The construction industry is under growing pressure to keep building while dramatically reducing its environmental impact. As one of the largest consumers of raw materials and producers of waste, it can no longer rely on the traditional “take-make-dispose” model that treats buildings as temporary products and materials as expendable.
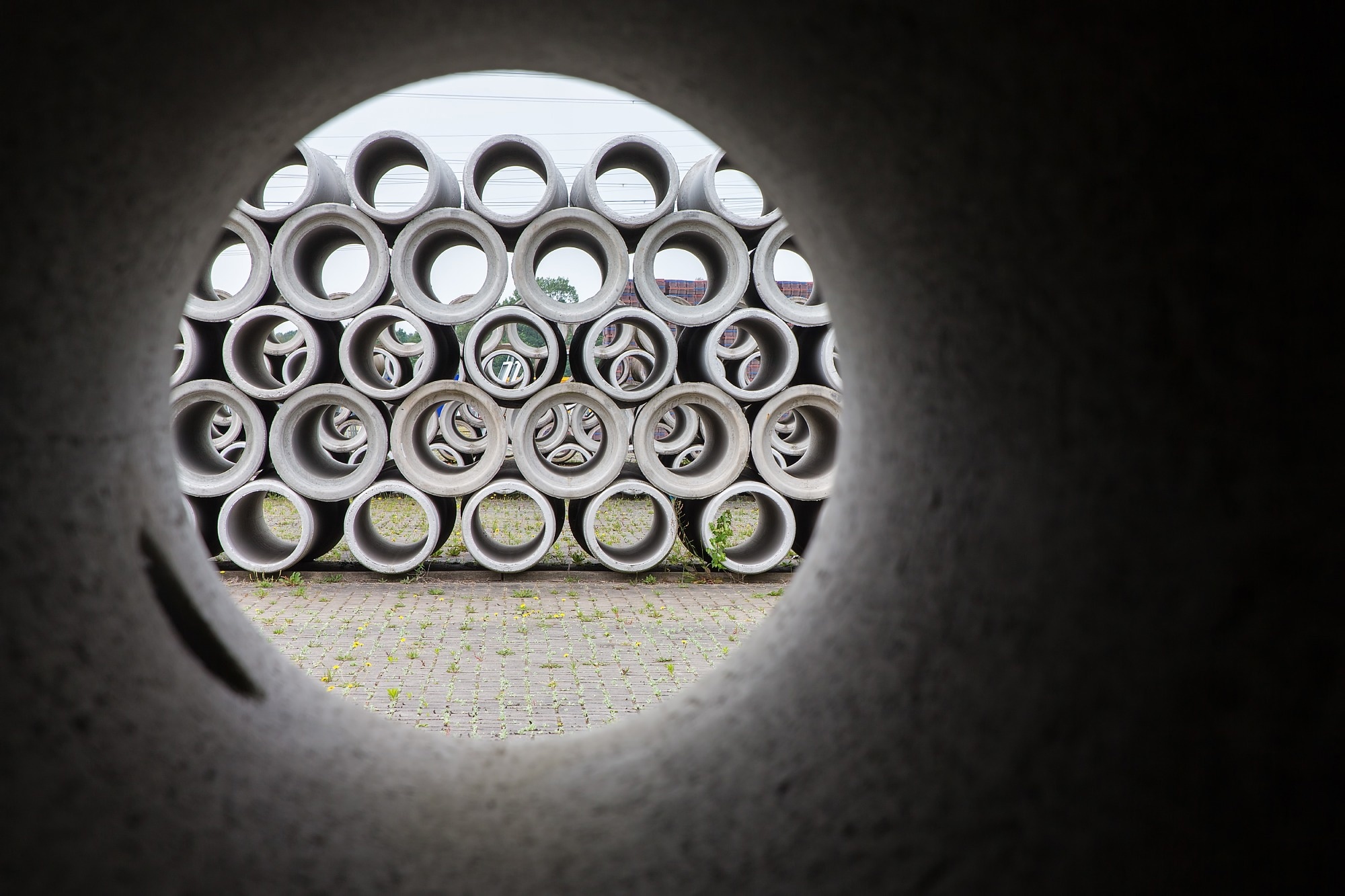
Image Credit: Ben Schonewille/Shutterstock.com
Circular construction offers a more sustainable alternative; an approach that reimagines how buildings are designed, used, and eventually deconstructed. It focuses on keeping materials in use for as long as possible, designing structures that can be adapted over time, and viewing buildings not as endpoints but as part of a continuous resource cycle.1,2
This article looks at the foundations of circular construction, from the guiding principles and frameworks behind it to the strategies, tools, and challenges involved in making it a standard part of how we build.
Download your PDF copy now!
Principles of Circular Construction
Circular construction is rooted in the broader idea of the circular economy, which aims to keep materials circulating within the system rather than allowing them to become waste. Instead of a linear process, this approach encourages regenerative, closed-loop models where buildings are designed to be both durable and flexible.1,2,3
- Design for Disassembly and Adaptability: Buildings should be created with future change in mind—able to be reconfigured, taken apart, and reused. That means using modular components, reversible connections, and clear documentation.4
- Prolonging Material Lifespan: Choosing robust materials and construction techniques that extend usability helps reduce demand for new resources and lowers embodied carbon across a building’s life.1
- Closed Resource Loops: Materials from demolition and surplus can be reintegrated into new projects, minimizing extraction and waste.3,5
- Ecosystem Thinking: Circular design also considers how buildings interact with energy, water, and natural systems, aiming to reduce environmental impact throughout.1,2
Together, these strategies shift the role of buildings from being disposable to being long-term contributors to future construction.
Core Frameworks and Models
Several models help apply circular economy principles to construction. One widely used guide is the 9R framework—Refuse, Rethink, Reduce, Reuse, Repair, Refurbish, Remanufacture, Repurpose, and Recycle. It encourages addressing material use as early in the process as possible, with recycling seen as a last resort.3,5 This hierarchy emphasizes prevention over correction, prioritizing smarter design and reduced consumption rather than relying on downstream solutions that require more energy and processing.
Research has also identified three main areas where innovation is driving circularity in construction:1
- Circular Product: Focuses on components and materials that are durable, repairable, and reusable.
- Circular Process: Involves efficient planning across the entire building lifecycle, using lean methods and lifecycle thinking to reduce resource use.
- Circular Platform: Emphasizes digital tools—like BIM and material passports—that improve coordination and transparency across stakeholders.
These areas work together to support systemic change. It’s no longer just about using better materials; it's now more focused on reform in terms of how information flows and decisions are made across the project lifecycle.1
Newer techniques like multi-criteria decision analysis (MCDA) are being used to evaluate how circular a building really is. These tools help compare different design options based on factors like ease of disassembly, recycled content, and maintenance needs.6
Implementation Strategies and Tools
Turning circular principles into action requires both smart design choices and the right tools. One of the most practical steps is creating material passports—digital records that track where a product comes from, what it’s made of, and how it can be reused. These passports make it easier to recover and redeploy materials across future projects.2,4
Modular design also plays a central role, enabling buildings to be assembled in ways that simplify future changes or disassembly. Paired with digital tools like Building Information Modeling (BIM) and digital twins, teams can better plan, track, and manage materials across the entire building lifecycle.1,7 BIM helps teams visualize and coordinate building components in 3D, while digital twins create real-time, data-driven models of structures in use, enabling better planning for maintenance, adaptation, and end-of-life recovery.
Lifecycle assessments (LCAs) are also key when it comes to helping designers understand and reduce environmental impact from early-stage planning through operation and eventual decommissioning. Combined with lean construction, which aims to cut waste and increase value, these strategies form the basis of a more circular project delivery model.2,5
Systemic Barriers and Policy Implications
Despite the momentum and innovation in circular construction, implementation remains slow. A major challenge is the fragmented nature of the construction sector, which makes coordinated action difficult. The industry's conservative culture resists changes, especially with new business models that require manufacturers to take responsibility for products over their entire life cycles.1,8
Additionally, existing policies, incentives, and certification schemes for circular practices are inconsistent. Many governments lack regulations that support waste reduction. Other barriers include limited data on materials, high upfront costs for circular designs, regulatory issues surrounding material reuse, and inadequate infrastructure for waste collection and processing.8
To address these challenges, researchers argue that governments should introduce more supportive policies, tax incentives, and legal frameworks, as well as invest in education and training to build sectoral capacity. Interdisciplinary research, pilot projects, and high-profile demonstration buildings are also advocated as ways to reduce risks and inspire widespread adoption.8
Future Prospects and Conclusion
The next phase of circular construction depends on better data, stronger collaboration, and the integration of digital technologies. As platforms evolve to link material databases with project planning, the ability to track, manage, and reuse components will become easier and more cost-effective.1,7,9
There’s also momentum around AI-driven tools that can recommend low-impact materials and optimize reuse strategies. At the same time, researchers and industry leaders are working to refine certification systems, align design standards, and improve infrastructure to handle end-of-life materials more efficiently.
For circular construction to become the norm, the industry must move beyond isolated initiatives and toward coordinated, system-wide change. This could mean shared material databases, standardized design protocols, joint ownership models for building components, and procurement policies that favor circular-ready products. That means aligning goals, sharing data, and rethinking how we define value—not just in economic terms, but in environmental and social ones too.8,9
By treating buildings as part of an ongoing material ecosystem rather than a one-off product, circular construction opens the door to a built environment that’s more resilient, resource-efficient, and ready for the future.
Looking to Learn More?
Curious about what’s next in sustainable construction? Explore topics like digital twins, embodied carbon tracking, or circularity in public infrastructure to see how these ideas are shaping the future of the built environment.
Download your PDF copy now!
References and Further Reading
- Gasparri, E. et al. (2023). Circular economy in construction: A systematic review of knowledge gaps towards a novel research framework. Frontiers in Built Environment, 9, 1239757. DOI:10.3389/fbuil.2023.1239757. https://www.frontiersin.org/journals/built-environment/articles/10.3389/fbuil.2023.1239757/full
- Rao, P. A. et al. (2025). Adopting circular economy in construction: A review. Frontiers in Built Environment, 11, 1519219. DOI:10.3389/fbuil.2025.1519219. https://www.frontiersin.org/journals/built-environment/articles/10.3389/fbuil.2025.1519219/full
- Paredes, R. (2024). Circular Construction for Eco-Building. SafetyCulture. https://safetyculture.com/topics/circular-construction/
- The circular design of buildings. European Circular Economy Stakeholder Platform. https://circulareconomy.europa.eu/platform/en/toolkits-guidelines/circular-design-buildings
- Jegen, P., Gast, L., & Faulstich, M. (2025). A review of the implementation of R-imperatives in circular construction. Cleaner Production Letters, 8, 100097. DOI:10.1016/j.clpl.2025.100097. https://www.sciencedirect.com/science/article/pii/S2666791625000065
- Abadi, M., & Moore, D. R. (2022). Selection of Circular Proposals in Building Projects: An MCDM Model for Lifecycle Circularity Assessments Using AHP. Buildings, 12(8), 1110. DOI:10.3390/buildings12081110. https://www.mdpi.com/2075-5309/12/8/1110
- Innovative digital approaches in circular construction for a sustainable tomorrow. (2023). PlanRadar. https://www.planradar.com/ae-en/innovative-digital-solutions-circular-construction/
- Metinal, Y. B., & Gumusburun Ayalp, G. (2025). Uncovering Barriers to Circular Construction: A Global Scientometric Review and Future Research Agenda. Sustainability, 17(4), 1381. DOI:10.3390/su17041381. https://www.mdpi.com/2071-1050/17/4/1381
- How can we realize a digitally controlled circular construction? (2024). BUILD UP. https://build-up.ec.europa.eu/en/news-and-events/news/how-can-we-realize-digitally-controlled-circular-construction
Disclaimer: The views expressed here are those of the author expressed in their private capacity and do not necessarily represent the views of AZoM.com Limited T/A AZoNetwork the owner and operator of this website. This disclaimer forms part of the Terms and conditions of use of this website.