Reducing carbon dioxide emissions in sectors such as the cement industry is vital to mitigate the worst predicted effects of climate change. This article will discuss new research into alternative, greener binders for the cement industry, which could help to reduce the sector’s impact on the environment.
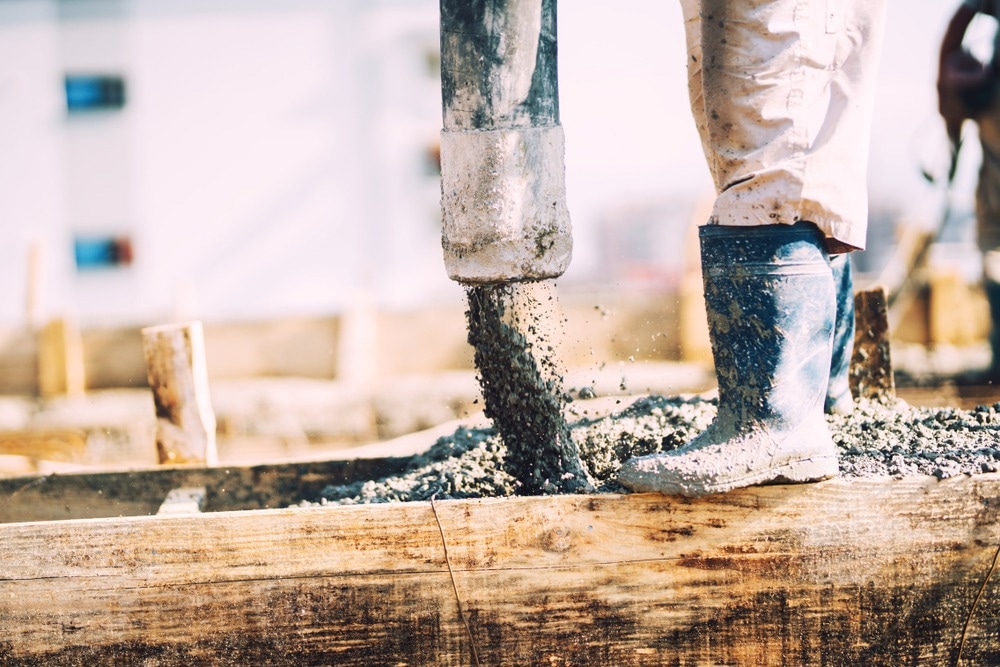
Image Credit: bogdanhoda/Shutterstock.com
The Cement Industry and Climate Change
The cement industry is one of the most polluting sectors, responsible for around 7 - 8% of total global carbon emissions yearly. To put this into perspective, the manufacture of cement alone emits more greenhouse gases than the overwhelming majority of countries (with the US and China being two exceptions).
As the world quickly urbanizes and industrializes, the need for cement will increase as new buildings and infrastructure are constructed. In order to limit global temperature rises in line with international agreements such as the Paris Agreement, the cement industry will need to rapidly and drastically reduce its CO2 emissions.
According to some estimates, the global building floor area will double over the next three decades. Due to this growing demand, annual cement production is likely to reach around five billion tons by 2030, a more than fourfold increase compared to 1990 levels.
Whilst the average global CO2 emissions per tonne of output has fallen over the past few decades by 18%, the sector’s emissions as a whole have risen significantly. Progress has been made in three key areas of cement production, though there is still room for improvement.
More efficient kilns mean that production is less energy intensive. Alternative fuels such as biomass are increasingly being utilized instead of traditional fossil fuels. Lastly, the industry is developing the use of alternative cement-like materials, such as various industrial wastes, to reduce the proportion of Portland cement clinker.
Alternative Binders: A Green Solution
Binders are an essential component of cementitious mixtures as they function as a “glue,” hardening and strengthening the final concrete product. Portland cement, the most commonly used and environmentally damaging binder, is composed of calcium silicate minerals.
The large quantities of calcium-rich materials in the raw cement mix, usually limestone, are the main source of CO2 emissions. Energy-intensive manufacturing processes release CO2 in flue gas, with process emissions related to clinker production representing around 60% of the cement industry’s total emissions.
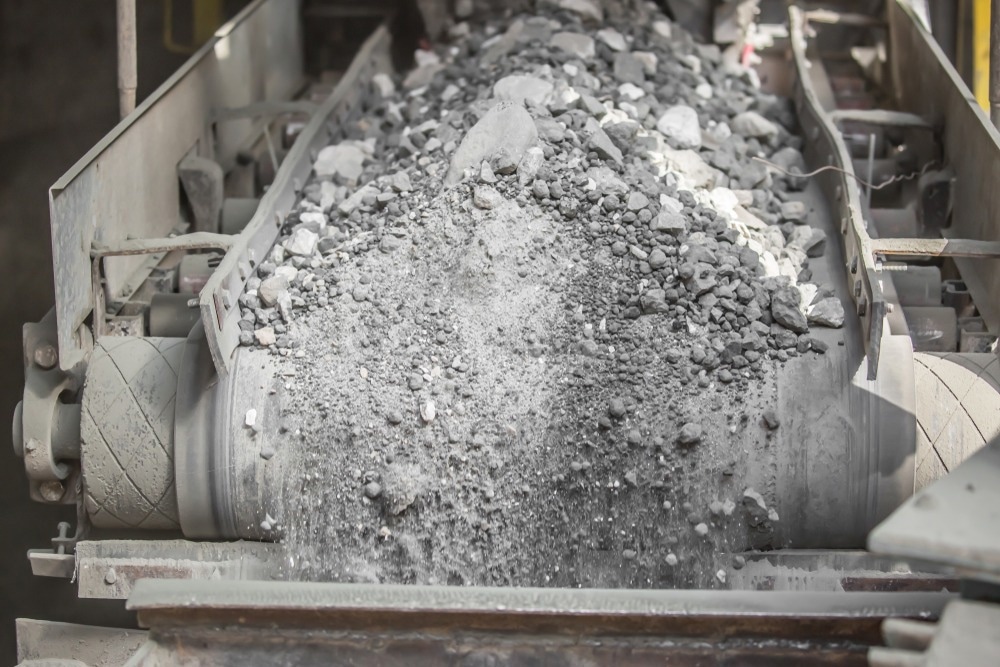
Image Credit: Vera Larina/Shutterstock.com
In recent years, alternative binders have been extensively studied by the cement industry and academic institutions. Binders such as alkali-activate binders, magnesium silicate cement, and wollastonite-based cement have all emerged as suitable candidates for green cement production.
The Research
The new study, conducted by researchers from Imperial College London’s Department of Civil and Environmental Engineering and the Swiss Federal Laboratories for Materials Science, has investigated the effect of alternative binders on magnesia silicate cement.
Aluminates and carbonates were explored in the research, with the goal of providing an in-depth understanding of their influence on magnesium silicate hydrate (M-S-H) phases. Advanced characterization methods and thermodynamic calculations were used by the paper’s authors to obtain valuable insights into material properties.
Specifically, the experimental study aimed to obtain information on the factors which govern the hydrated phases’ composition and investigate how phase assemblage, reaction degree, and compressive strength are related in the resultant cementitious mixtures.
Hydromagnesite and metakaolin, both commercial products, were used for the addition of reactive silica, carbonate, and alumina. High-purity (>99.5wt%) Al(OH)3 was heated for two hours at 600oC to prepare reactive alumina. Laser diffraction was employed to obtain the particle size distributions of the various materials.
MgO was either obtained commercially or by burning Mg(OH)2 in a laboratory furnace. Both high and low-grade silica fume were used as reactive silica sources. Paste samples with different ratios of Al/Si and Mg/Si were prepared.
Mortar mixtures, which were mixed and cured according to EN 196-1 and adapted to take into account longer curing times and smaller prism sizes, were tested for compressive and flexural strength. To ensure sufficient sample materials were available for casting, raw materials were converted into technical materials.
In order to achieve proper workability, a polycarboxylate-ether-based superplasticizer was incorporated into the mortar mixtures. Additionally, the water/solid ratio was adjusted to 0.9 to ensure optimal workability. Once cast, mortars were de-molded after a 24-hour period and cured in a climate chamber before testing.
X-ray diffraction and thermogravimetric analyses were conducted to quantify factors such as crystalline phases and analyze and categorize exhaust gases during testing.
Study Observations and Conclusions
The study found that alumina and carbonates prevented Mg(OH)2 precipitation and favored hydrotalcite and M-(A-)S-H formation. Early consumption of MgO was decreased by higher aluminum contents, favoring hydrotalcite formation and AlO(OH) non-reaction and the formation of Al(OH)3.
Amongst the samples analyzed by the authors, the AMS sample (which contains an Mg/Si ratio of 1.5 and Al/Si ratio of 1) exhibited the highest compressive strength. The AMS sample contains an intermediate amount of alumina and no hydromagnesite.
Central to the sample’s high compressive strength is the reaction between MgO and metakaolin, which produces M-(A-)-S-H and hydrotalcite. However, increased alumina content produces no marked improvement in mechanical properties, leading instead to the formation of higher amorphous Al(OH)3 content.
Another key conclusion of the research is that reducing the water/solid ratio would achieve mortars with higher compressive strength. Optimizing the content and type of superplasticizer could reduce this value and enhance the mechanical performance of cement incorporating these alternative binders.
The authors have noted that further investigations are needed to fully understand the benefits of these mortar mixtures and how carbonates and alumina affect the system, especially in relation to the stability of the resulting alumina-silica-carbonate-magnesium system, which adds complexity to the binder.
More from AZoBuild: Calcium Carbonate Concrete: Building on Recycling
References and Further Reading
Bernard, E et al. (2023) Effect of aluminate and carbonate in magnesia silicate cement Concrete and Concrete Composites 139, 105010 [online] sciencedirect.com. Available at:
https://www.sciencedirect.com/science/article/pii/S095894652300084
Disclaimer: The views expressed here are those of the author expressed in their private capacity and do not necessarily represent the views of AZoM.com Limited T/A AZoNetwork the owner and operator of this website. This disclaimer forms part of the Terms and conditions of use of this website.