques in the built environment. Built Environment Project and Asset Management, 5, pp.202–216. doi.org/10.1108/BEPAM-12-2013-0068.
- Guoguo, L (2009) Integration of LCA and LCC for Decision Making in Sustainable Building Industry; Chalmers University of Technology: Gothenburg, Sweden.
- Hromada, E., et al. (2021) Residential Construction with a Focus on Evaluation of the Life Cycle of Buildings. Buildings, 11, p.524. doi.org/10.3390/buildings11110524.
- Petrović, B., et al. (2021) Life Cycle Cost Analysis of a Single-Family House in Sweden. Buildings, 11, p.215. doi.org/10.3390/buildings11050215.
- Oladazimi, A., et al. (2020) Comparative Life Cycle Assessment of Steel and Concrete Construction Frames: A Case Study of Two Residential Buildings in Iran. Buildings, 10, p.54. doi.org/10.3390/buildings10030054.
- Quale, J., et al. (2012) Construction Matters: Comparing Environmental Impacts of Building Modular and Conventional Homes in the United States. Journal of Industrial Ecology, 16, pp.243–253. doi.org/10.1111/j.1530-9290.2011.00424.x.
- Loizou, L., et al. (2021) Quantifying Advantages of Modular Construction: Waste Generation. Buildings, 11, p.622. doi.org/10.3390/buildings11120622.