Jun 22 2022
The use of recycled materials and seawater sea-sand concrete (SSC) in building has increased in recent decades due to a scarcity of raw materials. Because seawater and sea sand are plentiful marine resources, they have social, economic, and environmental advantages. This is discussed in research in the journal Buildings.
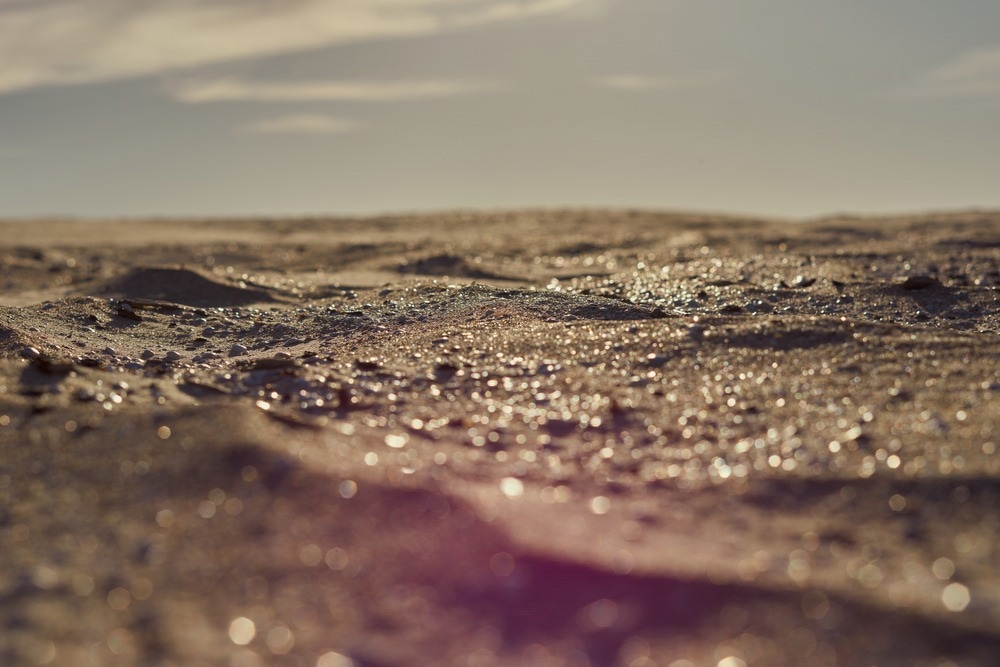
Study: Mechanical Properties of Seawater Sea-Sand Concrete Exposed to Daily Temperature Variations. Image Credit: nadia_if/Shutterstock.com
However, one major difficulty with using SSC in buildings is that the chloride ions in seawater and sea sand may quickly destroy standard steel reinforcements in concrete. Scholars recently recommended that SSC be strengthened with fiber-reinforced polymer (FRP) components. FRP-SSC structures do not require any particular treatment because it is resistant to chloride corrosion.
As a result, SSC structures can be used in marine constructions, coastal infrastructures, bridges, and pavements when corrosion-resistant reinforcing materials are used. Corrosive substances, freezes, and thaws, alkali-aggregate interactions, cyclic loads, increased temperatures, temperature cycles, or a combination of these elements are all likely to have an impact on the durability of concrete buildings.
One of the most prevalent forms of environmental stress is the daily temperature. Although the natural temperature may not appear to have an impact on concrete’s durability, a high number of temperature cycles can cause it to lose its mechanical qualities. Curling and expansion/contraction of concrete slabs are caused by temperature fluctuations, which is a major element impacting pavement behavior.
Internal concrete stress induced by daily temperature variations can develop cracks, lowering the structural longevity of concrete structures. Because daily temperature variations have a significant impact on the durability of concrete, it is critical to close the knowledge gap indicated above in order to encourage the use of SSC buildings in the future.
Mechanical characteristics such as compressive strength, Young’s modulus, Poisson’s ratio, toughness, ultimate strain, and the stress-strain relationship were measured using axial compression tests on SSC cylindrical specimens in this article. The impact of daily temperature variations on the mechanical characteristics of SSC (e.g., thermal cycle times and temperature amplitude) was addressed.
The microstructures of SSC subjected to temperature fluctuations were studied using scanning electron microscopy (SEM). Finally, theoretical methods for predicting the stress-strain relationship after temperature cycles were presented.
FRP bars were successfully employed to strengthen concrete bridge decks that came into touch with de-icing salt in a demonstration project run by an EU–US initiative called SEACON, shown in Figure 1.
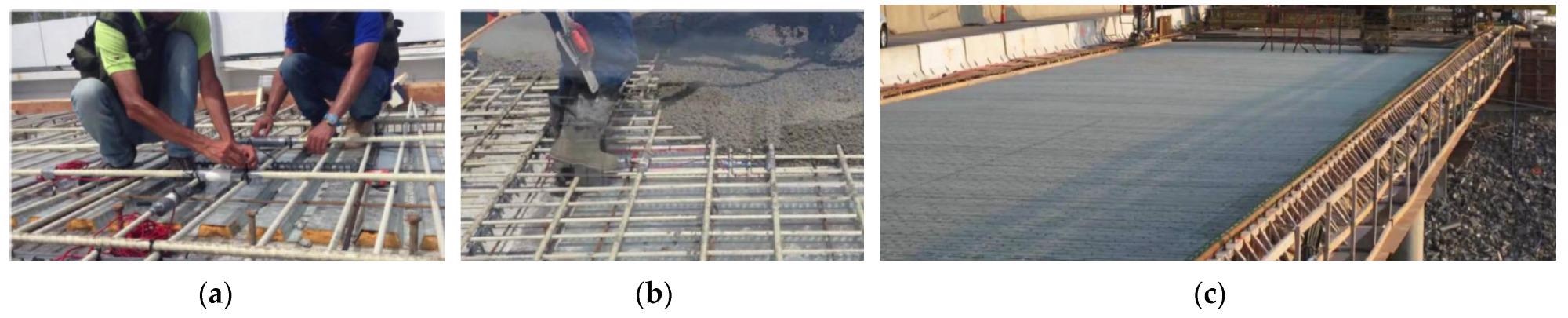
Figure 1. Demonstration project for FRP-SSC bridge decks: (a) FRP mesh; (b) concrete casting; (c) bridge deck. Image Credit: Qiao, et al., 2022
Methodology
Three classes of seawater sea-sand concrete (SSC) were studied in this investigation, with the combinations stated in Table 1.
Table 1. Mix proportions of SSC. Source: Qiao, et al., 2022
Concrete |
Cement: Seawater: Sea Sand: Gravels: SP (by Weight) |
C40 |
1:0.55:2.101:3.151:0.008 |
C70 |
1:0.38:1.613:3.276:0.01 |
C90 |
1:0.295:1.054:2.24:0.01 |
Temperature cycles made by an environmental chamber were used to imitate daily temperature fluctuations (Figure 2).
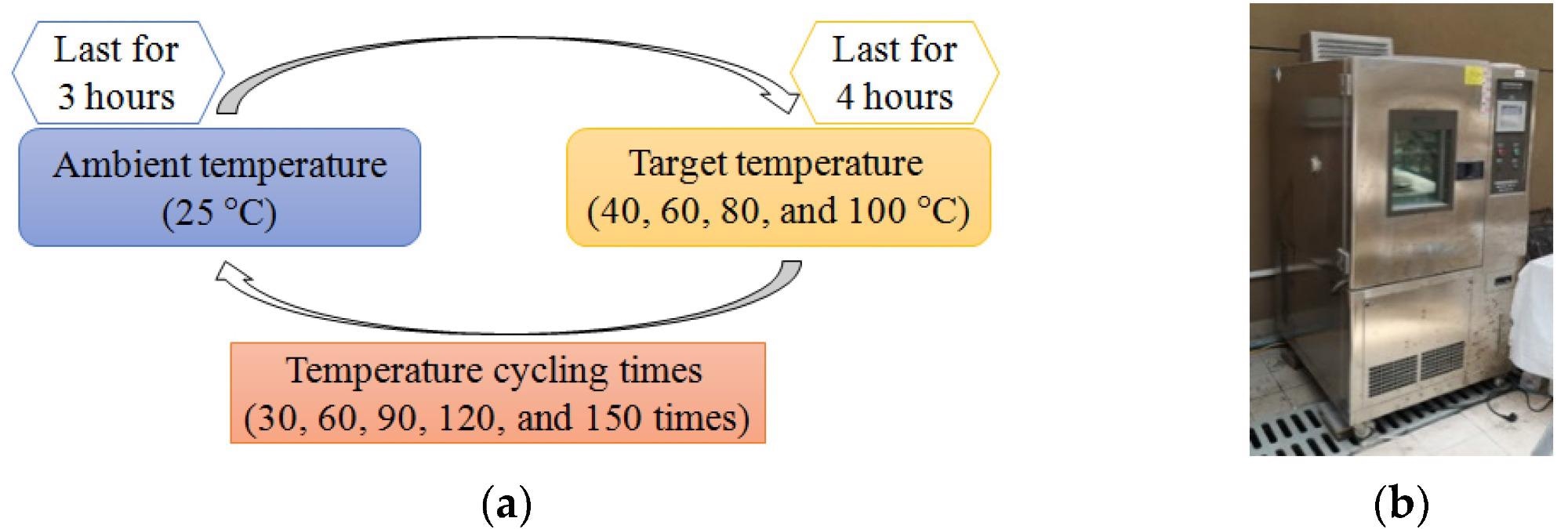
Figure 2. Simulation of daily temperature variations: (a) cyclic temperature regime; (b) programmable environmental chamber. Image Credit: Qiao, et al., 2022
According to previous research, the mean annual temperatures and humidity in Guangzhou’s coastline city are 24 °C and 70%, respectively (Figure 3).
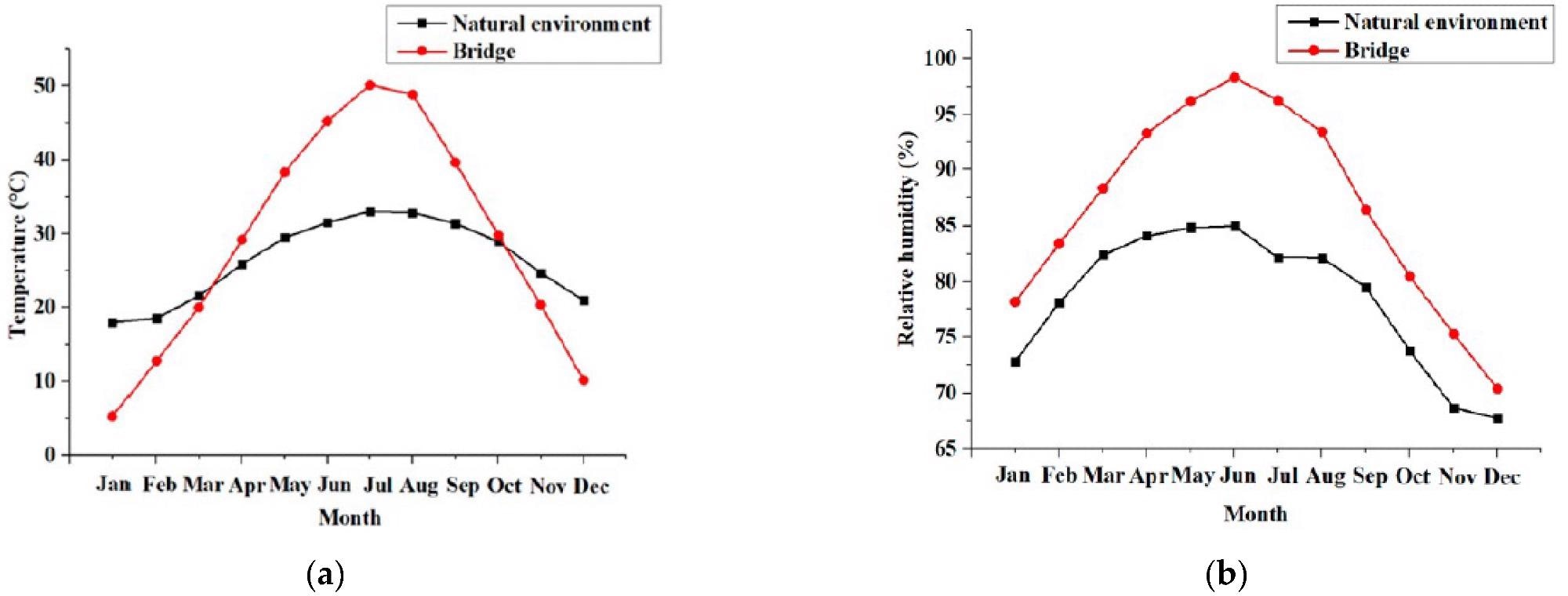
Figure 3. Recorded data for Guangzhou, China: (a) temperature; (b) relative humidity. Image Credit: Qiao, et al., 2022
SSC cylinders were subjected to compression tests using a 4000 kN testing equipment in accordance with ASTM C39/C39M, with a loading rate of 0.18 mm/min (Figure 4).
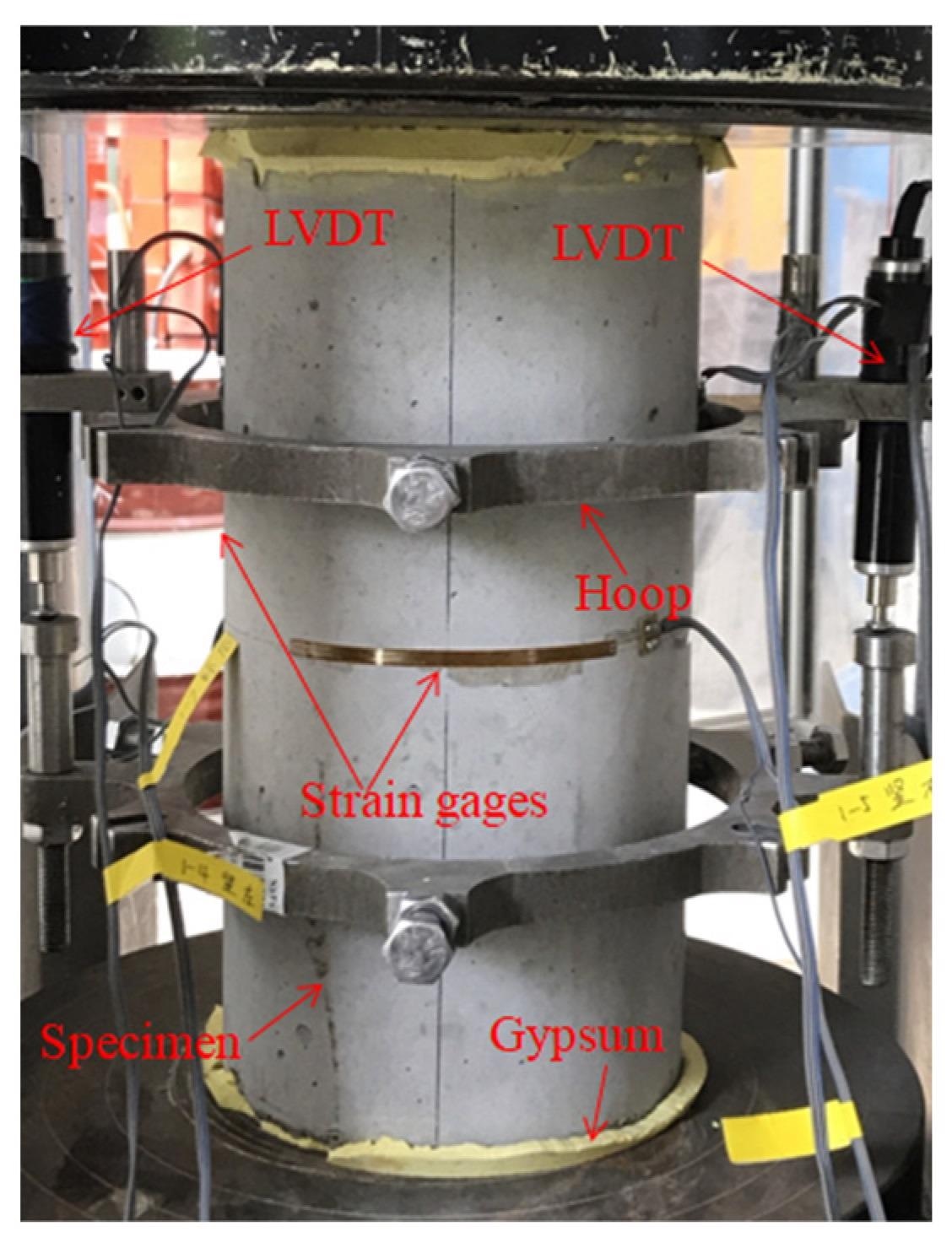
Figure 4. Experimental setup for SSC compressive test. Image Credit: Qiao, et al., 2022
Results
Figure 5 depicts the failure mechanisms of SSC cylinders under axial compression. When concrete strength increases, the frequency of fractures decreases, and failures become more brittle, as seen in Figure 5(a–c) for unconditioned cylinders.
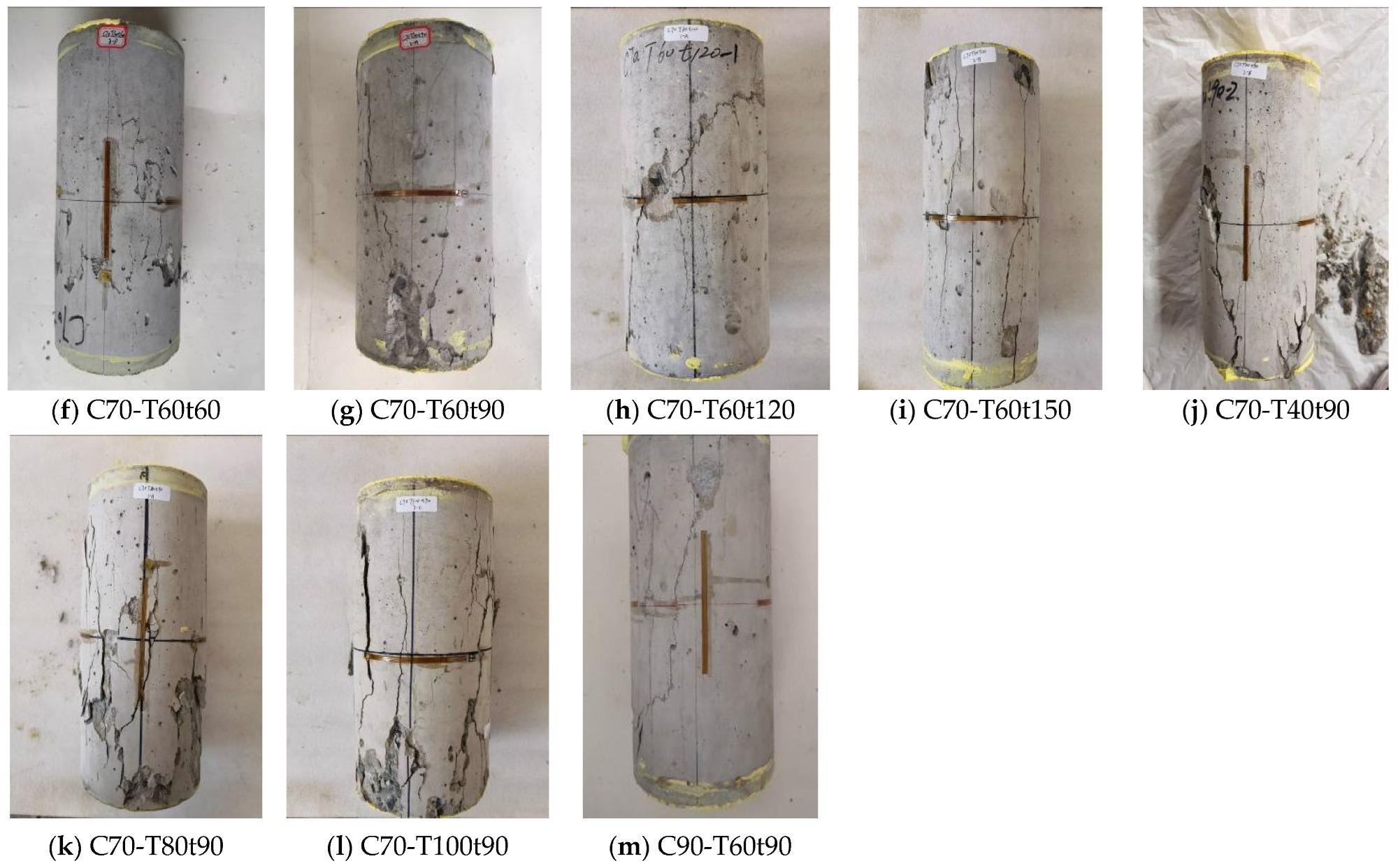
Figure 5. Failure modes of SSC cylinders. Image Credit: Qiao, et al., 2022
Figure 6 shows the stress-strain curves of the SSC cylinders, where the stress is directly proportional to the applied force divided by the cross-sectional area, as well as the strain is calculated using the LVDT values.
Figure 6a shows that the post-peak curves of unconditioned concrete with a smaller strength are less steep, implying reduced brittleness, which is consistent with the failure mode data. The effects of the target temperature on the stress-strain relationship of SSC are shown in Figure 6b, and the effects of thermal cycling durations on the stress-strain relationship of SSC are shown in Figure 6c.
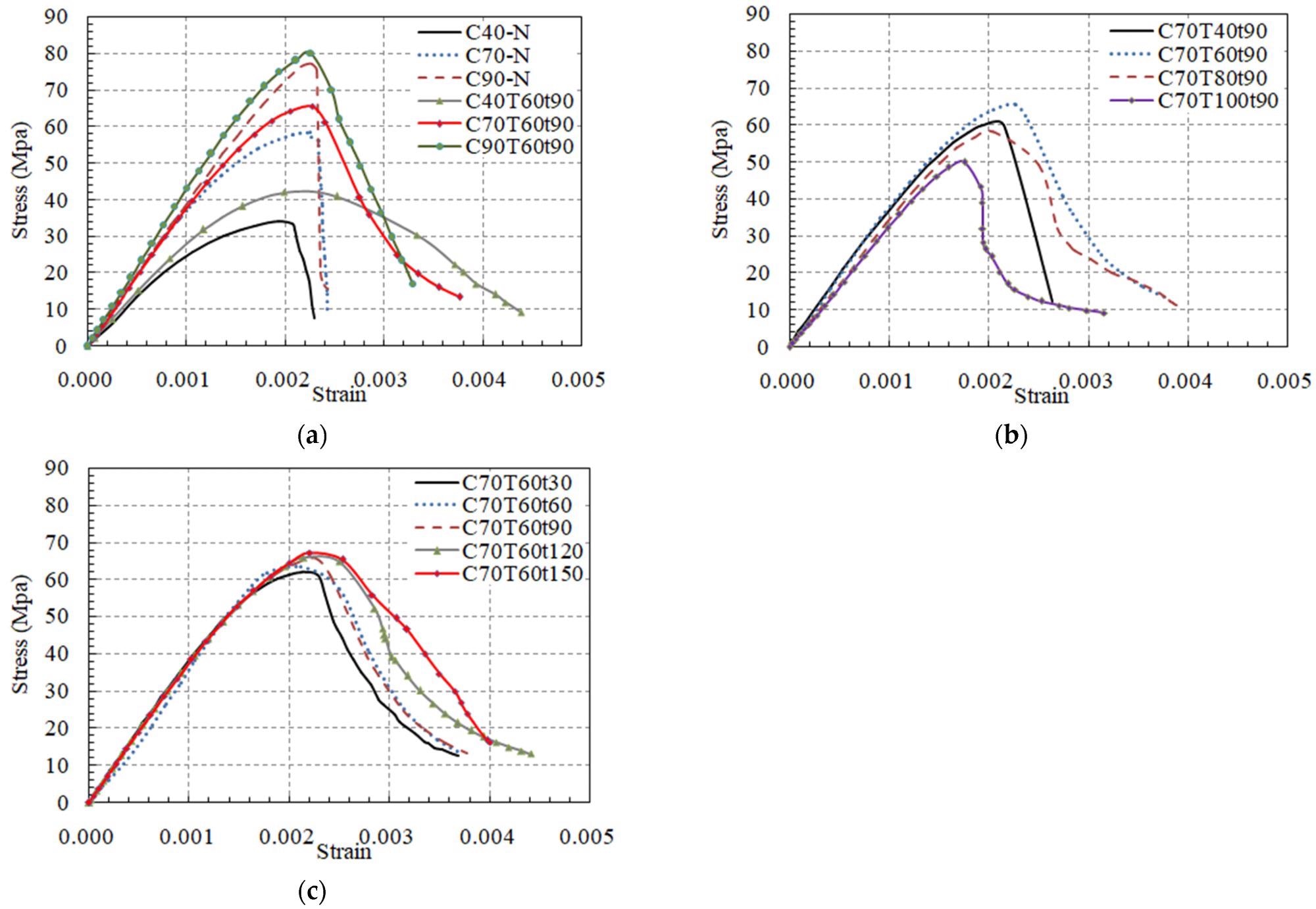
Figure 6. Stress-strain curves of SSC: (a) unconditioned and conditioned specimens; (b) specimens with various target temperatures; (c) specimens with various cycling times. Image Credit: Qiao, et al., 2022
Table 2 lists a cylindrical compressive strength (fc) of unconditioned SSC and SSC exposed to heat cycles, and Figure 7 displays the compressive strength comparison.
Table 2. SSC specimens and key experimental results. Source: Qiao, et al., 2022
Specimen |
f'c
(MPa) |
Ec
(GPa) |
U |
εc
(µε) |
Toughness
(MPa) |
C40-N |
34.1 |
26.9 |
0.19 |
1940 |
513 |
C70-N |
58.4 |
37.0 |
0.23 |
2250 |
905 |
C90-N |
77.2 |
41.5 |
0.20 |
2340 |
977 |
C40T60t90 |
42.1 |
29.8 |
0.17 |
1990 |
1025 |
C70T60t90 |
65.7 |
39.5 |
0.20 |
2200 |
1394 |
C90T60t90 |
80.1 |
42.4 |
0.20 |
2380 |
1447 |
C70T60t30 |
61.9 |
39.7 |
0.21 |
2120 |
1256 |
C70T60t60 |
63.3 |
40.0 |
0.24 |
2200 |
1297 |
C70T60t120 |
66.0 |
38.4 |
0.19 |
2140 |
1647 |
C70T60t150 |
67.3 |
37.9 |
0.18 |
2200 |
1700 |
C70T40t90 |
59.9 |
37.3 |
0.22 |
1860 |
923 |
C70T80t90 |
58.3 |
34.3 |
0.18 |
2040 |
1248 |
C70T100t90 |
50.0 |
32.3 |
0.18 |
1760 |
744 |
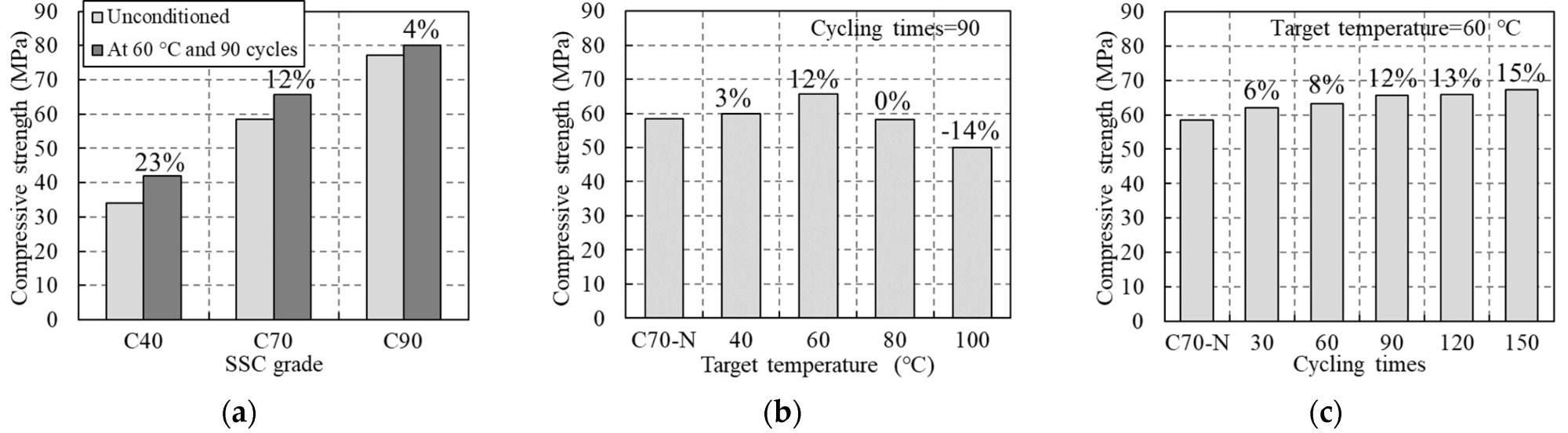
Figure 7. Compressive strength of SSC: (a) effects of SSC grade; (b) effects of target temperature; (c) effects of cycling times. Image Credit: Qiao, et al., 2022
The compressive strength of SSC with grades of C40, C70, and C90 rises by 23%, 12%, and 4% following thermal cycles (target temperature = 60 °C and cycling durations = 90). (Figure 7a). The impacts of the target temperature on the compressive strength of SSC (cycle times = 90) are shown in Figure 7b. At 40 °C and 60 °C, SSC shows an increase in strength. When cycle periods are increased to 60 °C, the compressive strength steadily rises, as illustrated in Figure 7c.
The effects of temperature cycles on concrete Young’s modulus are insignificant, as illustrated in Figure 8, and are purely dependent on compressive strength.
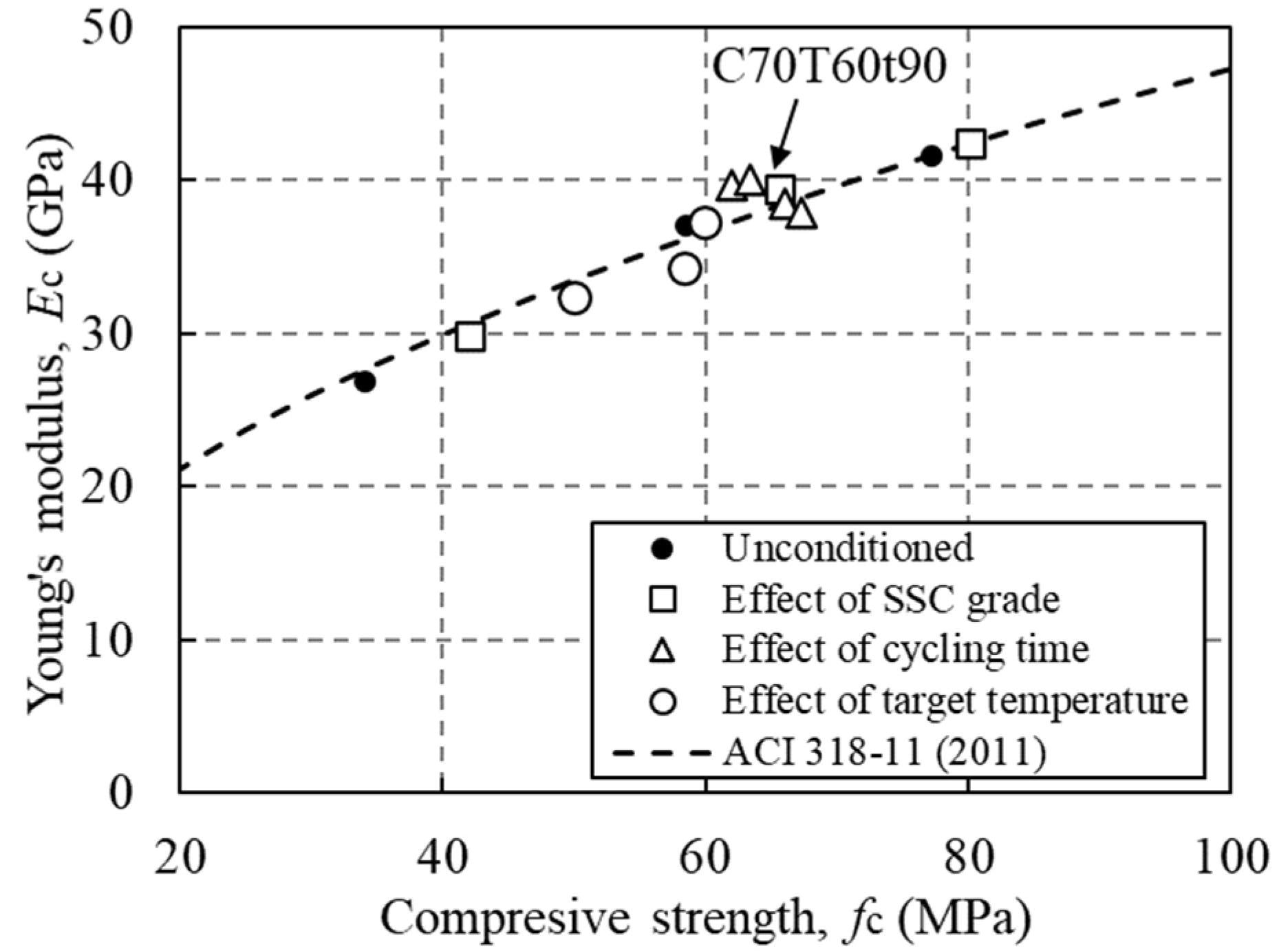
Figure 8. Young’s modulus of SSC. Image Credit: Qiao, et al., 2022
Figure 9 depicts the associations between the εc and fc of tested specimens.
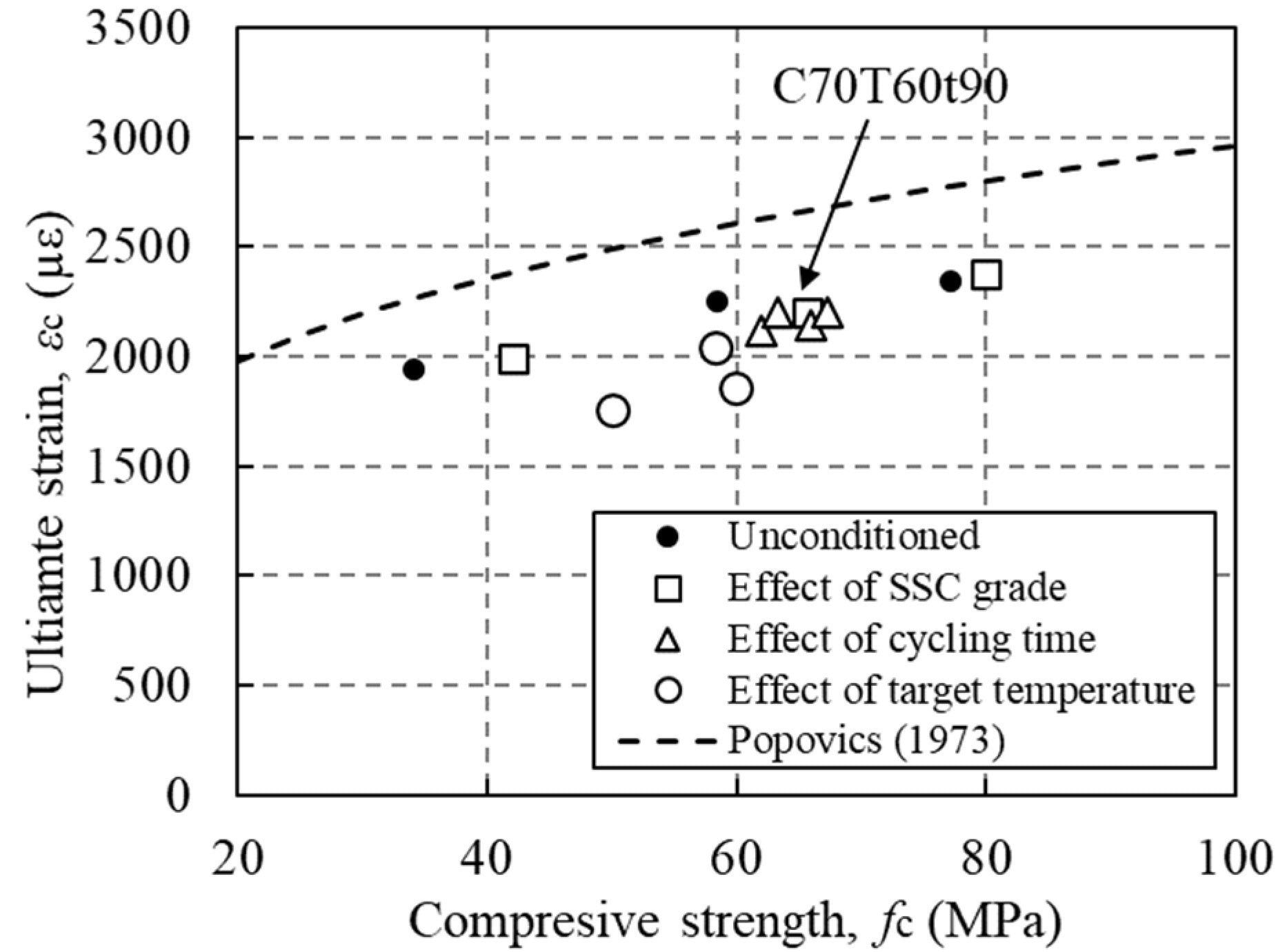
Figure 9. Ultimate strain of SSC. Image Credit: Qiao, et al., 2022
Figure 10 shows that independent of compressive strength, a Poisson’s ratio of SSC varies from 0.17 to 0.24.
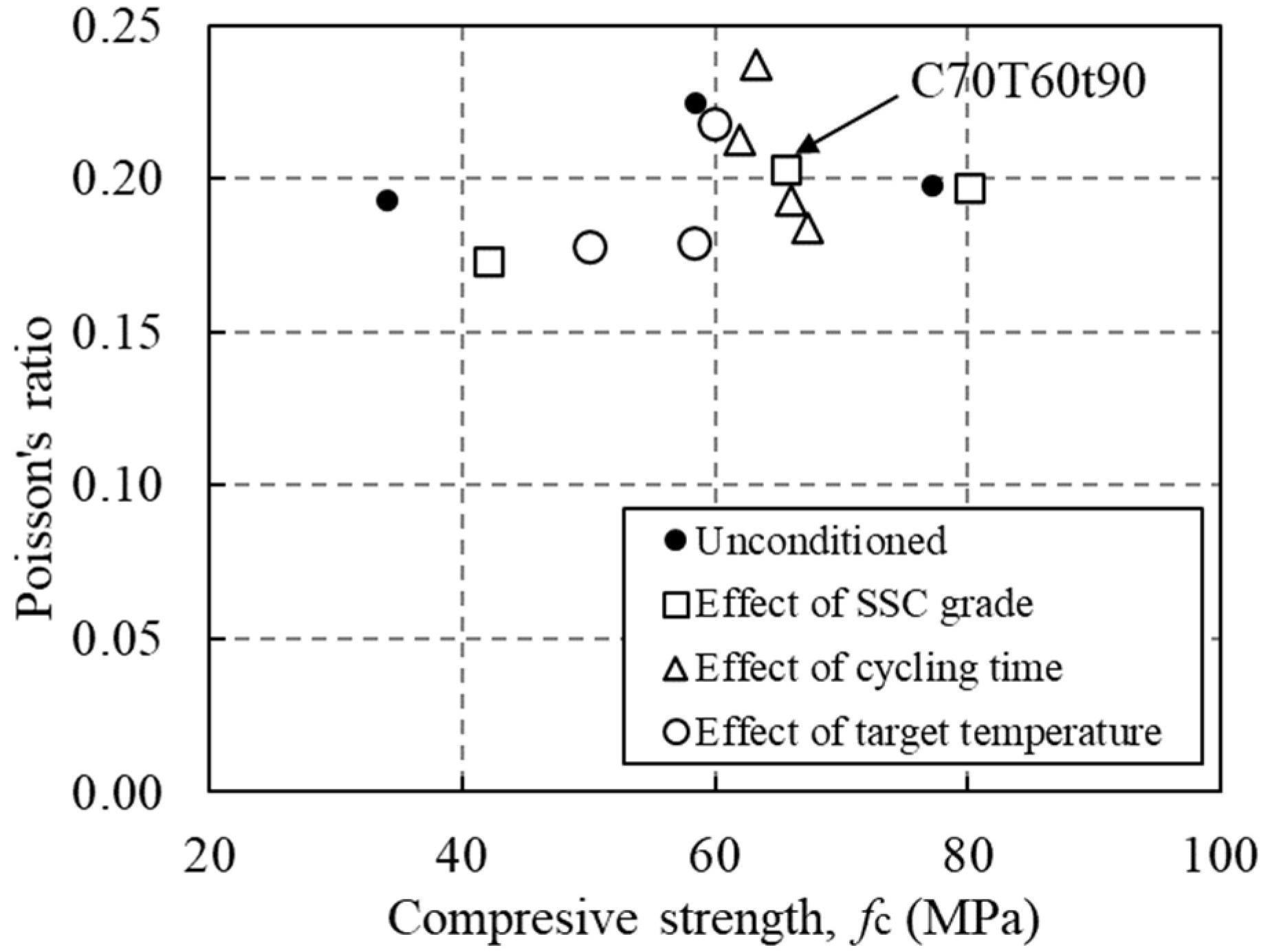
Figure 10. Relationship between Poisson’s ratio and compressive strength. Image Credit: Qiao, et al., 2022
Thermal cycling, as seen in Figure 11, has the potential to modify the Poisson’s ratio of SSC to some amount. Poisson’s ratio is normally decreasing with the rise in goal temperature and cycling times.

Figure 11. Poisson’s ratio of SSC: (a) effects of SSC grade; (b) effects of target temperature; (c) effects of cycling times. Image Credit: Qiao, et al., 2022
Figure 12 depicts the link between SSC toughness and compressive strength, whereas Figure 13 depicts the toughness impacts of concrete grade, target temperature, and cycling durations.
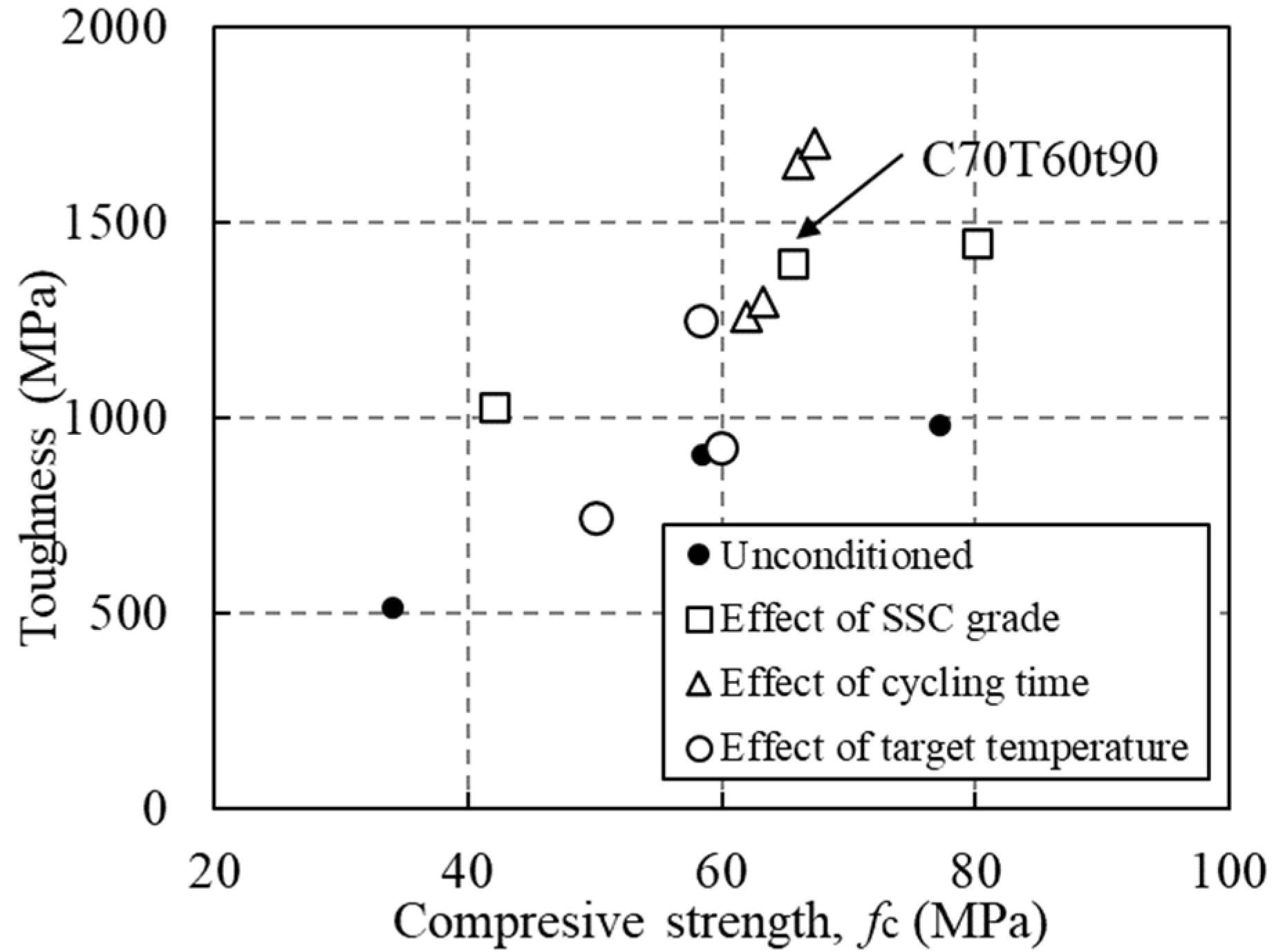
Figure 12. Relationship between toughness and compressive strength. Image Credit: Qiao, et al., 2022
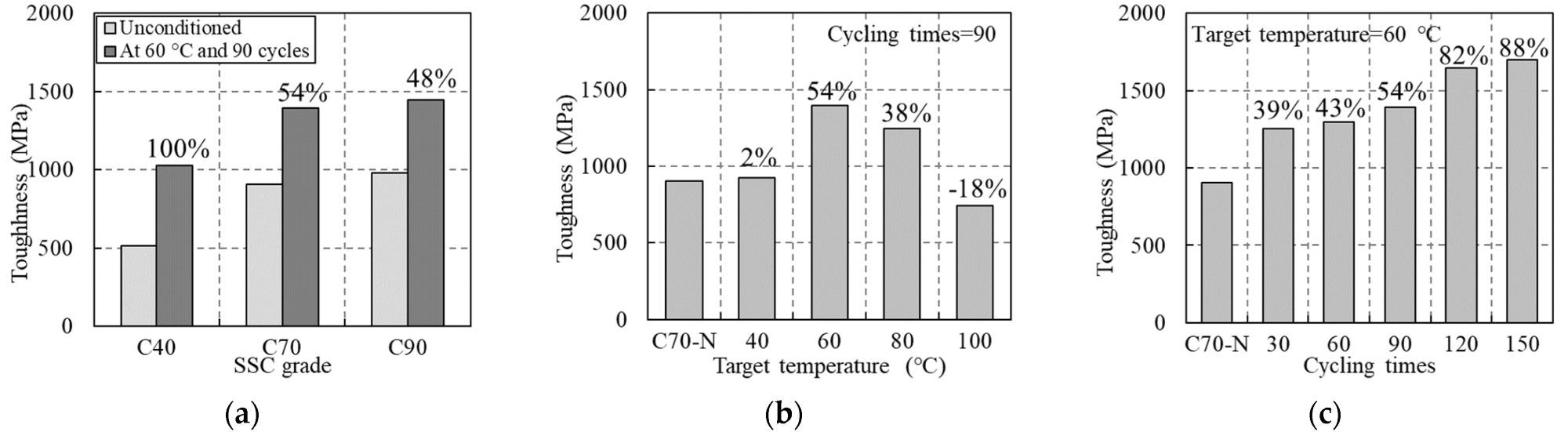
Figure 13. Toughness of SSC: (a) effects of SSC grade; (b) effects of target temperature; (c) effects of cycling times. Image Credit: Qiao, et al., 2022
In Figure 14, SEM pictures of SSC are shown.
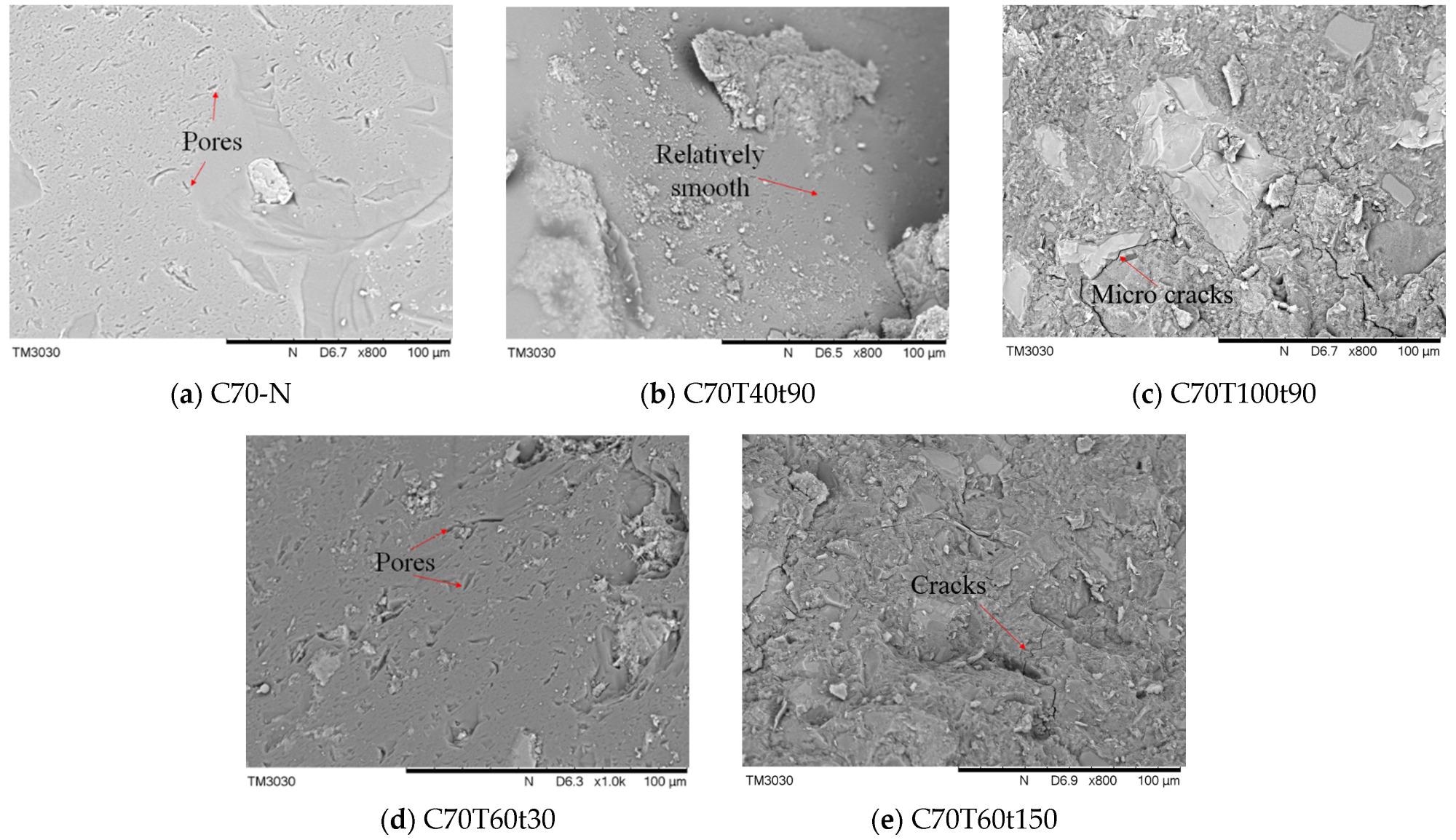
Figure 14. SEM images of SSC. Image Credit: Qiao, et al., 2022
Figure 15 shows a comparison of the experimental and predicted compressive strength and ultimate strain data.
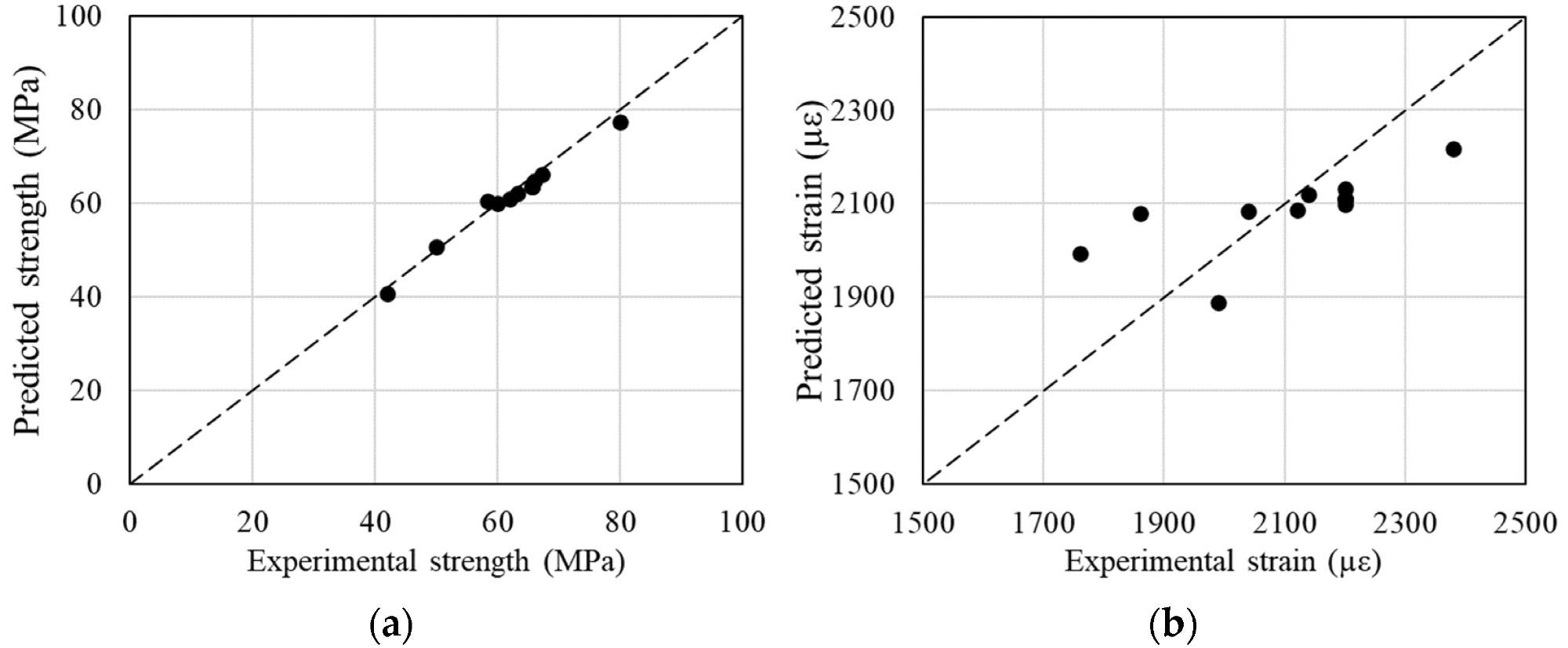
Figure 15. Comparison between the experimental and predicted results: (a) compressive strength; (b) ultimate strain. Image Credit: Qiao, et al., 2022
Figure 16 shows a comparison of the anticipated and experimental stress-strain curves of SSC specimens.
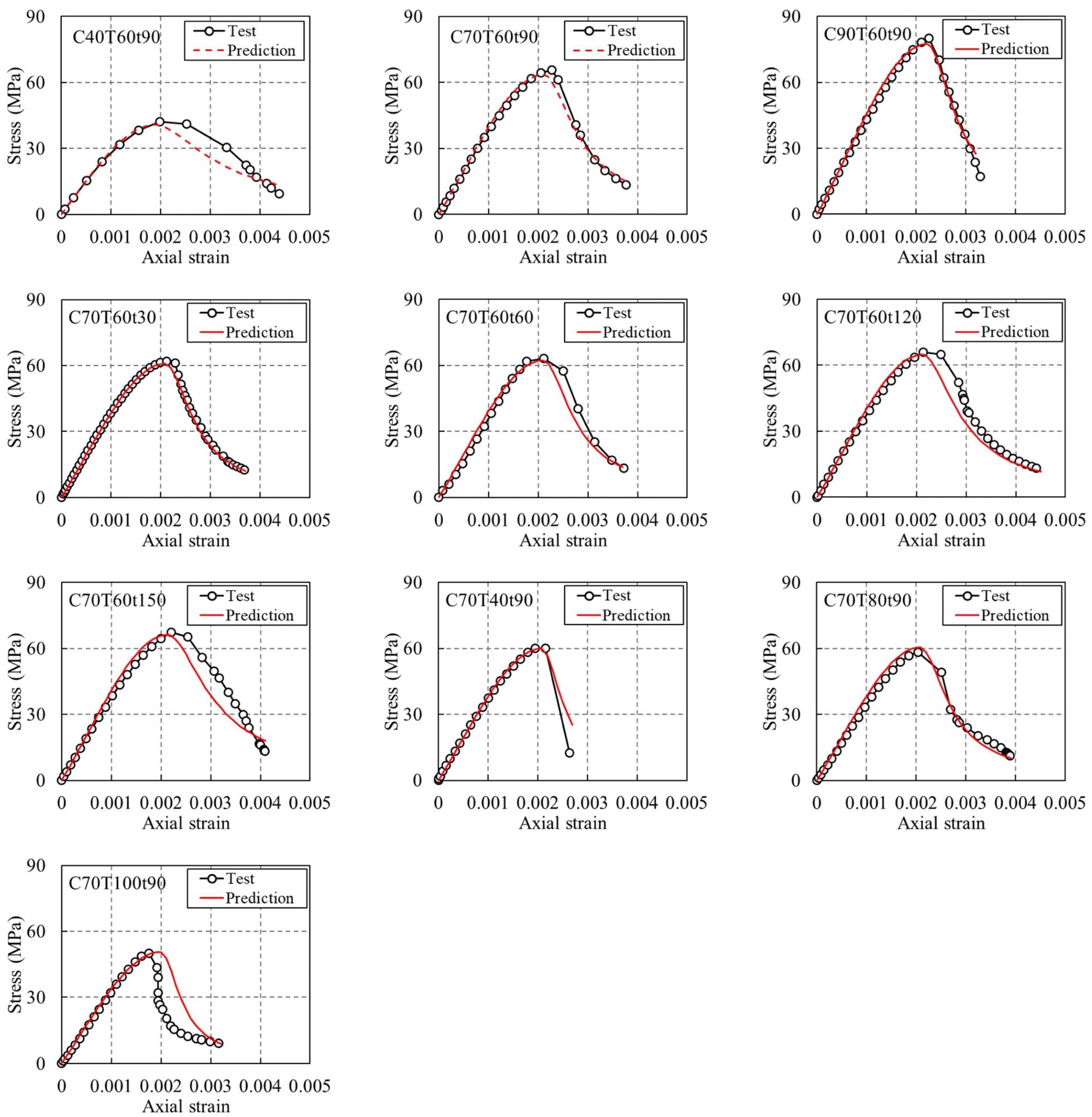
Figure 16. Prediction of stress-strain relationship of SSC subjected to thermal cycles. Image Credit: Qiao, et al., 2022
Conclusion
The impact of temperature fluctuations (e.g., target temperature and thermal cycle durations) on the mechanical characteristics of seawater sea-sand concrete (SSC) is the focus of this research. The following are the findings reached.
The compressive strength of SSC improves at 60 °C as the number of thermal cycle periods increases owing to increased cement hydration. The compressive strength of SSC is lowered if the goal temperature is 100 °C since microcracks occur in the SSC interfacial transition zone due to the unmatched expansion and contraction of aggregates and paste.
SSC’s Young’s modulus and ultimate strain are functions of compressive strength, and thermal cycling has only a small impact. With longer cycle periods, Poisson’s ratio of SSC reduces marginally.
The toughness of SSC exposed to thermal cycling is higher than that of unconditioned SSC since the strength increases and the post-peak branches of the stress-strain curve are flat.
The stress-strain relationship of SSC during temperature fluctuations is predicted using a theoretical model, and the prediction closely reflects the actual data. It is worth noting that the proposed formulae are based on samples with temperatures ranging from 25–100 °C and cycle periods ranging from 30 to 150 times.
Journal Reference:
Qiao, S., Xiong, Z., Li, Y., Ye, Z., He, S., Li, L. and Zeng, Y. (2022) Mechanical Properties of Seawater Sea-Sand Concrete Exposed to Daily Temperature Variations. Buildings, 12(5), p.517. Available Online: https://www.mdpi.com/2075-5309/12/5/517/htm
References and Further Reading
- Fang, Z., et al. (2022) Static behavior of grouped stud shear connectors in steel-precast UHPC composite structures containing thin full-depth slabs. Engineering Structures, 252, p. 113484. doi.org/10.1016/j.engstruct.2021.113484.
- Sun, C., et al. (2021) Compound utilization of construction and industrial waste as cementitious recycled powder in mortar. Resources, Conservation & Recycling, 170, p. 105561. doi.org/10.1016/j.resconrec.2021.105561.
- Sun, C., et al. (2021) Study on Aggregate Interlock Behavior of Pre-Cracked Recycled Aggregate Concrete without Stirrups. Journal of Building Engineering, 39, p. 102257. doi.org/10.1016/j.jobe.2021.102257.
- Liu, X., et al. (2022) Enhanced early hydration and mechanical properties of cement-based materials with recycled concrete powder modified by nano-silica. Journal of Building Engineering, 50, p. 104175. doi.org/10.1016/j.jobe.2022.104175.
- Li, T., et al. (2020) Preparation of sea water sea sand high performance concrete (SHPC) and serving performance study in marine environment. Construction and Building Materials, 254, p. 119114. doi.org/10.1016/j.conbuildmat.2020.119114.
- Tjaronge, M. W., et al. (2014) Compressive strength and hydration process of self compacting concrete (SCC) mixed with sea water, marine sand and portland composite cement. Advanced Materials Research, 935, pp. 242–246. doi.org/10.4028/www.scientific.net/AMR.935.242.
- Younis, A., et al. (2018) Fresh and hardened properties of seawater-mixed concrete. Construction and Building Materials, 190, pp. 276–286. doi.org/10.1016/j.conbuildmat.2018.09.126.
- Xiao, J., et al. (2017) Use of sea-sand and seawater in concrete construction: Current status and future opportunities. Construction and Building Materials, 155, pp. 1101–1111. doi.org/10.1016/j.conbuildmat.2017.08.130.
- Liu, W., et al. (2016) Carbonation of concrete made with dredged marine sand and its effect on chloride binding. Construction and Building Materials, 120, pp. 1–9. doi.org/10.1016/j.conbuildmat.2016.05.011.
- Xiao, J., et al. (2022) Influence of sulfuric acid corrosion on concrete stress-strain relationship under uniaxial compression. Measurement, 187, p. 110318. doi.org/10.1016/j.measurement.2021.110318.
- Mohammed, T. U. T., et al. (2004) Performance of seawater-mixed concrete in the tidal environment. Cement and Concrete Research, 34, pp. 593–601. doi.org/10.1016/j.cemconres.2003.09.020.
- Xie, J., et al. (2022) Effects of immersion in water, alkaline solution and seawater on the shear performance of BFRP bars embedded in seawater sea-sand concrete. Journal of Composites for Construction, 26, p. 04021071. doi.org/10.1061/(ASCE)CC.1943-5614.0001184.
- Xiong, Z., et al. (2022) Axial performance of seawater sea-sand concrete columns reinforced with basalt fibre-reinforced polymer bars under concentric compressive load. Journal of Building Engineering, 47, p. 103828. doi.org/10.1016/j.jobe.2021.103828.
- Li, Y. L., et al. (2016) Experimental study on seawater and sea sand concrete filled GFRP and stainless steel tubular stub columns. Thin-walled structures, 106, pp. 390–406. doi.org/10.1016/j.tws.2016.05.014.
- Dong, Z., et al. (2018) Durability test on the flexural performance of seawater sea-sand concrete beams completely reinforced with FRP bars. Construction and Building Materials, 192, pp. 671–682. doi.org/10.1016/j.conbuildmat.2018.10.166.
- Nishida, T., et al. (2015) Some considerations for applicability of seawater as mixing water in concrete. The Journal of Materials in Civil Engineering, 7, p. B4014004. doi.org/10.1061/(ASCE)MT.1943-5533.0001006.
- El-Salakawy, E., et al. (2005) Field investigation on the first bridge deck slab reinforced with glass FRP bars constructed in Canada. Journal of Composites for Construction, 9, pp. 470–479. doi.org/10.1061/(ASCE)1090-0268(2005)9:6(470).
- Limeira, J., et al. (2010) Dredged marine sand in concrete: An experimental section of a harbor pavement. Construction and Building Materials, 24, pp. 863–870. doi.org/10.1016/j.conbuildmat.2009.12.011.
- Mehta, P K & Monteiro, P J M (2006) Concrete: Microstructure, Properties, and Materials, 3rd ed.; McGraw-Hill, New York, NY, USA.
- Wegian, F M (2010) Effect of seawater for mixing and curing on structural concrete. The IES Journal Part A: Civil & Structural Engineering, 3, pp. 235–243. doi.org/10.1080/19373260.2010.521048.
- Xiong, Z., et al. (2022) Fatigue bond behaviour between basalt fibre-reinforced polymer bars and seawater sea-sand concrete. Ocean & Coastal Management, 218, p. 106038. doi.org/10.1016/j.ocecoaman.2022.106038.
- Tang, Y., et al. (2021) Fracture behavior of a sustainable material: Recycled concrete with waste crumb rubber subjected to elevated temperatures. Journal of Cleaner Production, 318, p. 128553. doi.org/10.1016/j.jclepro.2021.128553.
- Silva, M. A. G., et al. (2013) Influence of temperature cycles on bond between glass fiber-reinforced polymer and concrete. ACI Structural Journal, 110, pp. 977–987.
- Wang, Z., et al. (2018) Effect of sustained load and seawater and sea sand concrete environment on durability of basalt-and glass-fibre reinforced polymer (B/GFRP) bars. Corrosion Science, 138, pp. 200–218. doi.org/10.1016/j.corsci.2018.04.002.
- Liang, R Y & Niu, Y Z (1998) Temperature and curling stress in concrete pavements: Analytical solutions. Journal, Transportation Engineering, 124, pp. 91–100. doi.org/10.1061/(ASCE)0733-947X(1998)124:1(91).
- Nama, B. H., et al. (2014) Effect of daily temperature variations on the continuous deflection profiles of airfield jointed concrete pavements. Construction and Building Materials, 73, pp. 261–270. doi.org/10.1016/j.conbuildmat.2014.09.073.
- Liu, H., et al. (2016) Effect of temperature variation on modal frequency of reinforced concrete slab and beam in cold regions. Shock and Vibration, 2016, p. 4792786. doi.org/10.1155/2016/4792786.
- An, M., et al. (2020) Effect of thermal cycling on the properties of high-performance concrete: Microstructure and mechanism. Construction and Building Materials, 243, p. 118310. doi.org/10.1016/j.conbuildmat.2020.118310.
- Liu, F., et al. (2018) Static and impact behaviour of recycled aggregate concrete under daily temperature variations. Journal of Cleaner Production, 191, pp. 283–296. doi.org/10.1016/j.jclepro.2018.04.237.
- ASTM D1141-98 (2013) Standard Practice for the Preparation of Substitute Ocean Water. American Society for Testing and Materials: West Conshohocken, PA, USA.
- JGJ 55-2011 (2011) Specification for Mix Proportion Design of Ordinary Concrete. Ministry of Housing and Urban-Rural Development: Beijing, China.
- Xiong, Z., et al. (2021) Bond behavior of basalt fiber reinforced polymer bars in seawater sea-sand concrete exposed to daily temperature variations. Advances in Structural Engineering. doi.org/10.1002/suco.201900106.
- Guo, X., et al. (2020) Effect of subtropical natural exposure on the bond behavior of FRP-concrete interface. Polymers, 12, p. 967. doi.org/10.3390/polym12040967.
- Ding, F. X., et al. (2011) Elasto-plastic analysis of circular concrete-filled steel tube stub columns. The Journal of Constructional Steel Research, 67, pp. 1567–1577. doi.org/10.1016/j.jcsr.2011.04.001.
- ASTM C39/C39M (2017) Standard Test Method for Compressive Strength of Cylindrical Concrete Specimens. American Society for Testing and Materials: West Conshohocken, PA, USA.
- Ferretti, E (2004) On Poisson’s ratio and volumetric strain in concrete. International Journal of Fracture, 126, pp. 49–55. doi.org/10.1023/B:FRAC.0000026587.43467.e6.
- Huang, Y. J., et al. (2018) Mechanical properties of sea sand recycled aggregate concrete under axial compression. Construction and Building Materials, 175, pp. 55–63. doi.org/10.1016/j.conbuildmat.2018.04.136.
- Li, Y. L., et al. (2018) Thermal and mechanical properties of alkali-activated slag paste, mortar and concrete utilising seawater and sea sand. Construction and Building Materials, 159, pp. 704–724. doi.org/10.1016/j.conbuildmat.2017.10.104.
- ACI 318-11 (2011) Building Code Requirements for Structural Concrete and Commentary. American Concrete Institute: Farmington Hills, MI, USA.
- Popovics, S (1973) A numerical approach to the complete stress-strain curve of concrete. Cement and Concrete Research, 3, pp. 583–599. https://doi.org/10.1016/0008-8846(73)90096-3.
- Li, L. G., et al. (2017) Effects of packing on compressive behaviour of recycled aggregate concrete. Construction and Building Materials, 157, pp. 757–777. doi.org/10.1016/j.conbuildmat.2017.09.097.
- Li, L. J., et al. (2014) Mechanical properties and constitutive equations of concrete containing low volume of tire rubber particles. Construction and Building Materials, 70, pp. 291–308. doi.org/10.1016/j.conbuildmat.2014.07.105.