A recent article in Scientific Reports looks at how gold ore tailings (GOTs) and recycled coarse aggregates (RCAs) can be used as substitutes for river sand (RS) in geopolymer concrete (GPC). The study focused on how durable this type of concrete is, especially when exposed to sulfates and chlorides.
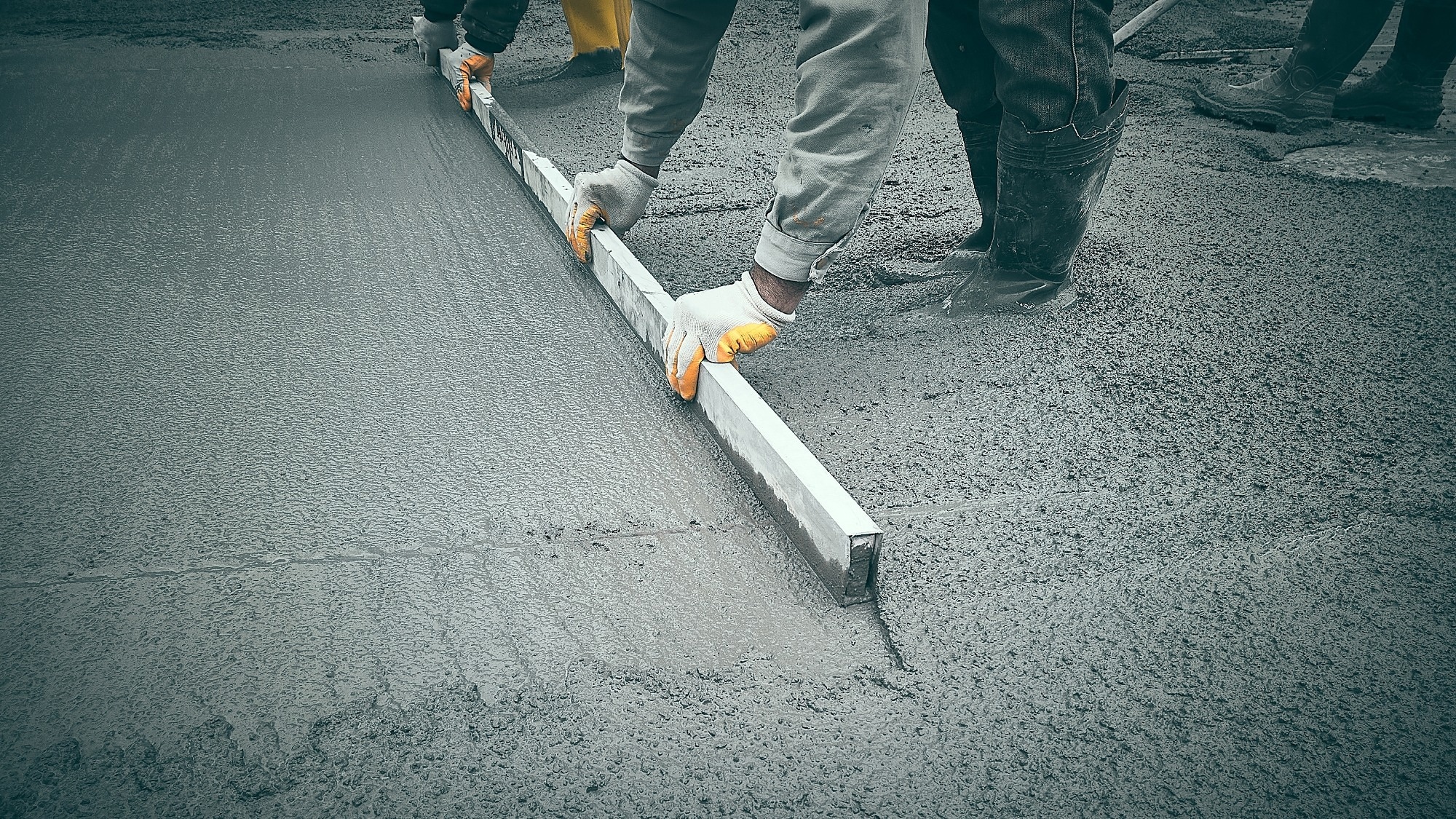
Image Credit: phil_berry/Shutterstock.com
Background
Mining and construction are two of the biggest sources of industrial waste. These materials can cause serious environmental problems, including soil contamination and acid mine drainage. Waste from mining, such as zinc, copper, and gold tailings, can be especially harmful if not managed properly.
In India, the gold mining industry produces around 1.5 million tons of GOTs each year, much of which has gone unused. GOTs contain high amounts of silica and alumina, making them a potential raw material in construction, including for bricks, tiles, and more recently, concrete.
Previous studies have looked at using GOTs in various forms of concrete, including geopolymer mortar. However, their use as a fine material in GPC made with RCAs hasn’t been explored much. This study aimed to fill that gap by evaluating the durability of GPC made with both GOTs and RCAs.
Methods
The researchers collected GOTs from gold mines in southern India. Old concrete cubes were crushed and used as RCAs. River sand, a standard fine aggregate, was also included for comparison. Fly ash (Class F) was used as the main binder, with ground granulated blast furnace slag (GGBFS) added to speed up setting time.
The chemical makeup of the GOTs, fly ash, and slag was analyzed using X-ray fluorescence. Their surface structures were examined using field emission scanning electron microscopy.
GOTs, RCAs, RS, fly ash, and GGBFS were mixed with an alkaline solution to form a uniform blend. A total of 21 concrete cube samples were made for durability testing.
In these mixes, aggregates made up about 75–80 % of the concrete by weight. Of the total aggregate portion, 30 % was river sand and 70 % was recycled coarse aggregates. In some mixes, 15 % of the sand was replaced by GOTs. Also, 30 % of the fly ash was replaced by GGBFS. For comparison, conventional concrete (CC) samples were also prepared.
Three tests were used to assess durability: resistance to 5 % magnesium sulfate (sulfate attack), resistance to chloride penetration (via rapid chloride permeability and bulk diffusion tests), and leachability testing to detect heavy metals.
Results and Discussion
In the sulfate test, carried out at intervals up to 365 days, GPC samples gained strength and weight during the first 180 days. After that, both properties declined. This drop after prolonged exposure was more significant in GPC than in the conventional concrete.
The main reason was that magnesium–silicate–hydrate compounds formed during sulfate exposure expanded, creating cracks in the GPC. These cracks reduced both strength and weight over time. The breakdown of certain hydration products also contributed to this deterioration after the 180-day mark.
The chloride penetration test, using 3 % sodium chloride over 35 days, showed that GPC allowed less chloride to pass through than conventional concrete. This was due to lower diffusion rates in GPC, which can help protect steel reinforcements from corrosion.
A leachability test was also done to check for toxic elements in the GOTs and GPC. The fluid extracts were tested using inductively coupled plasma analysis. GOTs contained high levels of arsenic (As), zinc (Zn), iron (Fe), and mercury (Hg), which are considered hazardous. However, during the geopolymerization process, these metals were locked into the concrete matrix and no longer posed a risk. Cyanide levels were also measured and found to be within safe limits.
Download your PDF copy now!
Conclusion
This study showed that GOTs can be used to make geopolymer concrete with good durability. The raw materials met the standards set by the Bureau of Indian Standards. GOTs replaced part of the river sand in the mixes without causing major performance issues.
Compared to conventional concrete, the GPC samples performed better in terms of resistance to chemicals like sulfates and chlorides. Even though GOTs contained high levels of toxic metals, these were successfully immobilized during the concrete-making process.
Using GOTs in concrete reduces the demand for natural resources and helps lower carbon emissions. With the right additives, GOTs could potentially replace all of the river sand in concrete production and be used in various types of concrete, including lightweight, ultra-high-performance, and self-compacting mixes.
Journal Reference
Lokesha, E. B., Aruna, M., & Reddy, S. K. (2025). Durability characteristics of geopolymer concrete produced using gold ore tailings along with recycled coarse aggregates. Scientific Reports, 15(1). DOI: 10.1038/s41598-025-97056-6, https://www.nature.com/articles/s41598-025-97056-6
Disclaimer: The views expressed here are those of the author expressed in their private capacity and do not necessarily represent the views of AZoM.com Limited T/A AZoNetwork the owner and operator of this website. This disclaimer forms part of the Terms and conditions of use of this website.