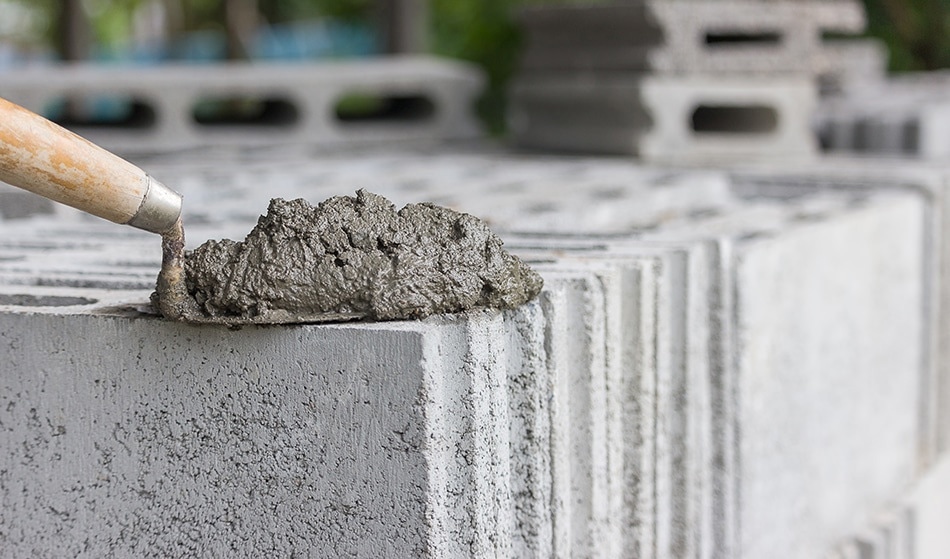
Image Credits: okcm/shutterstock.com
Hydraulic cements are the proper name for the binding agents used in concretes and most mortars. They are so-called because they interact with water to produce a hydrated gel of the calcium-, silica- and aluminate-containing mineral mix that comprises cement. This reaction produces the strength and durability of cement.
Hydraulic cements are broadly divided into inherently hydraulic cements, which set when reacted with an excess of water, and pozzolanic cements, which are siliceous and must be mixed with hydrated lime.
Types of Cement
Hydraulic lime
This is a niche product, and refers to lime-containing mostly calcined pozzolanic clay-rich limestone, with free lime, which forms the active constituent in natural cements.
Natural cements
Also called Roman cements, these consist of argillaceous limestone (“cement rock”). The quality may depend on the presence of other ingredients in the local limestone which enhance cementing properties. These were prominent before the introduction of Portland cement and faded out subsequently.
Portland cement
This artificial cement is preferred for its standardized properties, achieved by mixing multiple raw ingredients in a uniform composition and holding them at much higher temperatures than with natural cements. It comprises Portland cement clinker finely inter-ground with a small percentage of gypsum or another form of calcium sulfate, at up to 5% ground limestone. The final properties may be fine-tuned by changing the mix, physical characteristics, and temperature.
Types of Portland cement
These are classified as:
- Type I or general use or ordinary Portland cement or (in Europe) Portland cement CEM I: this is
the cement most commonly used throughout the world in civil engineering, and building works.It makes versatile, durable and forgiving concretes and mortars, but is the least sustainable type of cement.
- Type II or general use Portland cement with moderate sulfate resistance and heat of hydration
- Type III or high early strength (rapid-hardening) Portland cement
- Type IV or Portland cement with low heat of hydration
- Type V or high sulfate-resistant Portland cement
Types I, II, and III may have air-entraining agents added to them, to incorporate tiny bubbles which confer freeze-thaw resistance.
Hybrids such as Type I/II meet the specifications of more than one type.
Factory-made composite cements
As used here, the expression 'factory-made composite cements' means any cement that comprises Portland cement clinker (usually Type I) inter-ground with 5% to 30% of one or more additional inorganic constituents (power station fly ash, blast furnace slag and/or limestone), plus gypsum.
The British/European standard for common cements, BS EN 197-1, classifies factory-made composite cements into CEM II - V, or any 'non-CEM I' cement specified in the standard.
Two of these, CEM II/M and CEM V, include the word 'composite' in their names. In general, these cements, when used appropriately, perform as well as CEM I cement and with better strength under certain conditions.
Blended cements resist chemicals, are denser, with enhanced flux and reduced heat of hydration, and have comparable strength. Most blended cements today are not factory-made, but blended by cement/concrete production companies.
In the ASTM C-595, blended cements are classified as:
- Portland blast furnace slag cement (IS) with 25%–70% slag, for general purpose uses, subcategorized as; type IS (MS) which is moderately sulfate-resistant, type IS (A) which contains air bubbles when placed, and type IS (MH) that has moderate hydration heat.
- Portland-pozzolan cement based on Portland or IS cement, plus 15%–40% pozzolans of unspecified type. Two types are distinguished: types IP and P, for general use, with subtypes IP (MS), IP (A), and IP (MH) as before; and type P with less early strength, with the same subcategories, plus type P (LH) with low hydration heat.
- Portland-limestone cement or type IL
- Ternary blended cement or type IT
Blended cements with special performance characteristics include:
- Pozzolan-modified Portland cement or I (PM) based on Portland cement and <15% pozzolans, for general use, modified as types I(PM)(MS), I(PM)(A); and I(PM)(MH).
- Slag-modified Portland cement or I (SM), with < 25% slag, for general use, and the same modifiers as before (types I(SM)(MS), I(SM)(A), and I(SM)(MH)).
- Slag cement or type S, containing 70% or more of slag, and with air entrainers, used to make concrete with Portland cement, or a pozzolan-lime cement (mortar) with lime. In the US, slag cement means unblended 100% granulated blast furnace slag used in concrete as a cementitious additive or part-replacement for Portland cement, like IS or I (SM) cements.
Factory-made composite cements can be substituted for CEM I cements in masonry mortars on a 1:1 basis .
Sulfate-resisting cements
Sulfate-resisting Portland cement (SRPC), conforming to BS 4027, is a CEM I cement with a high iron oxide content and low mineral phase, making it low-alkali and sulfate-resistant. It is no longer manufactured in the UK due to its high clinker content. This category includes CEM II/B-V type of Portland-fly ash cement with 25% or more fly ash.
Rapid-hardening Portland cements
Rapid-hardening CEM I cements have smaller particles and faster strength gain than ordinary CEM I. it produces more early heat, suitable for colder climates, and is used mostly for precast concrete units, ensuring rapid reuse of molds and formwork.
Rapid-setting and extra-rapid hardening cements are mixtures of CEM I and a non-Portland cement such as calcium aluminate or calcium sulfoaluminate.
White cement
White cement is CEM I typically made from pure chalk and white clay (kaolin) containing very small quantities of iron oxides and manganese oxides. It is used mainly for architectural details exposed to the eye.
Masonry cements
Masonry cements are used for low-strength applications like bricklaying, block laying, rendering, and plastering work. They contain Portland cement CEM I plus 6% to 35% limestone or hydrated lime - properly called Portland-lime cements. Masonry cements produce workable, cohesive mortars that resist freeze/thaw. Another type is plastic cement with <12% additives such as air-entraining plasticizers.
Expansive cements
Most concretes shrink as they dry out. Expansive cements are typically mixtures of Portland and calcium sulfoaluminate clinker, optimized for gypsum content, and retain or enhance their volume.
Environmental cements
In principle, environmental cements are of two types: those that treat and encapsulate environmental residues (contaminated soils, sludges, and wastes), and those that reduce environmental impact (eco-cements/low energy/low carbon cements) by less energy usage, use of recycled materials, and/or lower emissions.
Non-Portland cements
These products have less embodied energy and a smaller 'carbon footprint’, making them more sustainable. Their potential depends on local material availability. Niche products include calcium aluminate cement (high alumina) for refractory or rapid-hardening cements, magnesium oxychloride cement for flooring, and magnesium phosphate cement for rapid repair of roads and airport runways.
ASTM C-1157 cement classification
ASTM C-1157 is a performance-based classification:
- Type GU: general use cement (performs like Type I in ASTM C-150)
- Type HE: high early strength cement (like Type III)
- Type MS: moderate sulfate resistance (like Type II)
- Type HS: high sulfate resistance (like Type V)
- Type MH: moderate heat of hydration (like Type II)
- Type LH: low heat of hydration (like Type IV)
Option R is added if they are not alkali-reactive.
Sources and Further Reading
This article was updated on the 19th August, 2019.